Papers by Francesco Bellucci

International Journal of Astronautics and Aeronautical Engineering, 2021
Over the last years, in the context of the electric aircraft technology trend, the development of... more Over the last years, in the context of the electric aircraft technology trend, the development of electric brakes in replacing hydraulic systems has gained great interest due to its several potential benefits. Currently, materials for brakes for aircrafts range from the low-cost sintered friction pad/liner material vs sintered rotor disc material to the high cost carbon fiber material vs carbon fiber material. The subject of this work was developed in the framework of a European project (E-BRAKE) aimed at developing, manufacturing, testing, and qualifying an innovative Electro-Mechanical Braking actuation system for small aircraft application. This paper addresses the potential use of thermal spray technologies to produce a thin film of friction material onto low-carbon steel substrate to allow its use as potential composite material for the stators and rotors of brake units. In this research Stellite grade 1 (Cobalt-Chromium alloy), Colmonoy 6 (Nickel-Chromium alloy), Tungsten Carbide (Metal Ceramic composite) and Chromium Oxide (Oxide ceramic) coatings were deposited with two different thermal spray technologies, respectively the High Velocity Oxygen Fuel (HVOF) and the Atmospheric Plasma Spraying (APS), for the purpose of creating high friction and wear resistance composite coatings onto low-carbon steel substrate. Tribological properties (friction coefficient and wear rate), thermal conductivity, and diffusivity as well as metallographic structures and adhesion to the low-carbon steel substrate were evaluated to assess the potential use of the coatings as brake surface materials. The tribological and adhesion properties were evaluated by using a pin-on-disk high temperature Tribometer at 450 °C and a scratch test, respectively. The metallographic structures of the coatings were analysed with an Optical Microscope NIKON Eclipse 2150. Results obtained in this investigation show that all coatings exhibit high friction coefficients and low wear rates compared to the low-carbon steel substrate, good adhesion and a dense and solid microstructure. Furthermore, the Tungsten Carbide coating shows thermal conductivity and diffusivity higher than that of the low-carbon steel substrate. Findings reported in this study suggest that the thermal-sprayed Tungsten Carbide coating shows better properties than the other investigated coatings and, therefore, can be considered as a potential coating for brake materials. In fact, this coating shows dense and solid microstructures with a very low level of porosity (less than 1%), absence of un-melted particles, a very low presence of oxides and no cracks. In addition, the Tungsten Carbide exhibits: (i) The best adhesion to the low-carbon steel substrate with a very high critical load of detachment (around 65 N), (ii) Very high friction coefficient (0.84), and (iii) Very low wear rate. In the wear tests carried out on the Tungsten Carbide coatings, it was impossible to evaluate the wear tracks because the surface of the coating was only flattened. Lastly, Tungsten Carbide presents superior thermal properties compared to that exhibited by the low-carbon steel substrate.

Metals, 2017
Self-organized TiO2 nanotube layer has been formed on titanium screws with complex geometry, whic... more Self-organized TiO2 nanotube layer has been formed on titanium screws with complex geometry, which are used as dental implants. TiO2 nanotubes film was grown by potentiostatic anodizing in H3PO4 and HF aqueous solution. During anodizing, the titanium screws were mounted on a rotating apparatus to produce a uniform structure both on the peaks and on the valleys of the threads. X-ray diffraction (XRD), Scanning electron microscopy (SEM), Energy dispersive X-ray (EDX) and electrochemical characterization were used to evaluate the layer, chemical composition and electrochemical properties of the samples. Aging in Hank’s solution of both untreated and nanotubes covered screw, showed that: (i) samples are covered by an amorphous oxide layer, (ii) the nanotubes increases the corrosion resistance of the implant, and (iii) the presence of the nanotubes catalyses the formation of chemical compounds containing Ca and P.

