Papers by Dirk Van Goubergen
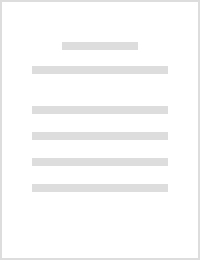
Having short changeover times is becoming more and more important in manufacturing operations. De... more Having short changeover times is becoming more and more important in manufacturing operations. Decreasing lot sizes, shorter lead times, lower inventories are all characteristics of lean production systems. A good changeover performance of the manufacturing equipment is a key enabler for this. In reality machine designs are not always made with a fast changeover capability in mind. So, production people are often forced to use IE techniques such as SMED (Single Minute Exchange of Die) to address this problem and reduce changeover times after equipment is put on the shop floor. There is clearly a need to incorporate fast changeover capabilities into the design of equipment. An initial set of guidelines has been established. However, several aspects of machine design which are primarily meant to reduce the changeover times, are also linked to the body of knowledge of Human Factors Engineering. A more HF friendly design also reduces the time and effort needed for changeovers. This paper investigates this relationship and shows this synergy.
Most publications on setup reduction are limited to describing the different 'technical' ... more Most publications on setup reduction are limited to describing the different 'technical' steps of the method with limited attention to implementation aspects. A broader approach is needed including a focus on change management. In this paper we will propose a framework that ties these different elements together in a concise and coherent approach that is broader than what currently can be found in the literature. A practical application will be shown.
Kluwer Academic Publishers eBooks, Jan 2, 2006
The ability to produce products which continue to meet changing customer expectations requires fl... more The ability to produce products which continue to meet changing customer expectations requires flexibihty within a manufacturing plant. Short setup times are a key enabler for obtaining these flexible production systems. The purpose of this research is to identify human factors issues in setup reduction and to develop a framework for assessing and improving the changeover from an ergonomics point of view. A Human Factors System Design methodology will be the starting point to identify how the existing human factors body of knowledge can be incorporated in the body of knowledge of design for fast changeover. This publication describes the first steps of this research. We identify the human factors gaps and deficiencies in the current set of design rules for fast changeover.

European Journal of Operational Research, Jun 1, 2008
The importance of ensuring short setup times in manufacturing has been well-documented in the lit... more The importance of ensuring short setup times in manufacturing has been well-documented in the literature over the past years. However, this body of work largely addresses situations involving a single machine with no specific workerrelated issues. In practice, there exist multiple machines or workstations that form a machine line, and that need setup operations to be performed by multiple workers. The existing literature does not provide adequate methodologies for setup reduction in such cases. This paper describes a quantitative modeling and algorithmic approach for scheduling activities or tasks in order to minimize the setup time in such situations, also taking into account relevant secondary objectives such as balancing the workload amongst the workers, concentrating slack toward the end of the setup process, and minimizing the movement costs of the workers performing the different setup tasks. Three real-life examples are used to demonstrate the efficacy of the proposed approach.
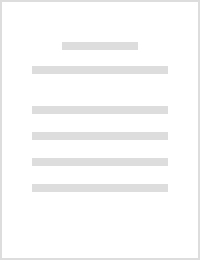
This paper describes the development of a Lean scheduling system for job shop environments for im... more This paper describes the development of a Lean scheduling system for job shop environments for improving flow. The authors introduce a cyclic scheduling system with fixed interval length and time slots, which can be represented by a ‘production wheel’ (as a variant of EPEI scheduling) . An iterative procedure to design the production wheel is proposed. Using the MSSI heuristic method, the production orders have to be scheduled on the wheel of the first machine(s) in the production chain. This heuristic minimizes the number of set-ups and the total amount of changeover time within the scheduling interval. Due to the limited number of time slots on the production wheel, it is possible to keep the total Work-In-Process (WIP) under control and consequently, also the lead times. A case study in a manufacturing facility in Belgium shows that the introduction of this scheduling system can reduce the average lead time by over 40%. This paper also explains how the production wheel can serve as a visual management tool to monitor and control the process status and progress.
Springer eBooks, Jan 25, 2008
Setup reduction is a key requirement nowadays for many lean implementations. Current setup reduct... more Setup reduction is a key requirement nowadays for many lean implementations. Current setup reduction methodologies, most of them based on Shingo's SMED, focus merely on simple one machine-one person situations, where as many value streams contain long multi-stage machine lines (e.g., in food industry) or multi-machine cells (e.g., in metal industry). In these situations, using SMED is not enough, one needs to look at reducing and optimizing all setup activities across all available persons and machines. This paper presents a comprehensive approach for these situations (MMSUR) that yields very good results and that is easy to apply with any improvement team of operators. A real life case study will be used to illustrate the approach and the results.
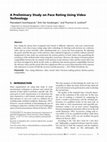
Human Factors and Ergonomics in Manufacturing & Service Industries, Jun 8, 2012
Pace rating has always been recognized and treated as difficult, subjective, and even controversi... more Pace rating has always been recognized and treated as difficult, subjective, and even controversial. Recently, a new idea of pace rating using video technology by showing work motions on a reference video and an actual (real-life) video simultaneously on a screen has been proposed. By adjusting the speed (and thus the pace) of the reference video, industrial engineers or workers without extensive background in time study can synchronize the motion patterns in both videos, thus quantifying the actual pace of the method under study using their visual sense. However, the impact of motion pattern compatibility between the two stimuli (work motions on the reference video and the actual video) has not been investigated in detail. In this study, we elaborate that motion pattern compatibility between the reference video and the actual video has a significant effect on correct determination of the response (the rated pace) in terms of both the accuracy and the precision.

