Papers by Janakarajan Ramkumar
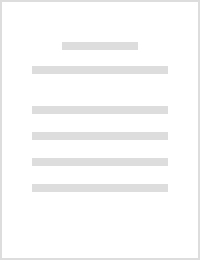
Journal of the Brazilian Society of Mechanical Sciences and Engineering
Machining of delicate thin members having extremely small thickness as compared to the other two ... more Machining of delicate thin members having extremely small thickness as compared to the other two dimensions is a precarious task when performed using conventional fabrication techniques. Non-contact machining process, such as micro-wire electrical discharge machining (micro-WEDM) process, an advanced means of machining, offers an appropriate way to machine thin-wall structures in an utmost precise manner. In the present work, thin-wall micromachining of Ti–6Al–4V is performed while utilizing the contactless, negligible thermal damage, and deformation-free nature of micro-WEDM process energized through the resistance–capacitance generator. The objective is to explore the feasibility of a minimum possible wall thickness. Performing the thin-wall micromachining using wire step-over approach, it is established that a wall of average thickness 8.47 µm with an end deflection and a wall of thickness about 15 µm free from end deflection is possible to fabricate using micro-WEDM process. It achieves a high aspect ratio of 70 corresponding to the minimum thickness of the wall. What’s more, a theoretical analysis is carried out to illustrate the functional relationship between wall-end deflection with workpieces’ thermophysical properties, discharge parameters, and the geometric parameters of the wall. Finally, the comparative assessment of wall-end deflection and volumetric material removal rate attained with three different materials, namely Ti–6Al–4V, mild steel, and SS-304, reveal that thermophysical properties of workpiece material play a critical role in determining the wall-end deflection and the resultant volumetric material removal rate.
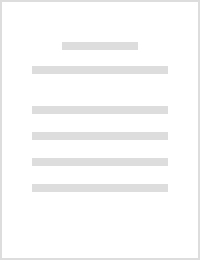
The good surface finish of gears is one of the critical parameters which leads to its noise-free ... more The good surface finish of gears is one of the critical parameters which leads to its noise-free operation, efficient power transmission, and longer service life. However, most of the gear manufacturing processes do not produce a good surface finish. Therefore, gears need post-processing to finish their surface. Out of several methods of gear finishing like gear grinding, lapping, and honing, the abrasive flow finishing process offers more flexibility due to its self-deformable abrasive medium which can easily flow across complex internal or external geometry. The present study aims to improve the surface finish of helical gear by abrasive flow finishing (AFF) by experimentally identifying the optimum range of the potential input process parameters. An AFF set up was used for gear finishing by using a medium of styrene-butadiene and soft silicone polymer, Silicon carbide abrasive, and silicone oil as a blending agent. A special fixture was developed comprising of five parts namely s...
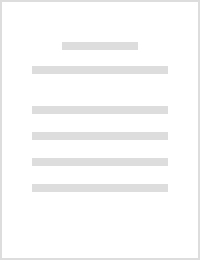
Electrical discharge machining is uttermost exploited material removal process broadly used in ma... more Electrical discharge machining is uttermost exploited material removal process broadly used in manufacturing industries for variegate shapes and difficult-to-machine electrically conductive materials. The nascent materials such as metal matrix composites, ceramic composites, duplex stainless steels, and titanium alloys have a vast demand in the area of automobiles, aircraft, aerospace, railways, and micro industries. The machining of these materials using conventional machining process is bonded to linear cutting to overcome this problem EDM was introduced. Many researchers have presented a vast work to understand the material removal mechanism of EDM and conclude that machining performance is mostly affected by process parameters. The machining performance can predict in appropriate way using process modeling techniques. The process modeling of materials like carbon nano-tube reinforced MMC is still needed a lot of research work. This paper includes review of AMC machining and expe...
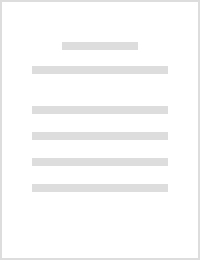
Materials and Manufacturing Processes
ABSTRACT This paper aims to examine the influence of nanoclay as secondary reinforcement in carbo... more ABSTRACT This paper aims to examine the influence of nanoclay as secondary reinforcement in carbon epoxy (CFRP) composite on the abrasive water jet machining (AWJM) response for the process parameters, namely, jet pressure (96 and 304 MPa), traverse rate (50, 100, and 150 mm/min), and nanoclay (0.00, 1.25, and 2.50 wt%). The most dominating parameters for AWJM response such as average surface roughness (Ra) characteristics, kerf taper (KT) formation, and material removal rate (MRR) of CFRP plates were investigated by adopting the Taguchi-based statistical method. ANOVA was utilized to obtain the influence of input factors on the process response. Traverse rate was attained as the most considerable factor for all the AWJM response. CFRP embedded with nanoclay showed relatively lower KT formation, Ra, and MRR than the CFRP laminate without nanoclay. Traverse rate with 150 mm/min showed higher Ra, KT formation and MRR compared to 50 and 100 mm/min. Jet pressure with 304 MPa showed lower Ra and KT formation while provided better MRR. The microstructure analysis of the machined surface was illustrated applying FESEM.
