Papers by Myungchang Kang
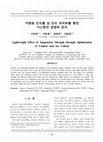
Journal of the Korean Society of Manufacturing Process Engineers
Recently, the lightweight paradigm has emerged in the automobile industry. Moreover, there are th... more Recently, the lightweight paradigm has emerged in the automobile industry. Moreover, there are three main methods for reducing the weight of the control arm during design. The first method involves using lighter materials in place of heavy ones. The second method is via optimization analysis technique using CAE. The third is via correlation, which checks the correlation between CAE results and actual testing. Because the CAE includes a safety rate, checking the difference between the actual tests and reducing the weight based on the difference are possible. The forged control arm can be thickened using mold open tolerances, the strength range of the mold open tolerance can be determined, and the optimal strength can be derived. The optimal strength control arm derived from the correlation reduces the ratio compared with the existing design, which can lead to weight reduction.
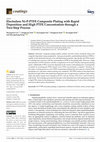
Coatings
Electroless composite plating enables uniform and thin surface treatment along with composite dep... more Electroless composite plating enables uniform and thin surface treatment along with composite deposition using nanoparticles. Among such particles, polytetrafluoroethylene (PTFE) is capable of dry lubrication because of its self-lubricating properties. Specifically, the PTFE content in a plating layer increases with the concentration of PTFE in the plating bath. However, a high concentration of PTFE interferes with the co-deposition of Ni and P, thereby reducing the plating speed. Additionally, PTFE is unevenly deposited on the surface of the plating layer. Consequently, a method for increasing the PTFE content at low PTFE concentrations is required. Therefore, in this study, a stirring process in a low-PTFE-concentration plating bath and a process wherein PTFE precipitates on a specimen without stirring were combined. The PTFE content of the plated layer deposited on high carbon steel, plated layer deposition rate, average friction co-efficient, static contact angle, and surface en...
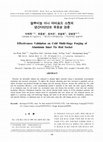
Journal of the Korean Society of Manufacturing Process Engineers, 2022
Recently, the automobile industry has continued to demand lighter materials owing to internationa... more Recently, the automobile industry has continued to demand lighter materials owing to international environmental regulations and increased convenience. To address this demand, aluminum parts have increased in popularity and are mainly developed and produced through hot forging and cold pressing. However, because this method has low yield and low production efficiency, a new manufacturing method is desirable. In this study, the water capacity efficiency of an aluminum inner tie rod socket was investigated using cold forging that provided a high yield and excellent production efficiency. Mechanical properties were derived through tensile testing of 6110A aluminum materials, and critical fracture factor and process analysis based on experimental data were carried out. The optimized process was applied as a prototype using cold multi-stage forging, and based on the derived results, the formability, productivity, and material efficiency of aluminum inner tie rod socket parts using this cold forging process was verified.
Journal of the Korean Society of Manufacturing Process Engineers, 2021
A cyclone is a dust-separating mechanism that works on the principle of centrifugal force. The pe... more A cyclone is a dust-separating mechanism that works on the principle of centrifugal force. The performance of a cyclone is evaluated using pressure loss and collection efficiency. A multi-cyclone arrangement is used to improve the collection efficiency within a limited area. In this study, experiments and numerical analyses were conducted on a dual arrangement of mini-hydrocyclone separators, which was fabricated using 3D printing. The experiment was performed at an inlet flow rate of 0.7 m/s, and alumina powder with a particle size of 0.5, 15, and 50 µm. ANSYS FLUENT, was used for the numerical analysis. The reliability of the numerical analysis was verified through a comparison with the experimental results. The errors in the experiment and numerical analysis were confirmed to be 2% at the outlet flow rate.
