Papers by Arnaud Duchosal
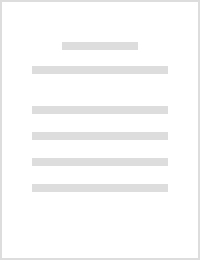
Ce travail vise a la prediction de l'apparition de la fissuration lors de reparations par sou... more Ce travail vise a la prediction de l'apparition de la fissuration lors de reparations par soudage a l'electrode enrobee, d'aciers austenitiques refractaires moules. Une modelisation du comportement thermique et mecanique ainsi que du chargement thermique du materiau lors du soudage, est proposee et la simulation thermique est validee grâce a la confrontation avec les resultats d'essais instrumentes. L'etude experimentale de la fissuration d'un acier refractaire moule a montre que les fissures se creaient et se propageaient principalement dans le reseau de carbures, present dans les zones interdendritiques qui presentent un caractere fragile, dans une matrice a comportement ductile. Des criteres macroscopiques sont proposes de maniere a localiser une zone critique, apres une operation de rechargement complete. En parallele, une " cellule ", representant un element de microstructure typique du materiau est modelisee. L'histoire thermo-mecanique de la zone critique, identifiee a l'aide des criteres macroscopiques, est appliquee dans la cellule representative de maniere a determiner a partir de quel nombre de passes la contrainte dans la cellule atteint une valeur seuil, determinee par un essai de traction in situ. Une confrontation avec l'experience permet de constater que la simulation predit l'apparition de la fissuration de facon precoce.
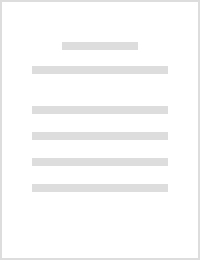
The International Journal of Advanced Manufacturing Technology, Aug 30, 2018
Multi-objective optimization is becoming an essential stage in the choice of machining parameters... more Multi-objective optimization is becoming an essential stage in the choice of machining parameters. The objective of this paper was to optimize the choice of cutting parameters in terms of cutting speed, depth of cut, and feed rate during turning process of AISI 52100 hardened steel when multiple objectives were simultaneously taken into consideration like surface roughness, consumed power, cutting time or machining cost, productivity or metal removal rate and cutting forces. The turning process in this case was in dry conditions and the selected machining parameters have been investigated using full factorial design of experiments for three parameters (cutting speed, depth of cut, and feed rate). The relationship between parameters and performance responses were developed by using multiple linear regression analysis (MLR) and first-order empirical models were obtained. Analysis of variance (ANOVA) was employed to check the validity of the developed models within the limits of the factors that were being investigated and to test the significance of the above parameters. Thus, the obtained empirical models have been used to determine the optimal machining parameters with multi-objective optimization method based on weighting factors and genetic algorithm (GA) optimization method. Finally, an industrial example demonstrating the effectiveness of the proposed methodology was presented and confirmed the values when compared to the experimental results. This methodology should help the users to obtain the optimal process parameters for their application.
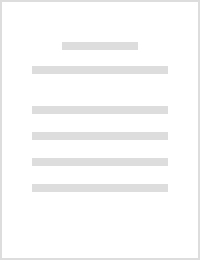
Journal of tribology, Apr 30, 2018
In this paper, the effect of compacted graphite iron (CGI) microstructure has been investigated i... more In this paper, the effect of compacted graphite iron (CGI) microstructure has been investigated in tribological strategy. From industrial context, two coatings have been chosen: a single layer coating (physical vapor deposition (PVD)) and a multilayer coating (chemical vapor deposition (CVD)). Pin-on-disk tests have been done to analyze wear mechanisms and to directly obtain the coefficient of friction. Rotation speed of the disk has been adjusted to get the same linear velocity on different disk radii to get up to 150 m min−1 similar to machining condition. Three-dimensional (3D) profilometer, scanning electron microscopy, and nano-indentation were used to observe the track profiles, the pin, and the disk wears and to measure the hardness of microstructure components, respectively. Results showed that PVD coating was more abrasive and had more volume of sticking materials. Chemical vapor deposition coating, which could be the most appropriate for machining CGI, has a real antisticking property and has less friction coefficient than PVD coating. But the presence of small TiCN precipitates in CGI material has a proven negative effect in CVD coating lifetime.