IEEE Antennas and Wireless Propagation Letters
International Journal of Hydrogen Energy
Resources, Conservation and Recycling
International Journal of Machine Tools and Manufacture
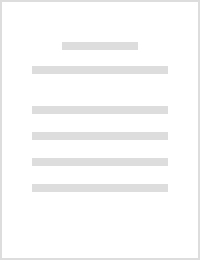
Surface and Coatings Technology
Abstract In the present work, electrodeposited chromium coatings were strengthened with 3 mol% yt... more Abstract In the present work, electrodeposited chromium coatings were strengthened with 3 mol% yttria-stabilised zirconia nanoparticles (YSZ) and carbon nanotubes (CNT) to analyse anti-corrosive and wear properties of the coatings. Highest hardness (~24 GPa), minimum scratch wear rate i.e. ~3 × 10−11 m3/Nm and highest corrosion resistance of ~3.9 kΩcm2 was obtained by synergistic incorporation of YSZ and CNT in Cr matrix. This can be linked to high dislocation density ~22 × 1011 cm−2 (Orowan effect) and compressive residual stresses i.e. ~840 MPa (Cr-YSZ-CNT), which tend to seal-up micro-holes and cavities, thereby, restricting the onset of wear and corrosion in the matrix. Addition of inert YSZ nanoparticles imparts chemical stability as well as hardness to the Cr matrix (~11 GPa for Cr-YSZ, ~8.4 GPa for Cr). Further, CNT incorporation, apart from matrix strengthening, results in low COF (~0.12) due to self-lubricating nature of CNTs, which leads to reduced wear rate of ~3.8 × 10−11 m3/Nm (Cr-CNT) with respect to Cr and Cr-YSZ. Thus, barrier protection and corrosion inhibition might be protective mechanisms for Cr-YSZ-CNT coating that make it suitable for engineering and industrial applications in order to protect the vital components exposed to tribological and corrosive media conditions.
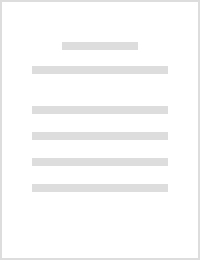
The International Journal of Advanced Manufacturing Technology
Abstract3-D components used in today’s industries need fine surface characteristics as a function... more Abstract3-D components used in today’s industries need fine surface characteristics as a functional requirement. Therefore, it is necessary to improve surface characteristics before putting them into useful applications, by achieving superior surface finish very close to dimensional precision. Magnetorheological fluid-based finishing processes are efficient in achieving ultrafine surfaces. This paper aims to explore the key quality performance of the magnetorheological finishing process in achieving nanolevel finish on Ti6Al4V discs. Sequential experimental design through statistical design of experiments was employed and response surface model was developed. Concentration of abrasive particles and wheel speed were considered as independent process parameters for the present study. To have uniform (or minimum variation) surface roughness values on the entire surface, a negative replica of the workpiece has been fabricated as a tool, and magnetic field was used to create magnetorheological effect. Using a template, surface roughness was measured at the same points before and after finishing. Initial Ra value was found to be the critical process parameter for finishing Ti6Al4V workpiece by magnetorheological finishing. % change in Ra is significantly affected by concentration of abrasive particles (≈50%) followed by initial Ra (≈ 38%). Finishing rate is significantly affected by initial Ra (≈61%) followed by concentration of abrasive particles (≈33%). An area roughness of 49 nm was achieved in the present study.
Nanomaterials and Energy
The design of ambient assistive technology, such as a wheelchair, is less explored from the engin... more The design of ambient assistive technology, such as a wheelchair, is less explored from the engineering design perspective compared with other products of similar platforms, such as bicycles and sm...
