Papers by Takalani Madzivhandila
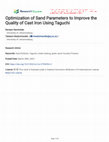
Research Square (Research Square), Mar 28, 2023
The main aim of the foundry industries is to produce quality castings with no rejection. In addit... more The main aim of the foundry industries is to produce quality castings with no rejection. In addition, in the present era of global competition, manufacturing industries has bound to take the challenge that is demand for high quality product with reduced lead-time. However, with the diversity of greensand casting parameters, it results in varying effects on the quality. With sand being one of the most frequent cause of quality reject/rework, it is essential to understand the effect it has on the casting outcome. Taguchi's approach in quality states that the quality of a product is dependent on the input, he gured that the perfect time to eliminate differences in products is during the designing and manufacturing of products, he developed a strategy for quality that can be used in process. Therefore, it is important to understand the inputs in sand mould preparation. The focus of the research is on greensand moulding process. The casting defect is the most contributing factor to quality reject in most foundries. The sand moulding process is the most contributing factor to the formation scrap. The target in foundries is to achieve low casting defects at minimum cost. It is essential to select signi cant parameters that cause variation of quality characteristic of castings .data should be collected dictated by the chosen orthogonal array (OA) and parameter levels. With the collected at the analysis of variance (ANOVA) can be generated to determine the statistical importance of parameter and response graphs are plotted to determine the optimum setting of control parameter
Ceramics International, 2012
ABSTRACT SiO2–cBN composites were consolidated by spark plasma sintering at 1473–1973K. The effec... more ABSTRACT SiO2–cBN composites were consolidated by spark plasma sintering at 1473–1973K. The effects of cBN content and sintering temperature on the relative density, phase transformation, microstructure and mechanical properties of the SiO2–cBN composites were investigated. The relative density of the SiO2–cBN composites increased with increasing SiO2 content. The phase transformation of cBN to hBN in SiO2–cBN composites was identified at 1973K, showing the highest transformation temperature in cBN-containing composites. The SiO2–20vol% cBN composites sintered at 1673K showed the highest hardness and fracture toughness of 12.5GPa and 1.5MPam1/2, respectively.
International journal of environment and waste management, 2023
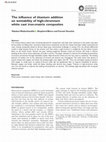
Journal of Composite Materials, 2018
The mining industry exerts ever increasing demand for components with high wear resistance to the... more The mining industry exerts ever increasing demand for components with high wear resistance to the extent that plain ferrous alloys are falling short. Innovative metal-matrix composites non-ferrous metals have been widely researched and used. Casting composites based on ferrous alloys pose monumental challenges in casting. First, the density differential results in large buoyant forces on the ceramic such that unless a rigid structure is configured, the less dense ceramic floats on the metal stream. Second, the poor wetting properties between metal and ceramic will result in inferior bonding of the matrix, hence separation of solids in service. The paper attempts to improve the bonding characteristics of zirconia and alumina through wettability studies. High-chromium white cast iron was used as a substrate. The wetting behavior of molten iron on the substrates of zirconia and alumina was investigated. The study shows that alumina is poorly wetted with copper and nickel; the wetting a...
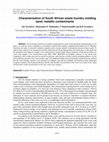
Waste foundry sands are invariably contaminated to some extent during the manufacturing of cast a... more Waste foundry sands are invariably contaminated to some extent during the manufacturing of cast alloys. As such the sand is regarded as a hazardous material that requires exceptional precautions for its disposal. Therefore, the study is initiated to identify, quantify and to classify metallic contaminants present in these sands. To achieve these objectives in conjunction with the South African Waste Management Act which plays as the guide line for industrial waste disposal, samples were collected from various South African foundries. In the present study, ten waste sand samples were characterised using XRF, XRD, SEM-EDS and Sulphur analyser. It was found after comparison with a virgin sand used as control or reference sand, that the cast alloy and the moulding additives are the main pollutants present in the waste foundry sand. The additional sulphur and acid potential characterisation, showed that the waste foundry sand has a low potential for sulphuric acid and acid sulphate soil ...
Engineering Journal, 2016
Dry analysis techniques including X-ray fluorescence (XRF), X-ray diffraction (XRD), Scanning Ele... more Dry analysis techniques including X-ray fluorescence (XRF), X-ray diffraction (XRD), Scanning Electron Microscope (SEM-EDS) and Fourier Transform Infra-red (FTIR) have been used to assess the Physico-chemical of waste sand samples, obtained from different local foundry. The casting process involved included Aluminum in shell sand, brass under alky urethane, grey iron in greensand moulding, high chrome using furan sand, steel casting in alkaline phenolic and lastly cast iron from greensand mould. The study revealed the transformations and changes which have taken place in the waste sand due to the casting process, in terms of chemical composition, mineralogy, morphology and bonding types. The study demonstrated that the waste sand after the casting process was a completely new material, compared to the original virgin sand used for moulding process.
Uploads
Papers by Takalani Madzivhandila