Papers by Philippe Véron
International Journal on Interactive Design and Manufacturing (IJIDeM)
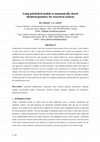
Engineering with Computers
Simplification of polyhedral models, which may incorporate large numbers of faces and nodes, is o... more Simplification of polyhedral models, which may incorporate large numbers of faces and nodes, is often required to reduce their amount of data, to allow their efficient manipulation and to speed up computation. Such a simplification process must be adapted to the use of the resulting polyhedral model. Several applications require simplified shapes which have the same topology as the original model (e.g. reverse engineering, medical applications, etc). Nevertheless, in the fields of structural analysis and computer visualization for example, several adaptations and idealizations of the initial geometry are often necessary. To this end, within this paper a new approach is proposed to simplify an initial manifold or non-manifold polyhedral model with respect to bounded errors specified by the user or set up, for example, from a preliminary F.E. analysis. The topological changes which may occur during a simplification because of the bounded error (or tolerance) values specified are performed using specific curvature and topological criteria and operators. Moreover, topological changes, whether they kept or not the manifold of the object are managed simultaneously with the geometric operations of the simplification process.
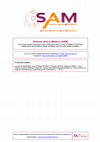
Engineering with Computers
Today, being able to generate and produce shapes that fit mechanical and functional requirements ... more Today, being able to generate and produce shapes that fit mechanical and functional requirements and having as low as possible mass is crucial for aerospace and automotive applications. Besides, the rise of new additive manufacturing technologies has widened the possibilities for designing and producing complex shapes and internal structures. However, current models, methods and tools still represent a limitation to that new horizon of printable shapes. This paper addresses the way internal lattice structures can be generated and optimized to reduce the mass of a product. A new framework is introduced that allows the modeling and optimization of non-uniform patterned lattice structures. Using non-uniform structures, additional degrees of freedom are introduced and allow the definition of a wide variety of shapes which can better fit the requirements. First, a non-uniform patterned lattice structure is generated using the results of an initial finite element analysis. This initial structure is then optimized while iteratively removing the beams considered as useless with respect to a user-specified mechanical criteria. At each iteration, the lattice structure is sent to a finite element solver that returns the von Mises stress map used to drive the simplification process. Here, the simulations are performed on the wireframe lattice structures to speed up the optimization loops. Once this process is completed, the final structure is no longer fully patterned, but it is reorganized to reduce the mass while satisfying the mechanical criteria. This approach is illustrated with examples coming from our prototype software.
Finite Elements in Analysis and Design
A flexible cable is modeled by a geometrically exact beam model with 3D rotations described using... more A flexible cable is modeled by a geometrically exact beam model with 3D rotations described using quaternion parameters. The boundary value problem is then discretized by the finite element method. The use of an asymptotic numerical method to solve the problem, requiring quadratic equations, is well suited to the quaternion parametrization. This combination of methods leads to a fast, robust and accurate algorithm very well-adapted for the simulation of the assembly process of cables. This is proved by running many examples involving complicated solutions.
Engineering with Computers
Page 1. Engineering with Computers (1998) 14:23 35 9 1998 Springer-Verlag London Limited Engineer... more Page 1. Engineering with Computers (1998) 14:23 35 9 1998 Springer-Verlag London Limited Engineering C~nputers Integrated Design and Collaborative Engineering of Fabric Structures P. V6ron, 1 P. Trompette 2 and JC ...