Journal of Cleaner Production, Dec 1, 2015
ABSTRACT

International Journal of Machine Tools & Manufacture, Jul 1, 2015
Pulsed ion beam treatment of materials provides an attractive alternative to pulsed laser process... more Pulsed ion beam treatment of materials provides an attractive alternative to pulsed laser processing for near surface modification of semiconductors, metals and polymers. The transfer of energy to the sample occurs by electronic and nuclear stopping over depths extending to several microns depending on ion species and voltage. A numerical code for modeling the melt and solidification behavior of materials under ion beam processing has been developed. The code and parameter extraction procedures were validated experimentally by comparing simulations with experimental measurements of the melt duration in silicon. The sensitivity of the melt behavior to variations in the beam properties was also investigated. The quiescent nature of the melt was confirmed by measurements of the diffusion of arsenic in the melt. These results demonstrate that simulations of the ion beam treatment can quantitatively match experimental results with no adjustable parameters.
HAL (Le Centre pour la Communication Scientifique Directe), Jun 22, 2005
Journal of Manufacturing Processes
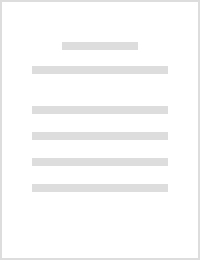
International Journal of Precision Engineering and Manufacturing-Green Technology, 2021
This work mainly focuses on the effectiveness of both rake and flank face application of the diff... more This work mainly focuses on the effectiveness of both rake and flank face application of the different metal working fluid (MWF) strategies such as liquid CO2, minimal quantity lubrication (MQL), and emulsion in face milling of Ti–6Al–4V alloy. Modified CoroMill 600 cutter via internal channels to both rake and flank faces of the inserts with PVD coated inserts were used for the studies. This novel approach of delivery of MWFs has been investigated on effective thermo-mechanical loads; in terms of the evolution of cutting temperature, cutting forces, and residual stresses. The hardness of the machined surfaces and chip microstructure analysis were also conducted to understand more about the mechanical and thermal load effects in machined material and observed parameters. It has been found that the effectiveness of both rake and flank application of the liquid CO2 machining is a better alternative for the emulsion and MQL strategies. Low thermal deformation of the material, higher magnitude of compressive residual stresses, and lower thermal load throughout the machining cycle have been observed. However, an increase in the mechanical load was observed because of the cold strength hardening of the Ti–6Al–4V workpiece at the liquid CO2 environment. These effects are negligible at room temperature after machining. Overall results show that the cryogenic machining offers best and lower thermal load effects over MQL and emulsion strategies for both rake and flank applications.
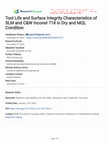
In this paper, a tool life test was performed using PVD coated insert on Inconel 718 (IN718) samp... more In this paper, a tool life test was performed using PVD coated insert on Inconel 718 (IN718) samples. The tool life was tested on IN718 workpiece fabricated through conventional (Cast & Wrought) and additive (Selective Laser Melting) process routes. The as-built SLM samples were subjected to two heat treatments such as Hot Isostatic Pressing (HIP) and Aeronautic Heat Treatment (AHT). This study aimed to evaluate the machining behavior of C&W and SLM IN718 from the machining point of view such as tool wear, chip appearance, surface roughness, and residual stresses. The tool life tests were performed under a dry and near dry environment like using Minimum Quantity Lubrication (MQL). Meanwhile, the tool wear propagation under different cutting conditions is also explored. Under both the cutting conditions flank wear and fracture of the cutting edge are the most predominant failure modes minimizing the tool life. The microhardness, surface roughness, and residual stress measurements wer...
