Papers by Jyotsna Dutta Majumdar
In the present study, the mechanical properties in terms of nano and microhardness and compressiv... more In the present study, the mechanical properties in terms of nano and microhardness and compressive strength of aluminium cenosphere composite foam (CF) developed by powder metallurgy route was carried out. The CF was developed under a varied compaction pressure between 125 MPa and 375 MPa, and sintered by two step sintering (step 1: heating at 400 ºC for 1 hrs. and step 2: heating at 700ºC for 2 hrs.) with a cenosphere content varying from 5 vol.% to 50 vol.%. The effect of process parameters and cenosphere content on microstructure, porosity and its distribution, microhardness and nano mechanical properties was undertaken. Finally, the compressive behavior of the Al-cenosphere composite foam processed under varied compaction pressure and with varied cenosphere content was evaluated.
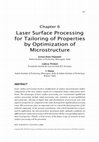
Laser surface processing involves modification of surface microstructure and/or composition of th... more Laser surface processing involves modification of surface microstructure and/or composition of the near surface region of a component using a high power laser beam. The advantages of laser surface processing over conventional equilibrium surface processing include rapid processing rate, retention of non-equilibrium microstructure, alloying in liquid state and development of processed zone with superior properties as compared to the same developed by equilibrium processing route. Microstructure plays an important role to control the final properties of the tailored component. In the present contribution, with a brief introduction to laser, and its application, the microstructures developed under optimum conditions by different laser surface processing will be discussed with the corresponding improvement in properties. Finally, a brief review of the future scope of research in laser surface processing will be presented. Jyotsna Dutta Majumdar Indian Institute of Technology Kharagpur, ...

The microstructure, the wear and corrosion behavior of WC-CoCr coatings, deposited on mild steel ... more The microstructure, the wear and corrosion behavior of WC-CoCr coatings, deposited on mild steel substrate by High Velocity Oxygen-Fuel (HVOF) flame-spraying, were examined as a function of oxygen flow ratio, standoff distance and powder feed rate during the deposition process. It is observed that the surface roughness, micro hardness and fretting wear of the coated film depends on the stand off distance at a constant power feed rate. At elevated stand off distance the surface roughness increases while the micro-hardness decreases. Fretting wear study shows the applicability of the coating whereas potentio-dynamics scanning reveals the corrosion property as well as the possible galvanic coupling effects between the substrate and the coating. A crude statistical model is proposed where the process parameters have been varied using a 2 k factorial experimental design and it is constituted of two types of variables: responses (Roughness) and factors (stand off distance, fuel/oxygen rat...
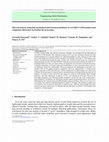
Engineering Solid Mechanics, 2021
A 100% overlap double pass friction stir process technique was developed for the fabrication of A... more A 100% overlap double pass friction stir process technique was developed for the fabrication of AA1100/17-4 PH stainless steel composites, using an H13 tool steel cylindrical threaded pin with shoulder diameter of 21 mm, pin diameter of 7 mm and pin height of 5 mm. Grooves of 2 mm width and 3.5 mm depth were machined on the 6 mm thick AA1100 plate, where the 17-4 PH stainless steel powder was packed and compacted using a pinless tool. Friction stir processing was conducted at rotational speeds of 2100, 2450 and 2800 rpm, while the travel speed of 20 mm/min, tilt angle of 2.5° and plunge depth of 0.2 mm, were kept constant. Investigations were carried out on the microstructure, elemental composition, and tensile testing and microhardness as well as structural analysis using X-ray diffraction. Defect-free micrographs with good mechanical and metallurgical connections were obtained from all the employed process parameters. However, agglomeration of reinforcements became noticeable at 2...
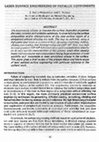
The engineering solution to improve the surface dependent properties like wear, corrosion and oxi... more The engineering solution to improve the surface dependent properties like wear, corrosion and oxidation resistance involves tailoring the surface composition and/or microstructure of the near-surface region of a component without affecting the bulk. This may be achieved, using a high power laser beam as a source of heat, by surface hardening, melting, alloying and cladding. Fast heating/cooling rate (104-1011 K/s), very high thermal gradient (106-108 K/m) and ultra-rapid reso/idification velocity (1-30 m/s) are the characteristics of this process which often develop exotic microstructures and compositions having large extension of solid solubility and metastable or even amorphous phases in the surface. This paper gives a brief review of the present status and future scope of laser assisted surface engineering with particular reference to the authors' work. INTRODUCTION Failure of engineering materials due to corrosion , oxidation, friction , fatigue and wear/abrasion is most lik...
