Papers by Jyotsna Dutta Majumdar
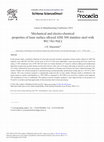
Physics Procedia, 2013
In the present study, a detailed evaluation of wear and corrosion resistance properties of laser ... more In the present study, a detailed evaluation of wear and corrosion resistance properties of laser surface alloyed of AISI 304 stainless steel with WC+Ni+NiCr (in the ratio of 70:15:15) has been undertaken. Laser processing has been carried out using a 5 kW continuous wave (CW) Nd:YAG laser (at a beam diameter of 3 mm) by surface melting and simultaneous deposition of precursor powder mixture in the melt zone (at a flow rate of 10 mg/s) and using Ar shroud at a gas flow rate of 5 l/min. Followed by laser processing, a detailed evaluation of fretting wear behavior has been conducted against WC surface. Finally, the corrosion property is measured using a potentiodynamic polarization testing unit in a 3.56 wt.% NaCl solution. The wear resistance property is significantly improved due to laser surface alloying which is attributed to the improvement in surface microhardness to 1350 VHN as compared to 220 VHN of as-received-stainless steel substrate. The mechanism of wear is established. The pitting corrosion resistance property is also improved due to the presence of Ni and Cr in solution and homogenization of microstructure due to laser processing.
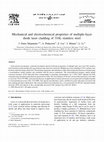
In the present investigation, a detailed mechanical and electrochemical properties of multiple-la... more In the present investigation, a detailed mechanical and electrochemical properties of multiple-layer laser clad 316L stainless steel (from the powders produced by gas atomized route) has been carried out. Multiple-layer laser cladding of 316 L stainless steel has been conducted using a diode laser. The mechanical property (microhardness) of the fabricated product has been evaluated using a microhardness testing machine and correlated with the process parameters. The electrochemical property, mainly pitting corrosion resistance of the fabricated layer corresponding to maximum microhardness (in a 3.56% NaCl solution) has been evaluated using standard potentiodynamic polarization testing. The microhardness of the laser assisted fabricated layers was found to vary from 170 to 278 VHN, increased with decrease in applied power density and increase in scan speed and was higher than that of conventionally processed 316L (155 VHN). The superior microhardness value is attributed to grain refinement associated with laser melting and rapid solidification. The critical potential to pit formation (E PP1) was measured to be 550 mV saturated calomel electrode (SCE) and superior to the conventionally processed 316L stainless steel (445 mV (SCE)).
AIJR Abstracts, Feb 6, 2021
Laser as a source of focused energy may be applied for the modification of microstructure and/or ... more Laser as a source of focused energy may be applied for the modification of microstructure and/or composition of the near surface region. The technique may be applied for the development of a ceramic/intermetallics/ interstitial compound dispersed metal matrix composite layer on the surface of metallic substrate by melting the substrate with a high power laser and simultaneous addition of alloy powders for the development of metal matrix composite layer by in-situ reactions. In the present contribution, development of metal-dispersed and intermetallic- dispersed matrix composite layer on the surface of metallic matrix has been discussed with a suitable example of its application.
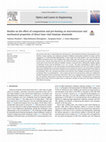
Optics and Lasers in Engineering, Aug 1, 2020
The present study aims at understanding the microstructure, and mechanical properties (micro hard... more The present study aims at understanding the microstructure, and mechanical properties (micro hardness, nanohardness, young's modulus and compressive strength) of different commercially available TiAl alloys with the composition of Ti-45Al-2Nb-2Mn-0.8B(4522XD), Ti-44Al-4.5Nb-1Mo-0.15B (TNMB-1) and Ti-47.5Al-2Nb-2Cr (GE4822) developed by direct laser cladding (DLC) using a high power Nd:YAG laser with adapted parameters for laser power, velocity and powder feed rate. DLC has been carried out by feeding the powder into the interaction zone of laser beam and substrate (GE4822), forming a melt pool which subsequently solidifies rapidly, to build bulk volumes with the dimension of 10 × 10 × 10 mm 3. The effect of preheating at 1053 K (780 °C) and shrouding environment on the characteristics and mechanical properties has also been studied in details. Direct laser cladding leads to continuous and defect free microstructures. However, the microstructures (both the morphology and grain size) were found to depend on the composition of ternary elements and to some extent on the preheating. There was a marginal coarsening of microstructure when cladding was performed by simultaneous heating. There was predominantly, and 2 phases present in the microstructure, which was confirmed by detailed transmission electron microscopic observation. There was a marginal decrease in hardness due to heating. The maximum improvement in hardness was found for the alloy 4522XD. A detailed study of compressive property showed that a maximum improvement in compressive strength was observed in alloy 4822 in both with and without pre-heating.