Materials Today: Proceedings, 2021
MM Science Journal, 2021
The performance of the PVD coated carbide insert with micro-holes is experimentally compared with... more The performance of the PVD coated carbide insert with micro-holes is experimentally compared with that of the conventional inserts while machining Inconel 718 under Dry and MQL condition (Canola Oil, 0.25% Gr with Canola Oil). The machining performance of textured tool is found to be relatively good when compared to untextured tool in terms of the cutting force, surface roughness, flank wear and crater wear occurred on the cutting inserts. It is being inferred that Canola oil with 0.25% Gr-nanoparticle has improved the cutting force by 17.39%, decreased the flank wear and surface roughness by 20% and 36.23% respectively while machining with the textured tool.

Procedia CIRP, 2020
In today's business environment, the trend towards more product variety and customization is unbr... more In today's business environment, the trend towards more product variety and customization is unbroken. Due to this development, the need of agile and reconfigurable production systems emerged to cope with various products and product families. To design and optimize production systems as well as to choose the optimal product matches, product analysis methods are needed. Indeed, most of the known methods aim to analyze a product or one product family on the physical level. Different product families, however, may differ largely in terms of the number and nature of components. This fact impedes an efficient comparison and choice of appropriate product family combinations for the production system. A new methodology is proposed to analyze existing products in view of their functional and physical architecture. The aim is to cluster these products in new assembly oriented product families for the optimization of existing assembly lines and the creation of future reconfigurable assembly systems. Based on Datum Flow Chain, the physical structure of the products is analyzed. Functional subassemblies are identified, and a functional analysis is performed. Moreover, a hybrid functional and physical architecture graph (HyFPAG) is the output which depicts the similarity between product families by providing design support to both, production system planners and product designers. An illustrative example of a nail-clipper is used to explain the proposed methodology. An industrial case study on two product families of steering columns of thyssenkrupp Presta France is then carried out to give a first industrial evaluation of the proposed approach.

Procedia CIRP, 2020
In today's business environment, the trend towards more product variety and customization is unbr... more In today's business environment, the trend towards more product variety and customization is unbroken. Due to this development, the need of agile and reconfigurable production systems emerged to cope with various products and product families. To design and optimize production systems as well as to choose the optimal product matches, product analysis methods are needed. Indeed, most of the known methods aim to analyze a product or one product family on the physical level. Different product families, however, may differ largely in terms of the number and nature of components. This fact impedes an efficient comparison and choice of appropriate product family combinations for the production system. A new methodology is proposed to analyze existing products in view of their functional and physical architecture. The aim is to cluster these products in new assembly oriented product families for the optimization of existing assembly lines and the creation of future reconfigurable assembly systems. Based on Datum Flow Chain, the physical structure of the products is analyzed. Functional subassemblies are identified, and a functional analysis is performed. Moreover, a hybrid functional and physical architecture graph (HyFPAG) is the output which depicts the similarity between product families by providing design support to both, production system planners and product designers. An illustrative example of a nail-clipper is used to explain the proposed methodology. An industrial case study on two product families of steering columns of thyssenkrupp Presta France is then carried out to give a first industrial evaluation of the proposed approach.

