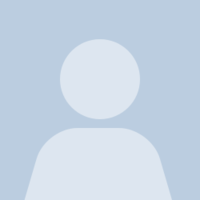
Andreas Kailer
Related Authors
chika oliver ujah
Tshwane University of Technology
Ivo Dlouhy
Institute of Physics of Materials ASCR
Awais Qadir
Technische Universität Bergakademie Freiberg
Zeeshan Baig
Universiti Teknologi PETRONAS
Rahul Kumar
Tallinn University of Technology
Uploads
Papers by Andreas Kailer