Conference Presentations by Becky Gooby
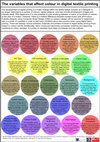
The development of digital printing is a major change within the textile design process as a desi... more The development of digital printing is a major change within the textile design process as a designer is no longer restricted to number of colours, repeat patterns, and may include photographic images and intricate detail. With digital print it is now possible to print anything between a metre, or hundreds of metres, at the click of a button. However, there is a marked difference between screen-colour and print-colour. A textile designer using Computer Aided Design (CAD) to create a design will be required to experiment with a number of variables in order to feel more confident about the outcome when using digital fabric printing. There are already various software, materials and printers involved in digital textile printing which impact on colour results. Additionally, fabric choice and secondary processes (washing and steaming) contribute to colour variation. This poster charts these variables and outline the affects they have on printed colour. Variables will include, but not be limited to: fabric, ink, software, printer, profile applied and secondary processes (washing, steaming).

The development of digital printing is a major change within the textile design process as the de... more The development of digital printing is a major change within the textile design process as the designer is no longer restricted to number of colours, repeat patterns, and may include photographic images and intricate detail. With digital print it is now possible to print anything between a metre, or hundreds of metres, at the click of a button.
However, there is a marked difference between screen-colour and print-colour. A textile designer using Computer Aided Design (CAD) to create a design will be required to experiment with a number of variables in order to feel more confident about the outcome when using digital fabric printing. There are already various software, materials and printers involved in digital textile printing which impact on colour results. Additionally, fabric choice and secondary processes (washing and steaming) contribute to colour variation.
The research project considers how designers can ensure colour assurance when digitally printing on a range of fabrics through an exploration of existing colour tools and methods. Using a practice as research methodology, a number of experiments have been conducted into colour systems, trialling different print techniques and with chemical coatings. The results of these investigations will be presented alongside an exploration of a number of variables which include colour profiling, existing software and tools, and potential CAD adjustments. Additionally, the presentation will provide an overview of the digital inkjet textile printing industry in the UK touching upon a number of case studies considered within the research.
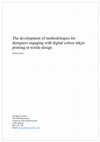
Digital textile printing (DTP) offers exciting, creative potential and entrepreneurial business m... more Digital textile printing (DTP) offers exciting, creative potential and entrepreneurial business models in textile design. Designers are no longer restricted to a number of colours or pattern repeat. It has become possible to print fabric without large set-up costs. This relatively sustainable technology reduces water-usage and dye-wastage. DTP meets Just in Time, Concept to Consumer demand, reducing stock wastage.
However, there is a marked difference between screen-colour to print-colour and software allows a user to select colours unprintable using CMYK colorants. Colour results are further affected by factors such as structure and composition of the fabric, dye type, printer communications, fabric pretreatments and secondary processes. A textile designer will be required to understand and experiment with a number of variables in order to feel colour confident.
These variables were considered, and existing colour management tools and methods evaluated, using a practice-as-research methodology. Experiments showed that neutral and achromatic colours were the most difficult to replicate, and hues with magenta/blue undertones were problematic. The choice of substrate had a sizeable impact on colour visualisation. The results were used to establish a best practice guide for designers wishing to obtain a more acceptable print-colour match.