The Food and Agriculture Organization estimated that one third of the world's food is wasted each... more The Food and Agriculture Organization estimated that one third of the world's food is wasted each year and that the environment and the economy are hugely impacted. Food losses refer to the decrease in edible food mass throughout the food value chain: at production, postharvest and processing stages [1]. A food loss is quantified only for products that are intended for human consumption, excluding feed and parts of products that are non-edible. The cause of food loss is twofold: technical and/or management errors. This study focuses on the food losses during the production process in an industrial setup. For example, losses may occur during washing, peeling, slicing and boiling or during process interruptions and accidental spillage. The main objective of this study is to gain access to reliable information related to food loss in the Belgian food-processing industry, by quantifying the food loss and exploring its causes within food processing companies through multiple case studies. A total of four company representatives participated in the study. The studies reveal the major data gaps on food loss, especially during the production process, and major causes of food loss within specific industries.
For the last decades many organizations started using Lean as their major business strategy for o... more For the last decades many organizations started using Lean as their major business strategy for organizing and improving their operational activities. Results in manufacturing have been very good, but nowadays also service and office environments start to realize that the Toyota Production System, which is the basis of Lean, is a universal approach. Healthcare institutions in the U.K. and the U.S.A. have already been applying lean principles to some degree. This paper describes the findings of our exploratory research on lean in service and healthcare showing how one department from the Ghent University Hospital in Belgium started to implement lean, resulting in significant performance improvements. After a brief discussion on the different elements of the Toyota Production System, we will show how they were adapted and applied in a service environment.
Pace rating has always been one of the main responsibilities for industrial engineers (IEs) when ... more Pace rating has always been one of the main responsibilities for industrial engineers (IEs) when manufacturing companies need standard times to use for planning, scheduling, cost efficiency and budget calculations. Although computer technologies have been applied to model, analyze, and visualize complex systems to help engineers solve specific issues, a simulation or visualization tool on pace rating that reveals and visualizes decision making patterns has as yet not been developed to help IEs perform worker's pace rating. This paper presents the development of a tool that can visualize response selection and execution, showing decision making patterns and help IEs to perform pace rating.
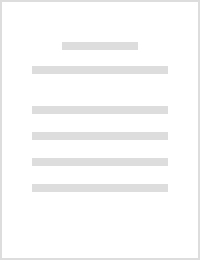
Lean manufacturing has been acknowledged as a methodology to eliminate waste, while six sigma has... more Lean manufacturing has been acknowledged as a methodology to eliminate waste, while six sigma has been regarded as a diagnostic tool to improve processes by eliminating variation. The important objective of both of the methodologies is to identify the most critical processes to generate savings for an organization. Lean sigma integrates these two methodologies into an effective hybrid method which combines the variability elimination tools from six sigma with the waste elimination methodology from lean manufacturing. Previous studies debate over the consistent result of the lean sigma methodology in the Small and Medium-sized Enterprises (SMEs) considering their implementation barriers (size, resource, skill, time). Moreover, the unique characteristics of food sector such as variability in raw material, seasonality, low self-life and complexity of the supply chain make it even more difficult to implement lean sigma methodology in the SMEs operating in the food sector. In this context, this paper aims to study the application of lean sigma methodology in a medium sized confectionary (ginger bread) producing company in Belgium. The results shows that the company successfully applied lean sigma methodology and saved a huge sum of money by reducing overfilling/overweight of final product (ginger bread). However, there are number of barriers identified during the implementation process that mainly derived from the unique characteristics of the food sector on one hand, and of SMEs on the other. This study proposes a lean sigma framework to reduce the overfill and rework. The proposed framework integrates lean tools and six sigma DMAIC methodology to reduce overfill and rework to enhance the bottom-line results. The result of this study will help food SMEs to apply lean sigma methodology to reduce variability and consequent waste in their production process. Moreover, the results on barriers of lean sigma implementation in food SMEs will paves the way for further research.
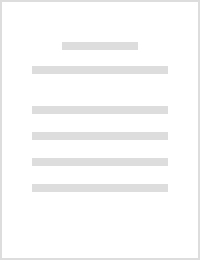
Recent literature emphasized the importance of determining factors for successful adoption of lea... more Recent literature emphasized the importance of determining factors for successful adoption of lean manufacturing in different settings. This study explored different determining factors and their impact on lean manufacturing in food processing industries in small and medium sized enterprises (SMEs). The characteristics of the food industries such as mandatory quality assurance requirements, perishability of the products and variability of raw materials obstruct a straightforward application of lean manufacturing. In addition, the challenges of “change” in SMEs are distinctive from those faced by large organization. In this context, this study explores the effect of determining factors on adoption of lean manufacturing in the food processing SMEs through multiple case studies. The nature of the process was found to be a very important factor in lean adoption. The low shelf-life of the food products and the extremely volatile demand and supply was a barriers to lean manufacturing adoption. The small size of the plant, the traditional set up and layout and the quality assurance requirements make it difficult to replicate lean in food processing SMEs. The study reconfirms that commitment of top management, culture, team work, and lack of skilled manpower impacted lean implementation.
Uploads
Papers by Dirk Van Goubergen