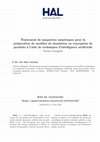
Computers in Industry
Mes remerciements s'adressent tout d'abord à Madame Claire LARTIGUE et Monsieur Benoit EYNARD pou... more Mes remerciements s'adressent tout d'abord à Madame Claire LARTIGUE et Monsieur Benoit EYNARD pour avoir accepté d'être les rapporteurs de mes travaux de thèse. Je remercie Messieurs Améziane AOUSSAT et Christian MASCLE d'avoir accepté d'évaluer mes travaux de recherche. Je remercie particulièrement mes deux directeurs de thèse Philippe VERON et Jean-Philippe PERNOT pour avoir encadré mes travaux de recherche durant ces trois années. Merci tout d'abord de m'avoir proposé ce sujet grâce auquel j'ai découvert le domaine de l'intelligence artificielle. Et surtout, merci pour ces heures et souvent ces nuits que vous avez passé à relire mes articles et présentations. Vous m'avez donné le goût de la recherche et l'envie de poursuivre ma carrière dans cette voie. Je remercie Lionel FINE et toute son équipe d'Airbus Groups Innovation. En plus de me fournir un passionnant support d'étude pour valoriser mes recherches, Lionel a été comme un troisième co-encadrant. Ses conseils toujours très avisés m'ont permis de progresser. Merci Lionel pour ces échanges très riches, j'espère que cette thèse n'est que le début d'une fructueuse collaboration. Je remercie mon directeur Laurent ARNAUD du campus Arts et Métiers ParisTech de Cluny et mes collègues de l'équipe de construction mécanique pour leur constante bonne humeur et pour leur soutien sans faille tout particulièrement ces derniers mois. Merci donc à Angelo, Frédéric, Michel, Yann et Yoann. Enfin, merci à Marc de tout coeur pour ta patience, tes encouragements et tes petits plats.
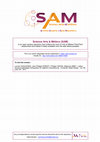
Computer-Aided Design
Additive manufacturing offers new available categories of geometries to be built. Among those cat... more Additive manufacturing offers new available categories of geometries to be built. Among those categories, one can find the well developing field of lattice structures. Attention has been paid on lattice structures for their lightweight and mechanical efficiency ratio, thus leading to more optimized mechanical parts for systems. However this lightness only holds true from a mass related point of view. The files sent to additive manufacturing machines are quite large and can go up to such sizes that machines can freeze and get into malfunction. This is directly related to the lattice structures tendency to be of a high geometric complexity. a large amount of vertices and triangles is necessary to describe them geometrically, thus leading to larger file sizes. With the increasing use of lattice structures, the need for their files to be lighter is also rising. This paper aims at proposing a method for tessellating a certain category of such structures, using topologic and geometric criteria to generate as few as possible triangles, thus leading to lightweight files. The triangulation technique is driven by a chordal error that control the deviation between the exact and tessellated structures. It uses interpolation, boolean as well as triangulation operators. The method is illustrated and discussed through examples from our prototype software.
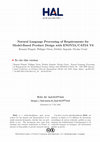
IFIP Advances in Information and Communication Technology, 2016
The enterprise level software application that supports the strategic product-centric, lifecycle-... more The enterprise level software application that supports the strategic product-centric, lifecycle-oriented and information-driven Product Lifecycle Management business approach should enable engineers to develop and manage requirements within a Functional Digital Mock-Up. The integrated, model-based product design ENOVIA/CATIA V6 RFLP environment makes it possible to use parametric modelling among requirements, functions, logical units and physical organs. Simulation can therefore be used to verify that the design artefacts comply with the requirements. Nevertheless, when dealing with document-based specifications, the definition of the knowledge parameters for each requirement is a labour-intensive task. Indeed, analysts have no other alternative than to go through the voluminous specifications to identify the values of the performance requirements and design constraints, and to translate them into knowledge parameters. We propose to use natural language processing techniques to automatically generate Parametric Property-Based Requirements from unstructured and semi-structured specifications. We illustrate our approach through the design of a mechanical ring.
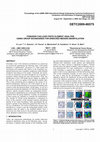
Volume 2: 29th Computers and Information in Engineering Conference, Parts A and B, 2009
Nowadays, most of the numerical simulations are carried out by successively performing the follow... more Nowadays, most of the numerical simulations are carried out by successively performing the following steps: CAD model definition or modification, conversion to a mesh model and enrichment with semantic data relative to the simulation (e.g. material behaviour laws, boundary conditions), Finite Element simulation and analysis of the results. Classically, the semantic data are attached to the mesh through the use of groups of geometric entities sharing the same characteristics. Thus, any modification of the CAD model always implies an update of the mesh as well as an update of the attached semantic data. This is time-consuming and not adapted to the context of industrial maintenance. Moreover, the CAD models do not always exist and should therefore be reconstructed starting from scratch or from the physical object. In this paper, we set up a framework towards the definition of CAD-less Finite Element analyses wherein enriched meshes are manipulated directly. The geometric manipulations are constrained with information extracted from the group definition. Actually, the boundaries of those groups are exploited to constrain the modifications. The concept of Virtual Group Boundaries is introduced to focus on the extension of the attached semantic information instead of the actual tessellation while generalising the approach to groups of any dimension going from 0D (vertex) to 3D (e.g. tetrahedron). The notion of Elementary Group is also introduced as a mean to ease the forthcoming transfer of the semantics from the initial to the modified models. Such a framework also finds interest in the preliminary design phases where alternative solutions have to be evaluated.