Procedia Structural Integrity, 2019
Selective laser melting (SLM) is one of the most used additive manufacturing processes, using whi... more Selective laser melting (SLM) is one of the most used additive manufacturing processes, using which complex parts can be built with high dimensional accuracy in a flexible manner with less material usage. The aerospace industry relies on SLM technique to manufacture components like turbine and compressor blades which has a high demand in its dimensional tolerance. Inconel 718 which is a nickel based super alloy used in steam turbine, jet engines where it is subjected to high thermomechanical loads. Inconel 718 is the most preferred alloy in the above applications due to its highest strength-to-weight ratio, its excellent resistance to fatigue, creep and corrosion. Inconel 718 is mainly strengthened by the precipitates which were formed during the heat treatment process by the combination of elements like Nb, Ti and Al along with the base element Ni. In this paper microstructure analysis of as-built and heat treated samples were done along with the evaluation of its mechanical characterization. Followed by the machining test under dry and emulsion conditions using the same cutting parameters. The surface integrity evaluation were done before performing four point bending fatigue test. The fatigue fracture of the sample corresponding to number cycles to failure along with the fractographic analysis of the dry and emulsion machined samples was investigated. The fatigue crack failure is compared to each process of machining to determine the best machining condition for Inconel 718. The best machining condition is dry compared to emulsion as it gives better surface roughness, more compressive residual stress due to which dry machined samples sustained more cycles to failure.

Mechanics & Industry, 2019
The main aim of this paper was to reproduce the frictional behaviour that occurred in milling wit... more The main aim of this paper was to reproduce the frictional behaviour that occurred in milling with a pin-on-cylinder system. Three different tribological tests were conducted reproducing friction phenomenon that happened in three machining conditions: (i) dry rubbing, representing the dry machining condition, (ii) MQL applied to front face rubbing which was similar to milling with MQL applied on the insert rake face and (iii) MQL applied to rear end rubbing which was similar to milling with MQL applied on flank face. Tribological tests were carried out with coated tungsten carbide pins rubbing on X100CrMoV5 steel cylinder. Apparent coefficient of friction, adhesion area and heat flux transmitted to the pin were analysed. It has been shown that MQL rear end rubbing provided a lower adhesion area and lower apparent coefficient of friction than with MQL front face rubbing. Furthermore, MQL rear end rubbing resulted in a greater cooling ability. These findings helped to explain why bett...
MM Science Journal, 2019
Components produced and repaired by the Laser Metal Deposition (LMD) process require finishmachin... more Components produced and repaired by the Laser Metal Deposition (LMD) process require finishmachining steps in order to improve the poor geometrical tolerance of the functional surfaces. In this work, the LMD process was conducted to build up samples from Ti-6Al-4V powders. The effect of the face milling process on surface roughness of the Ti-6Al-4V parts was studied in different build directions. The effect of the heat treatment was also considered. Changes in roughness and micro-hardness were evaluated and compared in each condition. Cutting forces were also measured in order to evaluate loading characteristic on the cutting insert. The heat-treated sample shows lower cutting forces in comparison with the as-build material. Different values of the surface roughness of the machined parts were obtained as a consequence of the microstructure variation.

MM Science Journal, 2019
This study mainly focuses to investigate the machining performances of variety of metal working f... more This study mainly focuses to investigate the machining performances of variety of metal working fluid (MWF) strategies such as cryogenic (CO2), minimum quantity lubrication (MQL) and emulsion, into rake and flank face application during the face milling of titanium (Ti-6Al-4V grade 5) alloy. Modified CoroMill600 milling cutter with internal channels to inserts rake face and flank face delivery, and PVD coated inserts are used for the study. This novel approach of rake face and flank face delivery of MWF's has been evaluated on machinability of the process, in terms of surface integrity, cutting forces and chip microstructure analysis. The results show that cryogenic CO2 machining has improved surface roughness (up to 34% and 38% for Ra and Rz respectively). Additional results show that efficient cooling at liquid CO2 condition reduces the friction between workpiece and tool, confirmed by observing chip microstructure. However, the cutting force has been found to increase as a result of higher shear resistance of the material at liquid CO2 machining, with evidences from the chip microstructure analysis. Up to 9% increase in hardness of the machined surface is observed at cryogenic environment compared to non-machined, indicates the cold strength hardening of the material. The overall results imply that the cryogenic CO2 offer best surface roughness and improved friction between tool and workpiece. Even though further studies are needed for the better understanding the results in terms of hardness of the machined workpiece via optimized cryogenic flow.
Uploads
Papers by Arnaud Duchosal