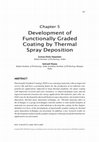
IGI Global eBooks, May 6, 2015
Functionally Gradient Coatings (FGCs) are emerging materials with an improved service life and ha... more Functionally Gradient Coatings (FGCs) are emerging materials with an improved service life and have a promising future for the production of (a) tailored components for applications subjected to large thermal gradients, (b) smart coating with improved corrosion and wear resistance, (c) improved fatigue wear, and (d) improved material structures for energy applications like batteries, fuel cells, etc. FGCs may be developed by physical/chemical vapor deposition, electro/electroless deposition, thermal spray deposition technique, etc. Thermal spraying refers to the technique or a group of techniques whereby molten or semi-molten droplets of materials are sprayed onto a solid substrate to develop the coating. In this chapter, detailed overviews of the development of functionally graded coating by thermal spray deposition techniques are presented. In addition, a few research results on the development of functionally graded coating for tribological and thermal barrier applications are presented.
Welding in The World, Mar 31, 2023
Procedia Manufacturing, 2017
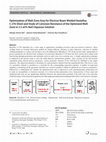
Arabian journal for science and engineering, Nov 16, 2018
Hastelloy C-276 superalloy has a wide range of applications including petroleum and petrochemical... more Hastelloy C-276 superalloy has a wide range of applications including petroleum and petrochemical industries. Since welding forms an essential fabrication method for joining different structures in these industries, selection of suitable welding parameters is a prime concern that is yet to be addressed for Hastelloy C-276. In the present study, optimization of process parameters for electron beam welding of 2.6-mm-thick Hastelloy C-276 sheet has been carried out to obtain weld bead having through-penetration and minimum weld (or melt) zone cross-sectional area. A simple optimization technique is employed in the present study to solve the multi-objective minimization problem. After carrying out the full factorial experiment using selected process parameters, various geometric elements of the weld bead are identified as the output responses. The regression equation is developed for each geometric element from the experimental data. The desired value of a geometric element is specified as a constraint for the corresponding regression equation. A number of regression equations (considering all the geometric elements) are solved in parallel to obtain an optimized set of process parameters, followed by a confirmation test. Further, the optimized melt zone is subjected to cyclic potentiodynamic polarization test to study its susceptibility to localized corrosion. It is observed that polarization curve characteristics of base metal and optimized melt zone are not significantly different; however, the repassivation potential of the melt zone is less than that of the base metal. A flowchart showing the layout of the employed optimization technique followed by corrosion test is attached.
Welding in The World, Oct 8, 2022
Transactions of the Indian National Academy of Engineering, Apr 15, 2022
INAE letters, Jun 8, 2019
This investigation aims to enhance both wear and corrosion resistance of interstitial-free (IF) s... more This investigation aims to enhance both wear and corrosion resistance of interstitial-free (IF) steel through deposition of predetermined thickness of pure Sn or Zn or alternate elemental Sn-Zn layers by twin-target magnetron sputtering at desired deposition rate. The thickness, average grain size, hardness and resistance to wear and corrosion of the deposit depend on the deposition parameters. Deposition of either Sn or Zn from single target seems more effective than that from twin target in improving these tribo-corrosion properties of IF steel. The results indicate that sputter deposition of Sn or Zn offers a superior wear and corrosion resistance to galvanized steel and can be a potential route to replace the conventional practice of hot dip galvanizing for the said objective.
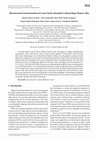
Journal of optics, Sep 21, 2020
Cu-based shape memory alloys (SMAs) present some advantages as higher transformation temperatures... more Cu-based shape memory alloys (SMAs) present some advantages as higher transformation temperatures, lower costs and are easier to process than traditional Ti-based SMAs but they also show some disadvantages as low ductility and higher tendency for intergranular cracking. Several studies have sought for a way to improve the mechanical properties of these alloys and microstructural refinement has been frequently used. It can be obtained by laser remelting treatments. The aim of the present work was to investigate the influence of the laser surface remelting on the microstructure of a Cu-11.85Al-3.2Ni-3Mn (wt%) SMA. Plates were remelted using three different laser scanning speeds, i.e. 100, 300 and 500 mm/s. The remelted regions showed a T-shape morphology with a mean thickness of 52, 29 and 23 µm and an average grain size of 30, 29 and 23µm for plates remelted using scanning speed of 100, 300 and 500 mm/s, respectively. In the plates remelted with 100 and 300 mm/s some pores were found at the root of the keyhole due to the keyhole instability. We find that the instability of keyholes becomes more pronounced for lower scanning speeds. It was not observed any preferential orientation introduced by the laser treatment.