The present work aims at understanding the effect of process parameters on the porosity and formi... more The present work aims at understanding the effect of process parameters on the porosity and forming route. A detailed investigation of the microporosity and nano have been undertaken through microcomputer tomography (µ respectively. The µ maximum of CF have been by nanoindentation analysis and compared with commercially pure (CP) aluminium. The sphericity results of the foam show that the pores are near spherical (with a sph diameter is below 50 µm, beyond which, the sphericity index decreases (0.175 to 0.4). The results of nanoindentation (for CP aluminium) to 673±54 MPa and energy absorption from 86±10 however; it decreases the elastic modulus from 58±3 (for CP
Proceedings of the National Academy of Sciences, India Section A: Physical Sciences, 2018
Ceramics International, 2017
Publisher: Elsevier NOTICE: this is the author's version of a work that was accepted for publicat... more Publisher: Elsevier NOTICE: this is the author's version of a work that was accepted for publication in Ceramics International. Changes resulting from the publishing process, such as peer review, editing, corrections, structural formatting, and other quality control mechanisms may not be reflected in this document. Changes may have been made to this work since it was submitted for publication. A definitive version was subsequently published in Ceramics International, [(in press), (2017)]
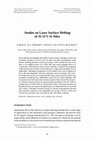
Lasers in Engineering
In the present investigation the effect of laser surface melting on wear and corrosion resistance... more In the present investigation the effect of laser surface melting on wear and corrosion resistance of Al-11 wt.% Si alloy has been investigated. Laser surface melting has been carried out using a 2 kW continuous wave CO 2 laser at an applied power of 2.3 kW and scan speed ranging from 6 to 12 mm/min. Following the laser surface melting, a detailed investigation of the melted zone in terms of microstructure, composition and phases were undertaken. Mechanical properties of the melted zone were evaluated so far as the microhardness and wear resistance were concerned. The corrosion behaviour of the as-received and the laser surface melted surface was evaluated in 1(M) H 2 SO 4 , 1(M) HNO 3 and 3.56 wt.% NaCl solutions. The microstructure of the melt zone consists of grain refined Al and Al-Si eutectic colonies which results in an improved microhardness from 87 VHN as compared to 55 VHN of the as-received Al-Si alloy. The wear resistance of the melt surface was improved significantly as compared to the as-received Al-Si alloy. A detailed corrosion study in various environments showed that corrosion resistance was marginally less in the 3.56 wt.% NaCl and 1 M H 2 SO 4 solutions, but was better in the 1 M HNO 3 solution.
The present study concerns the generation of a wear resistant Stellite 6 CO 2 laser clad layer on... more The present study concerns the generation of a wear resistant Stellite 6 CO 2 laser clad layer on the surface of an EN19 steel substrate by means of laser surface cladding. Laser surface cladding was carried out by melting the Stellite powder (particle size 10 to 40 µm) supplied through a pneumatically driven powder delivery system (using a 4 MP powder unit) with a 9 kW continuous wave (CW) CO 2 laser with the wavelength 10.6 µm. The microstructure of the clad layer was found to consist of three zones: a clad layer comprised of dendrites of Stellite 6; an alloyed zone comprised of a cellular microstructure, which was a mixture of Fe and Co; and the heat affected zone (HAZ), which was a mixture of pearlite and martensite. Compared to the EN19 steel substrate, the micro-hardness of the clad layer represented a significant improvement, increasing to 1200 VHN.
Journal of the Southern African Institute of Mining and Metallurgy, 2015
Laser surface alloying was used to develop copper and molybdenum aluminides by injecting premixed... more Laser surface alloying was used to develop copper and molybdenum aluminides by injecting premixed copper and molybdenum powder particles into a laser-generated melt pool on an aluminium substrate. Different laser processing parameters were used to produce the composite thin layers on the substrate material. The microstructure and phase constituents of the composite layer were studied by means of scanning electron microscopy (SEM), energy dispersive spectroscopy (EDS), and Xray diffraction (XRD) techniques. Experimental results show that the matrix structure of the metal matrix composite layer consists of θ-CuAl 2 and MoAl 5. Surface hardness was increased by a factor of 3.
Surface Review and Letters, 2007
The present study aims at enhancing the wear resistance and biocompatibility of Ti -6 Al -4 V by ... more The present study aims at enhancing the wear resistance and biocompatibility of Ti -6 Al -4 V by forming a thin layer of oxide. Surface oxidation has been carried out by controlled heating of the surface of Ti -6 Al -4 V substrate in air at the temperature ranging from 400–600°C and time from 25–60 h. The phase formed under thermal oxidation was predominantly the rutile and anatase phase. The thickness of the oxide layer varied from 1.5–7.0 μm. The microhardness on the surface was significantly improved as compared to the as-received substrate. Both the corrosion resistance property and biocompatibility were improved.
Surface Review and Letters, 2007
The present study aims at enhancing the wear resistance of Ti –6 Al –4 V by laser surface nitridi... more The present study aims at enhancing the wear resistance of Ti –6 Al –4 V by laser surface nitriding. Laser surface treatment has been carried out by melting of the sand blasted Ti –6 Al –4 V substrate using a high power continuous wave Diode laser with nitrogen as shrouding environment (at a gas flow rate of 51/min). Laser surface nitriding led to formation of dendrites of titanium nitrides. The microhardness is improved to a maximum of 900–950 VHN (Vickers hardness number) in laser surface nitriding as compared to 260 VHN of the as-received substrate. Surface nitriding increased primary potential for pit formation (Epp1) as compared to Ti –6 Al –4 V . Biocompatibility behavior showed a better cell viability due to surface nitriding as compared to the as-received Ti –6 Al –4 V .