Surface and Interface Analysis, 2012
Corrosion fatigue is defined as the sequential stages of metal damage that evolve with accumulate... more Corrosion fatigue is defined as the sequential stages of metal damage that evolve with accumulated load cycling, in an aggressive environment, and resulting from the interaction of irreversible cyclic plastic deformation with localized chemical or electrochemical reactions. It appears then evident the need to know and understand all phenomena that are involved in pit formation and growth in the presence of both an aggressive environment and a cyclic load. Although each single effect of both fatigue and corrosion have been extensively documented for aluminium alloys, their synergic action is not thoroughly understood and it continues to be an area of considerable scientific and industrial interest. Fatigue experiments were conducted on bare AA 2024 T3 aluminium alloy specimens in the presence of an aggressive environment consisting of a water aerated solution with 3.5% of NaCl in weight. The specimen was stressed in a four-point bending test; the upper surface of the specimen, experiencing only tensile stress, was the monitored one. True strain on this surface was monitored by means of fibre optic Bragg grating. The strain and open circuit potential variations observed as a function of number of cycles are interpreted as a result, and taking into account the numerous and complex phenomena occurring as time goes on. The pits birth and their subsequent growth seem to play a significant role in crack initiation and subsequent propagation up to final catastrophic failure. This has been verified also by means of finite element method analysis.
Corrosion Reviews, 2007
Friction Stir Welding (FSW) is a relatively new technology that was developed at The Welding Inst... more Friction Stir Welding (FSW) is a relatively new technology that was developed at The Welding Institute (TWI) in 1991. It is a solid phase process that operates at temperatures below the melting point of the materials being joined. All aluminium alloys can be welded, including some that cannot be joined by conventional fusion techniques such as Tungsten Inert Gas (TIG). Compared to fusion welding, the relatively low temperatures involved in FSW reduce thermal stresses and distortion. There is substantial potential for employing FSW during the fabrication of various components within the aerospace, shipbuilding, and automotive industries. As these welds may experience diverse aggressive environments, it is crucial to understand the degradation characteristics. This paper looks at some of the key technological issues relevant to the joining of li»ht alloys.
Dental Cadmos, 2014
Valutazione della rugosità degli impianti dentali in titanio Assessing the roughness of titanium ... more Valutazione della rugosità degli impianti dentali in titanio Assessing the roughness of titanium dental implants Ricevuto il 15 luglio 2013 Accettato il 4 novembre 2013
Electrochemical and Solid-State Letters, 1999
A novel magnetic approach is introduced to measure the corrosion rate of bare and coated ferromag... more A novel magnetic approach is introduced to measure the corrosion rate of bare and coated ferromagnetic materials. The corrosion of bare and acrylic-coated cobalt is monitored in situ and in real-time by coupling electrochemical impedance spectroscopy (EIS) and saturation magnetic moment measurements using a vibrating sample magnetometer (VSM). For the first time, the corrosion rate beneath a polymer coating is measured accurately in situ; additionally, it is suggested that the VSM can be used to enhance the interpretation of EIS data.
Corrosion Science, 2009
Correlation between electrochemical impedance measurements and corrosion rate of magnesium invest... more Correlation between electrochemical impedance measurements and corrosion rate of magnesium investigated by real-time hydrogen measurement and optical imaging, Electrochimica Acta http://dx.

npj Materials degradation, Sep 18, 2017
Water reduction, which leads to the evolution of hydrogen, is a key cathodic process for corrosio... more Water reduction, which leads to the evolution of hydrogen, is a key cathodic process for corrosion of many metals of technological interest such as magnesium, aluminium, and zinc; and its understanding is critical for design of new alloys or protective treatments. In this work, real-time hydrogen evolution measurement was coupled with potentiodynamic measurements on high-purity aluminium and AA2024-T3 aluminium alloy. The results show that both materials exhibit superfluous hydrogen evolution during anodic polarisation and that the presence of cathodically active alloying elements enhances hydrogen evolution. Furthermore, it was observed for the first time that superfluous hydrogen evolution also occurs during cathodic polarisation. Both the anodic and cathodic behaviours can be rationalised by a model assuming that superfluous hydrogen evolution occurs locally where the naturally formed oxide is disrupted. Specifically, during anodic polarisation, oxide disruption is due to the combined presence of chloride ions and acidification, whereas during cathodic polarisation, such disruption is due to alkalinisation. Furthermore, the presence of cathodically active alloying elements enhances superfluous hydrogen evolution in response to either anodic or cathodic polarisation, and results in 'cathodic activation' of the dissolved regions.
Metallography, Microstructure, and Analysis, May 5, 2016
The changes in microstructure during the forging of a large Ti-5-5-5-3 component are studied. The... more The changes in microstructure during the forging of a large Ti-5-5-5-3 component are studied. The effect of the different plastic strain and cooling rates experienced by the various zones of the component is analyzed and compared in terms of the microstructures that they induce. The results show that the microstructures vary in the different zones of the forging with the α phase spheroidization increasing with the amount of plastic strain sustained by the material. A correlation between the level of α phase spheroidization and the plastic softening of the forging has been found.
Surface & Coatings Technology, 2017