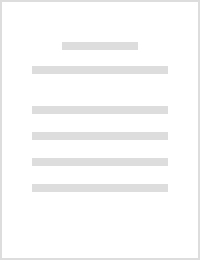
Procedia Manufacturing, 2019
Abstract The microstructure, surface roughness and mechanical properties of aluminum thin films d... more Abstract The microstructure, surface roughness and mechanical properties of aluminum thin films deposited by rf magnetron sputtering are presented. The films were sputtered on stainless steel substrates at varying rf powers of 150 W, 200 W, 300 W and 350 W at a deposition time of 2 hours and at a substrate temperature of 90oC. The microstructure at 200 W shows fine, well-defined and homogeneous distributed grains. The lowest surface roughness is at the power of 150 W whereas the highest is at 250 W. The highest modulus, hardness and lowest depth of penetration are obtained at 200 W. The results indicate no direct relationship among rf power, mechanical, roughness and microstructure of Al thin films deposited at substrate temperature of 90oC. As such, optimization of the sputtering process for rf power is necessary for deposition of quality Al films on metals.
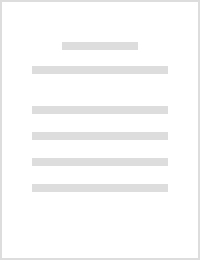
Optics and Laser Technology, Aug 1, 2019
Abstract In this study, the effect of laser induced periodic patterning of α-β titanium alloy (Ti... more Abstract In this study, the effect of laser induced periodic patterning of α-β titanium alloy (Ti-6Al-4V) developed by excimer laser (ArF, with a laser fluence of 2.4 J/cm2, a laser pulse repetition rate of 200 Hz and 50 laser pulses) and Fiber laser (using a power of 5 W, frequency of 80 kHz, scan speed of 800 mm/s and 2 times scanning) on its microstructure and corrosion behaviour have been investigated. The microstructure of the patterned surface shows a significant refinement of grains with the presence of α and β. A very low mass fraction of TiO2 was noticed when patterning was performed using ArF laser. A significant improvement in total surface energy (from 37 mN/m for Ti-6Al-4V to 41 mN/m for ArF laser patterned surface and 40 mN/m for Fiber laser patterned surface) and polar energy (from 11 mN/m for Ti-6Al-4V to 26 mN/m for ArF laser patterned surface and 24 mN/m for Fiber laser patterned surface) have been observed. Corrosion rate was reduced due to laser patterning (from 6.12 mm/year for as-received Ti-6Al-4V to 2.17 × 10−2 mm/year for ArF laser patterned and 1.68 × 10−2 mm/year for Fiber laser patterned Ti-6Al-4V surfaces). Laser surface patterning improved apatite deposition from 15% area coverage for Ti-6Al-4V to 34% and 33% area coverage for ArF and Fiber laser patterned surfaces, respectively.
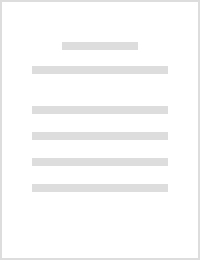
Intermetallics, Jul 1, 2021
Abstract The present work concerns understanding the microstructure and nano-mechanical propertie... more Abstract The present work concerns understanding the microstructure and nano-mechanical properties of titanium carbide (TiC) added (5 wt% and 10 wt%) titanium aluminide (Ti45Al5Nb0.5Si) composite developed by laser additive manufacturing (LAM) route. LAM has been carried out by melting pre-mixed titanium aluminide (Ti45Al5Nb0.5Si) and titanium carbide (5 wt% and 10 wt%) with a Nd:YAG laser (of 3 kW power and 2 mm beam diameter) and subsequently, depositing it on Ti–6Al–4V substrate one layer after another to a dimension of 10 mm × 10 mm x 4 mm. The process parameters used in the present study were applied power (varying from 400 to 600 W), scan speed between 200 and 400 mm/min and powder feed rate varying from 1.8 to 2.6 g/min. The effect of process parameters on microstructure, phase fraction, residual stress and microhardness was determined. In the LAM clad coupon there is formation of refined microstructures with the dispersion of carbides (TiC, Ti2AlC, Ti3AlC2 and Ti2AlC) in refined α2+γ matrix. TiC addition increases the nanohardness, which varies with applied laser parameters. Attempts were made to derive the process parameters corresponding to a maximum improvement in nano-hardness.