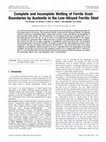
Journal of Materials Engineering and Performance, 2012
Low-carbon low-alloyed ferritic steels are the main material for the production of high-strength ... more Low-carbon low-alloyed ferritic steels are the main material for the production of high-strength pipes for the transportation of oil and gas. The formation of brittle carbide network during the lifetime of a pipeline could be a reason for a catastrophic failure. Among other reasons, it can be controlled by the morphology of grain boundary (GB) carbides. The microstructure of a low-alloyed ferritic steel containing 0.09 at.% C and small amounts of Si, Mn, Nb, Cu, Al, Ni, and Cr was studied between 300 and 900°C. The samples were annealed very long time (700 to 4000 h) in order to produce the equilibrium morphology of phases. The (a-Fe)/(a-Fe) GBs can be either completely or incompletely wetted (covered) by the c-Fe (austenite) above the temperature of eutectoid transition. The portion of (a-Fe)/(a-Fe) GBs completely wetted by c-Fe is around 90% and does not change much between 750 and 900°C. The (a-Fe)/(a-Fe) GBs can be either completely or incompletely wetted (covered) by the Fe 3 C (cementite) below the temperature of eutectoid transition. The portion of (a-Fe)/(a-Fe) GBs completely wetted by Fe 3 C changes below 680°C between 67 and 77%. The formation of the network of brittle cementite layers between ductile ferrite grains can explain the catastrophic failure of gas-and oil-pipelines after a certain lifetime.
International Materials Reviews, 2011
International Materials Reviews; ISSN: 0950-6608, Online ISSN: 1743-2804; DOI: 10.1179/1743280411... more International Materials Reviews; ISSN: 0950-6608, Online ISSN: 1743-2804; DOI: 10.1179/1743280411Y.0000000003; Volume 56, Issue 5/6, pages 341-388; ?? 2011 Institute of Materials, Minerals and Mining and ASM International ...

The International Journal of Advanced Manufacturing Technology, 2011
The development of nanostructured, hard, and wear-resistant composite coating of Al 2 O 3 , TiB 2... more The development of nanostructured, hard, and wear-resistant composite coating of Al 2 O 3 , TiB 2 , and TiN on low carbon steel (AISI 1025) substrate by combined self-propagating high-temperature synthesis (SHS) and laser surface alloying (LSA) has already been communicated in the author's previous publications. The coefficient of friction of the coating (with WC-Co as counterbody) is also found to have reduced substantially with the presence of free hexagonal boron nitride (hBN) in it. The occurrence of free hBN has been made possible by putting excess hBN in the precursor mixture which is supposed to undergo combined SHS and LSA. This has also been reported in one of the previous publications. This reduction in coefficient of friction is achieved at a cost of a marginal reduction in the microhardness as well as the specific wear rate as the free hBN in the coating matrix causes some softening. Laser posttreatment causes distinct enhancement in the microhardness and wear resistance of the coating while augmenting the favorable effect of free hBN on the coefficient of friction.
Trends in Biomaterials …, 2010
The present study aims at enhancing the biocompatibility of Ti-6Al-4V by laser surface nitriding.... more The present study aims at enhancing the biocompatibility of Ti-6Al-4V by laser surface nitriding. Laser surface nitriding has been carried out by melting of sand blasted Ti-6Al-4V substrate using a high power continuous wave DIODE laser with nitrogen as shrouding environment (at a pressure of 5 l/min). Following laser treatment, a detailed characterization of the surface has been conducted. Microhardness and biocompatibility have been evaluated. Laser surface nitriding led to formation of dendrites of TiN on the surface. The microhardness is improved to 900-950 VHN (in laser surface nitriding) as compared to 260 VHN of as-received substrate. Biocompatibility behavior showed a better cell viability in laser surface nitrided Ti-6Al-4V sample as compared to as-received one.
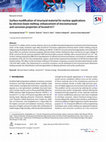
SN Applied Sciences, 2019
Inconel 617 is widely used in nuclear industry, due to its excellent elevated temperature mechani... more Inconel 617 is widely used in nuclear industry, due to its excellent elevated temperature mechanical and chemical properties. In this study, austenitic super alloy Inconel 617 has been subjected to electron beam surface melting using an indigenously developed electron beam welding unit (80 kV, 12 kW) for microstructural homogenization and understanding its effect on corrosion resistance property. Electron beam surface melting has been carried out at a gun voltage of 60 kV, current of 30 mA, and scan speed of 1000 mm/min inside a vacuum chamber with a vacuum level of 1.6 × 10 −5 mb. Surface melting induced by EBM led to development of refined microstructural features consisting of γ dendrites and precipitates of Ni 3 (Al, Ti) in the interdendritic regions, which further improved microhardness of the Electron Beam (EB) treated surface. The effect of electron beam melting on the kinetics of aqueous corrosion has been determined in acidic 3.56 wt% NaCl media. The improvement in corrosion resistance can be attributed to the microstructural refinement leading towards the redistribution and homogenization of alloying elements and surface purification.
Uploads
Papers by Jyotsna Dutta Majumdar