Papers by Ashoka Varthanan P

Proceeding of 2nd International Colloquium on Computational & Experimental Mechanics (ICCEM 2021)
Polluting railway tracks causes a lot of problems to both environment and human beings. One of th... more Polluting railway tracks causes a lot of problems to both environment and human beings. One of the main problems in the railway is the wastages that are put by the passengers on the railway track. These wastages are collected from railway tracks by manual. Besides, it is also dangerous to work on the track. So, a special simple and innovative product are needed for collecting the scraps or wastes thrown nearby the railway track. This paper is to discuss the fabrication of a model to collect the wastage materials on the railway track without any manual effort to facilitate the clean operation on track by the robust design of waste collecting vehicles. This device is simple in design and low-cost innovative concept to clean the track. This vehicle design is not only used in railway track cleaning, it can also be used in a home or road cleaning.
Proceeding of 2nd International Colloquium on Computational & Experimental Mechanics (ICCEM 2021)
High velocity oxy fuel (HVOF) is a thermal surface alteration method which improves or restores t... more High velocity oxy fuel (HVOF) is a thermal surface alteration method which improves or restores the surface morphology or dimensions of a component, therefore extending equipment life by considerably enhancing erosion and abrasion resistance, as well as corrosion control. Using a high-temperature, relatively high stream materials are sprayed onto the surface, resulting in a thick spray coating that may be ground to a very high surface polish. The HVOF coating process permits the application of various coating materials to generate a coating with extraordinary hardness, excellent adherence to the substrate, and significant abrasion resistance and cathodic protection. In this study, some of the recent researches carried out using HVOF techniques and the research finding are explored

Proceeding of 2nd International Colloquium on Computational & Experimental Mechanics (ICCEM 2021)
This paper describes the fundamental needs of the centrifugal casting (CC) process. It is widely ... more This paper describes the fundamental needs of the centrifugal casting (CC) process. It is widely popular in foundries because of its simplicity and characteristics. CC is called as if the casting is produced with the help of the centrifugal force developed by the mould rotation. The true centrifugal casting (TCC) process is suitable for making hollow pipes, in which the centrifugal force provides good adhesion of molten metal on the mould's wall. From the literature, CC is a method for the production of bulk functionally graded materials (FGMs). Many kinds of research have been done on the CC process and some of the results have been discussed here. In the case of FGMs by CC, the gradation of harder particles with higher density was found in the outer region because of the centrifugal force, according to this gradation and the transition of materials, the mechanical and wear properties are changed from one place to another place along the specimen. For this phenomenon, the CC process is suitable for the production of automobile components. This paper provides the baseline knowledge about CC in classification, process variables and the characterisation, advantages and applications, and CC uses in research.

Journal for Manufacturing Science and Production, 2008
Aggregate production plan (APP) aims to attain the highest profit level by utilizing all the reso... more Aggregate production plan (APP) aims to attain the highest profit level by utilizing all the resources efficiently. Most of the industries today are generating the APP separately for each plant even though they produce the same family of products in all the plants. APP devised for the plants after allocating the demand for the corresponding plants based on gross production and distribution costs is not optimum. The industry must work towards meeting the forecasted demand by creating a medium-term plan considering all its plants simultaneously. In this paper, APP is generated using simulated annealing (SA) for a multi-factory model, where the same family of products is manufactured at different localities. Data collected from a bearing manufacturing company is fitted to the mathematical model developed in this case. The parameters of the APP, viz., period-wise workforce level, quantity to be produced in regular production, overtime hours, outsourcing, finished goods inventory status and number of products sent from each plant to the demand centers are all normalized towards the objective of cost minimization.
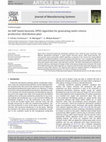
Journal of Manufacturing Systems, 2013
Multi-criteria integrated production-distribution problems were solved by many researchers using ... more Multi-criteria integrated production-distribution problems were solved by many researchers using different optimization techniques. A novel analytic hierarchy process (AHP) based heuristic discrete particle swarm optimization (DPSO) algorithm is proposed in this research for solving difficult production-distribution problems. A bearing manufacturing industry's case is considered in this paper and the mathematical model is formulated as mixed integer linear programming (MILP) problem considering multi-period, multi-product and multi-plant scenarios. The three major objectives considered are total cost reduction, minimization of change in labor levels and percentage under-utilization. The results of the AHP based heuristic DPSO algorithm are compared with the branch and bound algorithm results generated using LINGO software. The approach gives good near optimal solutions. In addition to the bearing manufacturing industry dataset, two other test datasets are also solved.