Acoustic Emission (AE) is considered an efficient tool for monitoring of machining operations, fo... more Acoustic Emission (AE) is considered an efficient tool for monitoring of machining operations, for both tool condition and working piece integrity. However, the use of AE is more challenging in case of drilling, due to heavy dependence of AE signals to process parameters. Monitoring drilling using AE thus requires robust methods to extract useful information in signals. The paper describes such a method that adapts itself to AE signals obtained during drilling, allowing the automatic set-up of an adaptive threshold to perform AE count rate. Experiments have been conducted that show the robustness of the method and its usefulness in drilling monitoring.
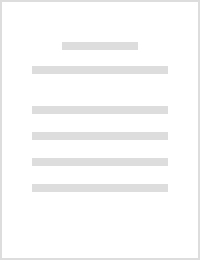
Nowadays, it is commonly admitted that the aesthetic appearance of a product has an enhanced role... more Nowadays, it is commonly admitted that the aesthetic appearance of a product has an enhanced role in its commercial success. Therefore, understanding and manipulating the aesthetic properties of shapes in the early design phases has become a very important field of research. There exists an appropriate vocabulary for describing the aesthetic properties of 2D free-form curves that includes terms such as straightness, acceleration, convexity and tension, which are normally used by stylists when describing and modifying shapes. However, the relationships between this vocabulary and the geometric models are not well established. This work investigates the possibility of applying Machine Learning Techniques (MLT) to discover possible classification patterns of 2D free-form curves with respect to the so-called straightness of the curve. First, we verified that MLT can correctly (99, 78%) reapply the classification to new curves. In addition, we verified the abilities of the Attribute Sele...
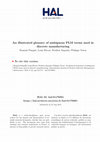
International Journal of Product Lifecycle Management, 2015
Product lifecycle management (PLM) is a strategic product-centric, lifecycle-oriented and informa... more Product lifecycle management (PLM) is a strategic product-centric, lifecycle-oriented and information-driven business approach that strives to integrate people and their inherent practices, processes, and technologies, both within and across functional areas of the extended enterprise from inception to disposal. The integration of people relies on the harmonisation of domain-specific glossaries by standardising a universal PLM vocabulary. So far, unfortunately, there is no PLM standard vocabulary. Therefore, the tremendous amount of knowledge that is continually brought forward by academic research studies, industrial practices and computer-aided applications causes semantic ambiguities. This paper consists of an illustrated glossary and a conceptual map. The glossary identifies, discusses, clarifies and illustrates ambiguous terms used in discrete manufacturing. The conceptual map finally underlines the logical flow of refereed definitions.
La présente invention concerne un distributeur hydraulique (10) muni d'au moins un corps (11)... more La présente invention concerne un distributeur hydraulique (10) muni d'au moins un corps (11) comportant une chemise (12) pourvue d'un orifice d'alimentation (13). Ce dispositif hydraulique (10) a une tige de transfert (15) munie d'au moins un conduit (16) de transfert de fluide, d'un premier orifice (17) présent dans la chemise (12) et d'un deuxième orifice (18) agencé à l'extérieur de la chemise (12). La chemise (12) comporte une chambre d'alimentation (25) reliée audit orifice d'alimentation (13) et une chambre principale (30) de retour de fluide reliée à un moyen d'évacuation (50) pour évacuer le fluide, un moyen de contrôle (20) étant solidarisé à la chemise (12) pour déplacer cette chemise (12) en translation par rapport à ladite tige de transfert (15) afin de contrôler la circulation de fluide au sein de ladite tige de transfert (15
Information Processing in Civil and Structural Engineering Design, 1996
A new methodology dedicated to the design of textile structures is introduced. It is based on a c... more A new methodology dedicated to the design of textile structures is introduced. It is based on a collaborative environment to carry out the dialogues between the actors participating in the design process. A speci®c data architecture has been set up to allow ecient collaborative design loops, to manage the data and check their coherence during the overall design process.
Uploads
Papers by Philippe Véron