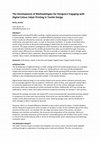
Digital textile printing (DTP) offers exciting, creative potential and entrepreneurial business m... more Digital textile printing (DTP) offers exciting, creative potential and entrepreneurial business models in textile design. However, there is a marked difference between screen-colour to print-colour. Colour results are affected by numerous variables which a textile designer will be required to understand, and experiment with, in order to feel colour confident. A number of variables were tested using a Practice as Research methodology, to determine the impact on printed colour outcome. This paper presents investigations which focused on the development, and generation of, visual indicator methods and ICC profiles generated from data, accumulated through measuring printed colour differences on substrates. The aim to provide an indication of colour changes when printing on different fabric substrates, allowing designers to make adjustments to designs to obtain a better colour match, and develop their colour expectation knowledge. INTRODUCTION The development of digital printing is a major change within the textile design process as a designer is no longer restricted to number of colours or repeat patterns, and may include photographic images and intricate detail in their design work. Digital textile printing (DTP) provides unprecedented opportunity for designers to offer bespoke, and customisation of, designs without large set up costs, leading to new entrepreneurial business models in the textile industry. Digital textile inkjet printing is a non surface-impact print process where colorants (primarily dyes, but increasingly pigment inks) are jetted in a dithered, matrix of dots, onto specially treated fabric, to create the appearance of solid colour. The colorant sits on the surface, although, secondary processes, allow dye molecules to further permeate the fibres. Additionally, DTP may include dye sublimation, solvent, latex, ultraviolet and direct-to-garment printing, for example T-shirt printers. Reduced ink wastage and water use makes DTP a more environmentally sustainable printing method in comparison to screen and rotary printing. Short print runs and the ability to react quickly to market trends allow businesses to carry less stock, reducing storage costs, and the likelihood of stock wastage as fabric is printed to demand. However, there is a marked difference between screen-colour and print-colour. A textile designer will be required to experiment with a number of variables in order to feel confident about the colour outcome of their print. For example: the ink range and colour bank of the printer, variations between one machine and another, the structure and composition of the substrate, fabric pre-treatment, secondary processes and the printer's achievable gamut will all affect final results. Colour is critical in the textile industry both in terms of meeting trends, client requirements and obtaining consistent colour. THE RESEARCH PROJECT The wider research inquiry considers how designers can ensure colour assurance when digitally printing through an exploration of existing colour tools and methods. The aim, to produce an
Papers by Becky Gooby
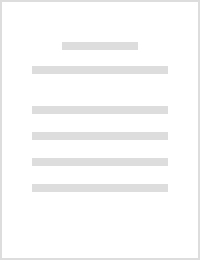
The development of digital printing is a major change within the textile design process as a desi... more The development of digital printing is a major change within the textile design process as a designer is no longer restricted to number of colours, repeat patterns, and may include photographic images and intricate detail. With digital print it is now possible to print anything between a metre, or hundreds of metres, at the click of a button. However, there is a marked difference between screen-colour and print colour. A textiles designer using Computer Aided Design (CAD) to create a design will be required to experiment with a number of variables in order to feel more confident about the outcome when using digital fabric printing. There are already various software, materials and printers involved in digital printing which impact on colour results. Additionally, fabric choice and secondary processes (washing and steaming) contribute to colour variation. The poster charts these variables and outlines the affects they have on printed colour. Variables include, but are not limited to: fabric, ink, software, printer, profiles applied, and secondary processes (washing, steaming).
Journal of textile design, research and practice, Sep 1, 2020
Digital textile printing (DTP) offers creative potential and entrepreneurial business models in t... more Digital textile printing (DTP) offers creative potential and entrepreneurial business models in textile design. Designers are no longer restricted to a number of colors or pattern repeat. It has become possible to print fabric without large setup costs. This relatively sustainable technology reduces water-usage and dye-wastage. DTP meets Just in Time, Concept to Consumer demand, reducing stock wastage. However, there is a marked difference between screen-color to print-color and software allows a user to select colors unprintable using CMYK (cyan, magenta, yellow, black) colorants. Color results are further affected by factors such as structure and composition of the fabric, dye type, printer
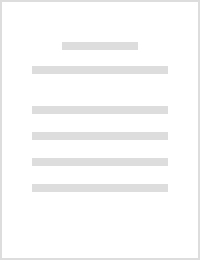
The development of digital printing is a major change within the textile design process as a desi... more The development of digital printing is a major change within the textile design process as a designer is no longer restricted to number of colours, repeat patterns, and may include photographic images and intricate detail. With digital print it is now possible to print anything between a metre, or hundreds of metres, at the click of a button. However, there is a marked difference between screen-colour and print colour. A textiles designer using Computer Aided Design (CAD) to create a design will be required to experiment with a number of variables in order to feel more confident about the outcome when using digital fabric printing. There are already various software, materials and printers involved in digital printing which impact on colour results. Additionally, fabric choice and secondary processes (washing and steaming) contribute to colour variation. The poster charts these variables and outlines the affects they have on printed colour. Variables include, but are not limited to:...