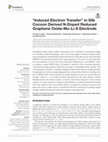
Frontiers in Materials
Developing 'carbon lithium sulfide composite (C-Li 2 S)' cathode is a promising strategy for Li-S... more Developing 'carbon lithium sulfide composite (C-Li 2 S)' cathode is a promising strategy for Li-S battery. Quite interestingly, when Li and S are caged in a heavily nitrogen-doped reduced graphene oxide (NDRGO) matrix derived from Tassar silk cocoon, the composite (NDRGO-Li-S) electrode behaves like a supercapacitor. In this work, we first optimized the concentrations of sulfur and then introduced molybdenum in the NDRGO matrix to develop a stable NDRGO-Mo-Li-2S (where 2 stands for 2M) composite electrode. The electrode design process utilized the concepts of "embedded redox couples" and "induced electron transfer"; a putative strategy to alter internal electron-shuttling kinetics for applications in various charge storage devices; where a time of electron-shuttling is the key. In NDRGO-Mo-Li-2S composite the charge transport occurs via "induced electron transfer," where Li + , is an external oxidant, provoking the inter atom electron transfer between Mo(VI), the internal oxidant, and S(-II), the internal reductant in Mo-S redox couple. This redox reaction is reversed using NDRGO, an external reductant inducing inter atom electron flow across [Mo(V)-(S2)] to complete the starting to product and back cycle. Such a redox cycle is competent for the flow of electrons in a lasting charge storage material through this unique bio-inorganic hybrid approach.
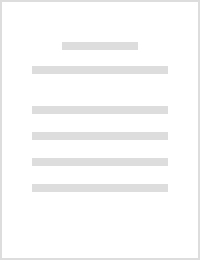
Journal of Alloys and Compounds
Abstract Conventional Cr as a protective coating on gun barrels is electro-deposited from toxic h... more Abstract Conventional Cr as a protective coating on gun barrels is electro-deposited from toxic hexavalent chromium electrolyte, which can be susceptible to cracking and tends to spall off. Herein, environment friendly trivalent Cr bath was utilized to electrodeposit chromium based composite coatings on armour steel with the incorporation of 3 mol% yttria stabilised zirconia (3YSZ) and carbon nano tubes (CNT). Higher dislocation density (17 × 1015 m−2), yield strength (4.6 GPa), calculated using Taylor's model, and reduced plasticity index (0.29) resulted in an enhanced hardness (∼25 GPa) and elastic modulus (∼206 GPa) for the synergistically incorporated YSZ and CNT in Cr matrix when compared to the Cr, Cr-YSZ and Cr-CNT coatings (using micro and nano-indentation techniques). Moreover, the fretting wear testing also elicited Cr-YSZ-CNT as most adroit coating having enhanced wear resistance (wear rate ∼3.7 × 10−5 mm3/Nm) due to the efficient presence of compressive stress (−918 MPa) and fine crystallite size (11 nm). The reduction in Hertzian contact diameter, from 32 μm for Cr to 27 μm for Cr-YSZ-CNT coating, results in a decreased tribological interaction between the counter body and coating material during the wear test. The mechanism involved in Cr-YSZ-CNT coating, grafted significantly with the mechanical and tribological performance, was attributed to toughening by YSZ nanoparticles that strengthen Cr matrix and impart higher resistance to crack-propagation during fretting wear. While the lubrication and bridging phenomenon of CNTs can potentially seal-up the initiation and propagation of cracks and pores within the matrix, thereby reducing the damage due to the wear. Thus, the dexterous mechanical and tribological performance of Cr-YSZ-CNT coating over Cr, Cr-YSZ and Cr-CNT coatings, makes it suitable composite material for gun barrel protection.
Journal of Materials Processing Technology
In this study, the transient evolution of temperature and velocity field, melt pool geometry (wid... more In this study, the transient evolution of temperature and velocity field, melt pool geometry (width, depth of penetration and melt pool volume), melting and solidification behavior during spot laser welding of 304 stainless-steel is presented. The transport phenomena associated with the melting and
Advanced Composites Letters
In this work, cold butt FRP joints were developed between two similar & dissimilar pipe materials... more In this work, cold butt FRP joints were developed between two similar & dissimilar pipe materials by winding up balanced glass fabric mats in varying orientation. The glass fabric mats were wetted with controlled quantity of resin and wound circumferentially at the place of joining. The strength of the cold butt joints was determined by flexural bend test, fatigue test and internal pressure leak test. It is clear from the experiments that the FRP joint strength is almost as good as the strength of the pipe material. The mechanisms of failure are also discussed.
Uploads
Papers by Janakarajan Ramkumar