International Journal of Services and Operations Management, 2010
Industries adopting multisite manufacturing allocate their forecasted demand from various custome... more Industries adopting multisite manufacturing allocate their forecasted demand from various customers/demand centres to the respective plants based on gross production, inventory holding and distribution costs. But demand allocation (by considering the gross production cost) will not be appropriate, as production in each plant can be carried out through regular, overtime and outsourcing means. Also, this will lead to the allocation of the lion's share of demand to a plant whose regular production cost is cheaper, but its overtime/outsourced production costs may be costlier than the regular production cost of other plants. In this paper, an aggregate production-distribution plan considering all the abovementioned costs is developed for a renowned bearing manufacturing industry in India. The proposed Integer Nonlinear Programming (INLP) model is solved using a genetic algorithm and the results are compared with LINGO 8.0, a popular operations research software. The performance of the genetic algorithm is found to be superior to that of the LINGO 8.0 results.

The International Journal of Advanced Manufacturing Technology, 2011
Integrated production-distribution plan considering three major objectives, viz., total cost mini... more Integrated production-distribution plan considering three major objectives, viz., total cost minimization, change in labor level reduction, and underutilization minimization, is developed for a renowned bearing manufacturing industry in India. The total cost minimization objective minimizes the regular, overtime, and outsourced production costs along with inventory holding, backorder, hiring/layingoff, and trip-wise distribution costs. The multi-criteria model is solved using a novel simulation-based analytic hierarchy process (AHP)-discrete particle swarm optimization (DPSO) algorithm. The solutions of the AHP-DPSO algorithm are verified using the AHP-binary-coded genetic algorithm solutions. The proposed simulation-based AHP-DPSO solutions are found to be superior. Demand is assumed to vary uniformly, and the simulation-based AHP-DPSO algorithm is used for obtaining the best production-distribution plan that serves as a trade-off between holding inventory and back-ordering products. In addition to bearing manufacturing industry dataset, two other test datasets are also solved.
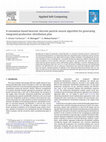
Applied Soft Computing, 2012
Deciding the strategy for production and distribution in a stochastic demand scenario is importan... more Deciding the strategy for production and distribution in a stochastic demand scenario is important for the manufacturing industries. An integrated production-distribution plan considering regular, overtime and outsourced production costs along with inventory holding, backorder, hiring/laying-off and tripwise distribution costs is developed for a renowned bearing manufacturing industry producing three types of products at three locations. Demand is assumed to vary uniformly and a novel simulation based heuristic discrete particle swarm optimization (DPSO) algorithm is used for obtaining the best production-distribution plan that serves as a trade-off between holding inventory and backordering products. The algorithm also uses an innovative regeneration type constraint handling method which does not require a penalty operator. In addition to the bearing manufacturing industry data set, two other test data sets are also solved. The simulation based optimization approach gives good approximate solutions for the stochastic demand problems.
Journal of Engineering, 2013
Engine performances and emission characteristics of Karanja oil methyl ester blended with diesel ... more Engine performances and emission characteristics of Karanja oil methyl ester blended with diesel were carried out on a variable compression diesel engine. In order to search for the optimal process response through a limited number of experiment runs, application of Taguchi method in combination with grey relational analysis had been applied for solving a multiple response optimization problem. Using grey relational grade and signal-to-noise ratio as a performance index, a particular combination of input parameters was predicted so as to achieve optimum response characteristics. It was observed that a blend of fifty percent was most suitable for use in a diesel engine without significantly affecting the engine performance and emissions characteristics.
In this present study, the effect of the shot peening process on fatigue life, surface hardness a... more In this present study, the effect of the shot peening process on fatigue life, surface hardness and corrosion properties of a low carbon alloy steel is examined at room temperature. The research article addresses the effect of shot peening by varying the process parameters such as peening distance and pressure with amachrome as shots. The experiment is designed by means of full factorial design. The experimental result reveals that the pressure and distance are the most significant factors in the shot peening process. The results illustrate that the average pressure of 7 bar and distance of 100 mm improves fatigue life by 1.5% of unpeened material under 20 Hz frequency while corrosion resistance improves by 4% with unpeening of the low carbon alloy steel by using amachrome as a shot.

The South African Journal of Industrial Engineering, 2013
This paper proposes a novel strategy to finalize the mould design of a specific cast component th... more This paper proposes a novel strategy to finalize the mould design of a specific cast component through the failure analysis using case study data of a foundry. Traditional failure mode and effect analysis (FMEA) is one of the effective tools for prioritizing the possible failure modes by calculating the Risk priority Number (RPN) of a process/design. But in foundries, prioritizing the failures through the traditional FMEA produces unmatched results when RPN values are identical during preproduction trials. Hence it is very difficult to finalize moulds design of a specific cast component using traditional FMEA approach. This research paper addresses an alternate FMEA approach named FEAROM (Failure Effects And Resolution of Modes) to resolve the difficulty in finalizing the mould designs. Analytical Hierarchy Process (AHP) is used for validating the results obtained using FEAROM method. The results presented are based on an experimental study carried out for a specific component in a foundry using the sand casting method. It is found that proposed FEAROM model matches well in practice and produces quality castings.
Uploads
Papers by Ashoka Varthanan P