Journal of Textile Design Research and Practice, 2020
Digital textile printing (DTP) offers creative potential and entrepreneurial business models in t... more Digital textile printing (DTP) offers creative potential and entrepreneurial business models in textile design. Designers are no longer restricted to a number of colors or pattern repeat. It has become possible to print fabric without large setup costs. This relatively sustainable technology reduces water-usage and dye-wastage. DTP meets Just in Time, Concept to Consumer demand, reducing stock wastage. However, there is a marked difference between screen-color to print-color and software allows a user to select colors unprintable using CMYK (cyan, magenta, yellow, black) colorants. Color results are further affected by factors such as structure and composition of the fabric, dye type, printer
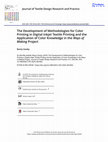
Journal of Textile Design Research and Practice, 2020
Digital textile printing (DTP) offers creative potential and entrepreneurial business models in t... more Digital textile printing (DTP) offers creative potential and entrepreneurial business models in textile design. Designers are no longer restricted to a number of colors or pattern repeat. It has become possible to print fabric without large set-up costs. This relatively sus-tainable technology reduces water-usage and dye-wast-age. DTP meets Just in Time, Concept to Consumer demand, reducing stock wastage. However, there is a marked difference between screen-color to print-color and software allows a user to select colors unprintable using CMYK (cyan, magenta, yellow, black) colorants. Color results are further affected by factors such as structure and composition of the fabric, dye type, printer communications, fabric pre-treatments and secondary processes. A textile designer will be required to understand and experiment with a number of variables in order to feel color-confident. This paper presents investigations which focused on developing meth-ods to aid a designer’s color expectation knowledge, using a Practice-as-Research methodology. Outcomes include a color reference book, digital lap dip tests presented as color maps, and a set of indicator ICC profiles, generated from data accumu-lated through measuring printed color differences on a variety of substrates. These visual prompts are intended to support design-ers to build their own internal color look-up table enabling them to predict and resolve color issues during the design process. Finally, the paper concludes by presenting a Case Study detailing an application of these color methods by the researcher for the Ways of Making project, a collaboration between Sir Peter Blake, Worton Hall Studios and Centre for Fine Print Research (CFPR) at University of West of England (UWE). Here, the indicator profiles were applied to Blake’s images, altering the color data to create experimental color modifications and printed onto silk. An initial selection of works from the project were exhibited at London Original Print Fair, Royal Academy, April 2019.
Thesis Chapters by Becky Gooby
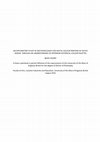
Digital printing technology has had a major impact for the textile designer. Their design process... more Digital printing technology has had a major impact for the textile designer. Their design process now enables them to create complicated multi-layered digital designs incorporating photographic images and intricate detail. Artwork is no longer restricted to a number of colours or a repeat pattern. Leading to new entrepreneurial business models in the textile industry, it has become possible to print a metre, or hundreds of metres, at the click of a button, without high set-up costs.
However, there are concerns about print-colour consistency and outcome. There is a gamut mismatch between the additive - mixing colours with light, and subtractive - mixing pigments or dyes, colour models used to reproduce colour on screen and in print. Numerous variables can alter colour outcome relating to textile chemistry, colour management, viewing conditions and printer technology. Yet colour accuracy is hugely important in the field of fashion and textiles, where colour is critical, and tolerance limits are competitive.
The research inquiry explored a number of variables to determine their influence on colour outcomes using a Practice-as-Research methodology to reflect the conditions and approach designers would employ. These practical experiments progressed into the development of a modality of visual colour methods, which aid a designer’s colour expectation knowledge; a Colour Reference Book, Digital Lab Dip tests presented as Colour Maps, and a set of Indicator ICC profiles generated from data accumulated through measuring printed-colour differences on a variety of substrates. The modality of visual prompts is intended to support designers to build their own ‘internal colour look-up table’, enabling users to predict and resolve colour issues during the design process.
The methods were applied in a real-world test case, using a body of colour work, inspired by archival research of the British Interwar period. The work has been presented as an Exhibition of Praxis, an online Project Tool-Kit, and a Written Report, which takes a traditional thesis format.
https://uwe-repository.worktribe.com/output/8704673/an-exploratory-study-of-methodologies-for-digital-colour-printing-in-textile-design-through-an-understanding-of-interwar-historical-colour-palettes
Uploads
Conference Presentations by Becky Gooby
However, there is a marked difference between screen-colour to print-colour and software allows a user to select colours unprintable using CMYK colorants. Colour results are further affected by factors such as structure and composition of the fabric, dye type, printer communications, fabric pretreatments and secondary processes. A textile designer will be required to understand and experiment with a number of variables in order to feel colour confident.