Journal of Manufacturing Processes

The Korean Society of Manufacturing Process Engineers, 2021
Recently, owing to the high demand for eco-friendly cars in the automotive industry, noise and vi... more Recently, owing to the high demand for eco-friendly cars in the automotive industry, noise and vibrations have become major challenges. The use of laminated damping steel is increasing in response to these demands. Laminated damping steel is primarily used in sound insulation plates. The vibration energy is converted into thermal energy due to the viscoelastic resin being located between two steel sheets and being able to damp the vibrations when an external force, such as, noise or vibration is applied to the steel plate. Laminated damping steel is chiefly applied to dash panels in automotive body parts, and because of its structure, junction technology for bonding with other components is necessary. However, there has not been sufficient research conducted on junctions. In this study, regardless of the electrode shape, in the range of 4.0 ~ 8.0 kA welding current, the same welding force and welding time were applied which were 2.8 kN and 200 ㎧ (12 cycles) and the tensile shear load and nugget size were analyzed after the resistance spot welding between different materials of laminated damping steel with a thickness of 1.035 mm. The results show that in the range of 5 ~ 8 kA welding current, 1.035 mm laminated damping steel meets the MS181-15 standard, which is the technical standard of Hyundai-Kia Motors.

The Korean Society of Manufacturing Process Engineers, 2021
Cold forging is a method in which molding is performed at room temperature. It has a high materia... more Cold forging is a method in which molding is performed at room temperature. It has a high material recovery rate and dimensional precision and produces excellent surface quality, and it is mainly used for the production of bolted or housing products. The lifespan of cold forging molds is generally determined by the wear of the mold, plastic deformation of the mold, and fatigue strength. Cold forging molds are frequently damaged due to fatigue destruction rather than wear and plastic deformation in a high-temperature environment as it is molded at room temperature without preheating the raw material and mold. Based on the results analyzed through FEM, an effective mold structure design method was proposed by analyzing the changes in tensile and compressive stresses on molds according to the number of molds and reinforcement rings and comparing the product geometry and mold stress using three existing mold models.
Surface and Coatings Technology, 2002
TiN films were deposited onto AISI D2 steels by an arc ion plating (AIP) technique. The effects o... more TiN films were deposited onto AISI D2 steels by an arc ion plating (AIP) technique. The effects of atmospheric humidity and counterface materials on the tribological behavior of the AIP-TiN layer have been investigated using a conventional ball-on-disc wear apparatus. ...
Transactions of Nonferrous Metals Society of China, 2009
CNT/Fe/Al 2 O 3 mixed powders were synthesized from Fe/Al 2 O 3 nanopowders using thermal CVD for... more CNT/Fe/Al 2 O 3 mixed powders were synthesized from Fe/Al 2 O 3 nanopowders using thermal CVD for the homogeneous dispersion of carbon nanotubes CNTs. CNTs consisted of MWNT, and the diameter was approximately 20-30 nm. After sintering, CNTs were homogenously located throughout Al 2 O 3 grain boundary and were buckled. A femto-second laser installed with special optical systems was used for micromachining of the nanocomposites. The relationship between material ablation rate and energy fluence was theoretically investigated and compared with experimental results from cross-sectional SEM analysis. The nanocomposites which have higher content of CNT show a fairly good machining result due to its higher thermal conductivity and smaller grain size as well as lower light transmittance.
Transactions of Nonferrous Metals Society of China, 2011
The shape and thickness of the dome were investigated with the aim of optimizing the type II CNG ... more The shape and thickness of the dome were investigated with the aim of optimizing the type II CNG storage vessels by using a finite element analysis technique. The thickness of the liners and reinforcing materials was optimized based on the requirement of the cylinder and dome parts. In addition, the shape of the dome, which is most suitable for type II CNG storage vessels, was proposed by a process of review and analysis of various existing shapes, and the minimum thickness was established in this sequence: metal liners, composite materials and dome parts. Therefore, the new proposed shape products give a mass reduction of 4.8 kg(5.1%
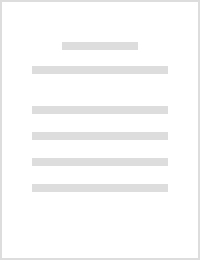
Transactions of Nonferrous Metals Society of China, 2012
ABSTRACT Mn+1AXn (MAX) phases are a family of nanolaminated compounds that possess unique combina... more ABSTRACT Mn+1AXn (MAX) phases are a family of nanolaminated compounds that possess unique combination of typical ceramic properties and typical metallic properties. As a member of MAX phase, Ti2AlN bulk materials are attractive for some high-temperature applications. The synthesis, characteristics and machining performance of hybrid Ti2AlN bulk materials were focused on in this work. The bulk samples mainly consisting of Ti2AlN MAX phase with density close to theoretic one were synthesized by a spark plasma sintering method. Scanning electron microscopy results indicate homogenous distribution of Ti2AlN grains in the samples. Micro-hardness values are almost constant under different loads (6–6.5 GPa). A machining test was carried out to compare the effect of material properties on micro-electrical discharge machining (micro-EDM) performance for Ti2AlN bulk samples and Ti6242 alloy. The machining performance of the Ti2AlN sample is better than that of the Ti6242 alloy. The inherent mechanism was discussed by considering their electrical and thermal conductivity.