Metallurgical and Materials Transactions, Apr 25, 2018
The present study concerns a detailed evaluation of wear resistance property of plasma spray depo... more The present study concerns a detailed evaluation of wear resistance property of plasma spray deposited composite hydroxyapatite (HA)-based (HA-50 wt pct TiO 2 and HA-10 wt pct ZrO 2) bioactive coatings developed on Ti-6Al-4V substrate and studying the effect of heat treatment on it. Heat treatment of plasma spray deposited samples has been carried out at 650°C for 2 hours (for HA-50 wt pct TiO 2 coating) and at 750°C for 2 hours (for HA-10 wt pct ZrO 2 coating). There is significant deterioration in wear resistance for HA-50 wt pctTiO 2 coating and a marginal deterioration in wear resistance for HA-10 wt pct ZrO 2 coating in as-sprayed state (as compared to as-received Ti-6Al-4V) which is, however, improved after heat treatment. The coefficient of friction is marginally increased for both HA-50 wt pct TiO 2 and HA-10 wt pct ZrO 2 coatings in as-sprayed condition as compared to Ti-6Al-4V substrate. However, coefficient of friction is decreased for both HA-50 wt pct TiO 2 and HA-10 wt pct ZrO 2 coatings after heat-treated condition as compared to Ti-6Al-4V substrate. The maximum improvement in wear resistance property is, however, observed for HA-10 wt pct ZrO 2 sample after heat treatment. The mechanism of wear has been investigated.
Procedia Manufacturing, 2017
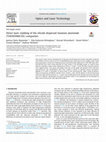
Optics and Laser Technology, Oct 1, 2018
The present study concerns development of titanium silicide dispersed titanium aluminide composit... more The present study concerns development of titanium silicide dispersed titanium aluminide composite with addition of 5 wt.% and 10 wt.% Si in Ti45Al5Nb0.5Si base alloy by direct laser cladding under varied process parameters. Direct laser cladding has been conducted using a high power (3 kW) fiber optic delivered Nd:YAG laser (with a beam diameter of 2 mm) using a 3-axis handling system in a layer by layer fashion to develop a coupon with a dimension of 10 mm  10 mm  4 mm. The effect of process parameters (applied power, scan speed and powder feed rate) on the depth and integrity of the clad zone, microstructures and microhardness have been studied in details to optimize process parameters. Addition of Si leads to formation of micro-cracks in the microstructures under varied parameters. There are formations of different silicides (Ti 5 Si 3 , Ti 7 Al 5 Si 12 , TiSi 2 and TiSi phases) in the microstructure of the base alloy with the presence a 2 + c phase. The microhardness of the clad layer increases with addition of Si. However, optimization of process parameters needs to be undertaken for the formation of defect free microstructure with improved hardness.
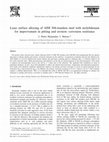
Materials Science and Engineering A-structural Materials Properties Microstructure and Processing, Jul 1, 1999
The present study concerns laser surface alloying (LSA) of AISI 304 stainless steel (304-SS) with... more The present study concerns laser surface alloying (LSA) of AISI 304 stainless steel (304-SS) with predeposited Mo (by plasma spraying) to enhance pitting and erosion-corrosion resistance of the substrate. A parametric correlation between the alloyed zone (AZ) depth (w) vis-à-vis incident laser power density (Q) and linear scanning speed (6) indicates that w is directly related to Q but varies inversely with 6. Both microstructure and chemistry of the AZ are strong functions of the LSA parameters. LSA seems to improve the microhardness level in the AZ by 2-3 times that of the substrate. The optimum LSA conditions in terms of predeposit thickness, Q and 6 have been identified to achieve the desired microstructure, composition and mechanical properties. LSA under such optimum conditions significantly improves the pitting corrosion resistance in terms of critical potential for pit formation (E PP1) and pit growth (E PP2). In addition, the erosion-corrosion resistance in 20 wt.% sand in 3.56 wt.% NaCl solution registers a marked improvement. Thus, it is concluded that LSA of 304-SS with Mo is an appropriate technique to enhance the resistance to pitting and erosion-corrosion in stainless steel.
Uploads
Papers by Jyotsna Dutta Majumdar