Journal of Applied Electrochemistry, 1986
The electrochemical behaviour of graphite-epoxy composite materials (GECM) in neutral 3.5~ aqueou... more The electrochemical behaviour of graphite-epoxy composite materials (GECM) in neutral 3.5~ aqueous solutions of NaC1 has been investigated. Two types of composite and pure graphite have been studied. The composite material shows a high value of electrode potential ranging between-40 and + 70 mV versus SCE, and behaves as cathode when coupled to alloys. The effects of chloride ion concentration, pH, temperature, nature of cations and anions, ancl resistance of the epoxy matrix to environmental agents on the rate of oxygen reduction reaction on GECM electrodes are reported. Moreover, polarization studies performed on GECM-aluminium alloy couples show that polarization occurs mainly at the composite interface. From potentiostatic anodic polarization curves of different alloys and cathodic polarization curves of GECM, the initial galvanic corrosion current densities for most alloy-GECM couples of interest in the aerospace industries have been obtained, These values are strongly affected by environment durability of the epoxy matrix and variation by one or two orders of magnitude are observed. Despite the latter discrepancy, these data can be helpful in the assesment of a galvanic series based on galvanic current density for alloy-GECM joints.
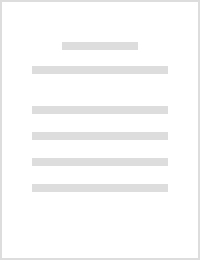
Key Engineering Materials, 2016
A company recently reported, the unexpected and sudden failure of several containers, fabricated ... more A company recently reported, the unexpected and sudden failure of several containers, fabricated from aluminium 8006 and sealed using a polymeric film. The failure resulted when there was a loss of adhesion at the metal/polymeric lid interface, making the containers unusable. Some preliminary adhesion tests have highlighted that, containers, coming from various production batches and sealed using the same kind of lid, exhibited different adhesion strengths. To investigate the cause of the detachment of the lid from the edge of the container, the following parameters has been considered: (i) the iron content of the Al alloy, (ii) the effect of lubricant oil at the polymeric film/substrate interface, (iii) the topography of the contact surface between the lid and the container. The electrochemical behaviour of Al8006 was investigated by means of potentiodynamic polarization tests, both in an aerated aqueous solution of Na2SO4 (0.5 M) and in an aerated aqueous solution of NaCl (0.6 M)....

Recently, the use of graphene as a conductive nanofiller in the preparation of inorganic/polymer ... more Recently, the use of graphene as a conductive nanofiller in the preparation of inorganic/polymer nanocomposites has attracted increasing interest in the aerospace field. The reason for this is the possibility of overcoming problems strictly connected to the aircraft structures, such as electrical conductivity and thus lightning strike protection. In addition, graphene is an ideal candidate to enhance the anti-corrosion properties of the resin, since it absorbs most of the light and provides hydrophobicity for repelling water. An important aspect of these multifunctional materials is that all these improvements can be realized even at very low filler loadings in the polymer matrix. In this work, graphene nanoflakes were incorporated into a water-based epoxy resin, and then the hybrid coating was applied to Al 2024-T3 samples. The addition of graphene considerably improved some physical properties of the hybrid coating as demonstrated by Electrochemical Impedance Spectroscopy (EIS) analysis, ameliorating anti-corrosion performances of raw material. DSC measurements and Cross-cut Test showed that graphene did not affect the curing process or the adhesion properties. Moreover, an increment of water contact angle was displayed.
Journal of Applied Electrochemistry
The electrochemical and corrosion behaviour of 6013-T6, 2024-T3 aluminium alloys and pure alumini... more The electrochemical and corrosion behaviour of 6013-T6, 2024-T3 aluminium alloys and pure aluminium in 0.6m NaCl and 0.3m Na2SO4 aqueous solutions was investigated using d.c. and a.c. electrochemical techniques. Results show that the 6013-T6 alloy exhibits superior corrosion resistance compared with that exhibited by the 2024-T3 alloy in both environments. These findings were interpreted on the basis of a barrier oxide film model.
ABSTRACT Restoration or seismic upgrading of historic structures requires special attention in te... more ABSTRACT Restoration or seismic upgrading of historic structures requires special attention in terms of type and implementation modes. In particular, in cases where steel elements are coupled to the walls of tuff. The paper presents a case study of realization of steel arches in support tufa masonry. After about ten years, steel arches are suffering about corrosion problems leading to plaster cracking. Half-cell potential of steel, relative humidity and chloride content tests have been performed in order to understand causes that triggered corrosion process. Cold spray technology treatment of steel has been performed in order to protect steel and dehumidifying and breathable plaster has been used in order to promote drying of the walls of tufa.
ABSTRACT Due to the presence of degradation on reinforced concrete structures, the concept of dur... more ABSTRACT Due to the presence of degradation on reinforced concrete structures, the concept of durability and service life of structures has been introduced in recent codes. The corrosion of reinforcement, a major cause of degradation, is not mainly related the appearance of structures, but to the structural safety. The consequences of corrosion of reinforcement are: (i) reduction of the cross section of the reinforcement, (ii) formation of corrosion products leading to loss of bond with concrete, (iii) appearance of cracks in the concrete cover and subsequent spalling.
Uploads
Papers by Francesco Bellucci