These variables were considered, and existing colour management tools and methods evaluated, using a practice-as-research methodology. Experiments showed that neutral and achromatic colours were the most difficult to replicate, and hues with magenta/blue undertones were problematic. The choice of substrate had a sizeable impact on colour visualisation. The results were used to establish a best practice guide for designers wishing to obtain a more acceptable print-colour match.
Papers by Becky Gooby
Thesis Chapters by Becky Gooby
However, there are concerns about print-colour consistency and outcome. There is a gamut mismatch between the additive - mixing colours with light, and subtractive - mixing pigments or dyes, colour models used to reproduce colour on screen and in print. Numerous variables can alter colour outcome relating to textile chemistry, colour management, viewing conditions and printer technology. Yet colour accuracy is hugely important in the field of fashion and textiles, where colour is critical, and tolerance limits are competitive.
The research inquiry explored a number of variables to determine their influence on colour outcomes using a Practice-as-Research methodology to reflect the conditions and approach designers would employ. These practical experiments progressed into the development of a modality of visual colour methods, which aid a designer’s colour expectation knowledge; a Colour Reference Book, Digital Lab Dip tests presented as Colour Maps, and a set of Indicator ICC profiles generated from data accumulated through measuring printed-colour differences on a variety of substrates. The modality of visual prompts is intended to support designers to build their own ‘internal colour look-up table’, enabling users to predict and resolve colour issues during the design process.
The methods were applied in a real-world test case, using a body of colour work, inspired by archival research of the British Interwar period. The work has been presented as an Exhibition of Praxis, an online Project Tool-Kit, and a Written Report, which takes a traditional thesis format.
https://uwe-repository.worktribe.com/output/8704673/an-exploratory-study-of-methodologies-for-digital-colour-printing-in-textile-design-through-an-understanding-of-interwar-historical-colour-palettes
However, there is a marked difference between screen-colour to print-colour and software allows a user to select colours unprintable using CMYK colorants. Colour results are further affected by factors such as structure and composition of the fabric, dye type, printer communications, fabric pretreatments and secondary processes. A textile designer will be required to understand and experiment with a number of variables in order to feel colour confident.
These variables were considered, and existing colour management tools and methods evaluated, using a practice-as-research methodology. Experiments showed that neutral and achromatic colours were the most difficult to replicate, and hues with magenta/blue undertones were problematic. The choice of substrate had a sizeable impact on colour visualisation. The results were used to establish a best practice guide for designers wishing to obtain a more acceptable print-colour match.
However, there are concerns about print-colour consistency and outcome. There is a gamut mismatch between the additive - mixing colours with light, and subtractive - mixing pigments or dyes, colour models used to reproduce colour on screen and in print. Numerous variables can alter colour outcome relating to textile chemistry, colour management, viewing conditions and printer technology. Yet colour accuracy is hugely important in the field of fashion and textiles, where colour is critical, and tolerance limits are competitive.
The research inquiry explored a number of variables to determine their influence on colour outcomes using a Practice-as-Research methodology to reflect the conditions and approach designers would employ. These practical experiments progressed into the development of a modality of visual colour methods, which aid a designer’s colour expectation knowledge; a Colour Reference Book, Digital Lab Dip tests presented as Colour Maps, and a set of Indicator ICC profiles generated from data accumulated through measuring printed-colour differences on a variety of substrates. The modality of visual prompts is intended to support designers to build their own ‘internal colour look-up table’, enabling users to predict and resolve colour issues during the design process.
The methods were applied in a real-world test case, using a body of colour work, inspired by archival research of the British Interwar period. The work has been presented as an Exhibition of Praxis, an online Project Tool-Kit, and a Written Report, which takes a traditional thesis format.
https://uwe-repository.worktribe.com/output/8704673/an-exploratory-study-of-methodologies-for-digital-colour-printing-in-textile-design-through-an-understanding-of-interwar-historical-colour-palettes