Journal of Materials Processing Technology, 2002
This study proposes an optimization cutting speed program developed to improve the machining prec... more This study proposes an optimization cutting speed program developed to improve the machining precision and tool life in high speed machining using the ball end mill. This program optimizes the cutting speed that varies during free surface machining. As for the ...
Journal of Materials Processing Technology, 2002
Recently the applications of high speed machining have increased due to the need for high precisi... more Recently the applications of high speed machining have increased due to the need for high precision and high accuracy machining and machining of difficult-to-cut material. However, the high speed machining also accompanies problems: the product quality can be ...
Journal of The Electrochemical Society, 2003
Cross-sectional scanning electron microscopy (SEM), secondary-ion mass spectrometry (SIMS), atomi... more Cross-sectional scanning electron microscopy (SEM), secondary-ion mass spectrometry (SIMS), atomic force microscopy (AFM), and electrochemical measurements are utilized to examine the effect of additives on the morphology and nature of Cu electrodeposited on ...

The International Journal of Advanced Manufacturing Technology, 2008
Much research has been carried out in the manufacturing of helical gears by cold forging or by ex... more Much research has been carried out in the manufacturing of helical gears by cold forging or by extrusion. Although cold forging is applied to some bevel, spur, and helical gears, problems in connection with the reduction forming load and tool life still make it difficult for these methods to be commercialized. In this study, focusing on reducing a load in forming helical gears, the extrusion of helical gears by two-step process is proposed. This process is composed primarily of extruding a billet to a spur gear and then twisting the previous spur gear extruded to a helical gear. Cylindrical billets of Cr-Mo steel(SCM 415) and aluminium alloy(Al60 series) were used as specimen materials for the experiments. The maximum loads obtained by upper-bound analysis and FEM are compared with the results of experiments. The loads of the analysis have good agreements with those of the experiment. The newly proposed method can be used as an advanced technique that remarkably reduces the forming load and replaces the conventional forming.
Current Applied Physics, 2012
The Korean Society of Manufacturing Process Engineers, 2021

Materials
Recently, friction stir welding of dissimilar materials has emerged as one of the most significan... more Recently, friction stir welding of dissimilar materials has emerged as one of the most significant issues in lightweight, eco-friendly bonding technology. In this study, we welded the torsion beam shaft—an automobile chassis component—with cast aluminum to lighten it. The study rapidly and economically investigated the effects of friction stir welding and process parameters for A357 cast aluminum and FB590 high-strength steel; 14 decomposition experiments were conducted using a definitive screening design that could simultaneously determine the effects of multiple factors. Friction stir welding experiments were conducted using an optical microscope to investigate the tensile shear load behavior in the welding zone. In addition to understanding the interactions between tool penetration depth and plunge speed and tool penetration depth and dwell time, we investigated and found that tool penetration depth positively affected the size of the hooking area and contributed to the stabiliza...
The Korean Society of Manufacturing Process Engineers
In this study, a mini hydro cyclone was designed and manufactured to achieve an inlet flow rate o... more In this study, a mini hydro cyclone was designed and manufactured to achieve an inlet flow rate of 2 L/min in the experiment, which was conducted using alumina powder with a specific gravity of 3.97. This hydro cyclone was studied for using in steam and water analysis system (SWAS) of thermal power plant and was manufactured by 3D printing. Numerical analysis was performed with Solidworks Flow Simulation, utilizing the reynolds stress method (RSM) of fluid multiphase flow analysis models. Experimental and numerical analysis were performed under the three conditions of inlet velocity 2.0, 4.0, and 6.0 m/s. The separation efficiency was over 80% at all inlet velocity conditions. At the inlet velocity 4m/s, the separation efficiency was the best, and it was confirmed that the efficiency was more than 90%.
The Korean Society of Manufacturing Process Engineers
Uploads
Papers by Myungchang Kang