Papers by N. Fanciullacci
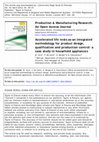
Cost reduction and product quality are key factors in the present competitive market. Product rel... more Cost reduction and product quality are key factors in the present competitive market. Product reliability is strongly correlated with customer satisfaction. Accelerated life tests (ALTs) represent a methodology able to investigate product reliability performance in a short time with respect to the classical testing methods in the design. The aim of this paper is the proposal and development of an integrated procedure based on ALTs in order to evaluate the reliability performance of a new product; the use of such testing methods is useful to systematically support the design and qualification phases and to help the service demand forecasting before the product launch. The smart choice of the acceleration parameter and the knowledge developed during the upstream phase in the product lifecycle can be useful and cost effective for its utilization in the downstream lifecycle, as an acceptable substitute of specific advanced final inspection methodologies. The methodology has been tested during the development of a new model of washing machine. The application of ALTs was able to stress one of the most important failure modes of the product, returning important validation data for the design phase and qualification phase and giving good expectation for its fruitful utilization for final inspection in production.
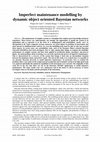
The maintenance of complex systems is a discipline that requires great knowledge and great experi... more The maintenance of complex systems is a discipline that requires great knowledge and great experience. These factors are, unfortunately, not enough: the opportunity to model the system to be maintained and to represent it in the form of a mathematical and probabilistic model, can't be disregarded at all. These composite systems, moreover, are often subject to problems of uncertainty and must operate in multifunctional contexts. So, even the modelling tools must be able to take into account these aspects. In recent years, new probabilistic tools, such as the Dynamic Object oriented Bayesian Networks (DOOBNs), have been developed. They're able, among other things, to estimate the reliability performance of complex systems and have been applied in production plants, machinery and process plants. An usual problem, often occurring, is to correctly represent the process of imperfect maintenance. This is characterized by a recovery of the system that brings it back into an intermediate situation between the minimum repair and perfect repair. The aim of this study is to evaluate how it is possible to use dynamic Bayesian networks to model imperfect maintenance. In particular, first we studied the problem, then a case study on the compressed air production and treatment system of an high speed train was analysed and finally the analytical capabilities of the instrument were assessed. The originality of this work lies in the fact that there are not in the literature DOOBN applications to model imperfect maintenance. The study results were very satisfactory and in the future it will be necessary to better investigate what are the limits and the potentials of the instrument.

Companies competing in an increasingly competitive market must ensure the production of goods wit... more Companies competing in an increasingly competitive market must ensure the production of goods with excellent performance, able to satisfy their customers and which have low manufacturing and management costs. It is in this context that companies have, in recent years, invested in research and development and have upgraded their reliability and maintenance functions. In many cases, the maintenance engineers have attempted to predict the reliability of the products, at least for evaluating the number of warranty repairs to be performed. This approach is on the one hand, extremely appropriate but, on the other, must face the difficulties of making laboratory test in conditions often radically different from those that the products meet during their normal operation. Frequently, the reliability estimation, coming from experimental test (in-house) are different from those obtained by the analysis of the service data (in-field). The former are executed in laboratory with standardized, con...

Companies competing in an increasingly competitive market must ensure the production of goods wit... more Companies competing in an increasingly competitive market must ensure the production of goods with excellent performance, able to satisfy their customers and which have low manufacturing and management costs. It is in this context that companies have, in recent years, invested in research and development and have upgraded their reliability and maintenance functions. In many cases, the maintenance engineers have attempted to predict the reliability of the products, at least for evaluating the number of warranty repairs to be performed. This approach is on the one hand, extremely appropriate but, on the other, must face the difficulties of making laboratory test in conditions often radically different from those that the products meet during their normal operation. Frequently, the reliability estimation, coming from experimental test (in-house) are different from those obtained by the analysis of the service data (in-field). The former are executed in laboratory with standardized, controlled and repeatable conditions, while the latter are affected by random environmental and operating conditions. In the field of household appliances, this is so true that the conditions of use may vary even from country to country. There are some approaches that allow to assess the reliability performance of a system starting from the results of experimental tests performed in a laboratory. One of these was proposed some years ago and is called systemability. In this study, it was applied, for the first time, this approach to the field of household appliances. In addition, we wanted to try to identify the parameters that allowed to distinguish two different European markets. In fact the in-field data come from two different countries and could be considered a great opportunity to validate the correlation model. In fact, it was possible to investigate the effects of two different environmental condition sets (costumer behaviours, , market issues, logistics, etc.) on the reliability performances of a product population that has been manufactured in the same industrial plant. One of the most important outcomes of the Systemability model was the capacity to predicts two different in-field reliability performances relative to two different markets in contrast with the classic methodology that uses the same in-house reliability data without considering environmental effects. The initial stage of modeling was followed by a second validation phase, which gave satisfactory results. The overall outcomes were very positive and they have allowed us to focus some improvements in maintenance management that will lead to greater effectiveness of the method in the coming years.
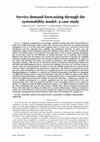
Companies competing in an increasingly competitive market must ensure the production of goods wit... more Companies competing in an increasingly competitive market must ensure the production of goods with excellent performance, able to satisfy their customers and which have low manufacturing and management costs. It is in this context that companies have, in recent years, invested in research and development and have upgraded their reliability and maintenance functions. In many cases, the maintenance engineers have attempted to predict the reliability of the products, at least for evaluating the number of warranty repairs to be performed. This approach is on the one hand, extremely appropriate but, on the other, must face the difficulties of making laboratory test in conditions often radically different from those that the products meet during their normal operation. Frequently, the reliability estimation, coming from experimental test (in-house) are different from those obtained by the analysis of the service data (in-field). The former are executed in laboratory with standardized, controlled and repeatable conditions, while the latter are affected by random environmental and operating conditions. In the field of household appliances, this is so true that the conditions of use may vary even from country to country. There are some approaches that allow to assess the reliability performance of a system starting from the results of experimental tests performed in a laboratory. One of these was proposed some years ago and is called systemability. In this study, it was applied, for the first time, this approach to the field of household appliances. In addition, we wanted to try to identify the parameters that allowed to distinguish two different European markets. In fact the in-field data come from two different countries and could be considered a great opportunity to validate the correlation model. In fact, it was possible to investigate the effects of two different environmental condition sets (costumer behaviours, , market issues, logistics, etc.) on the reliability performances of a product population that has been manufactured in the same industrial plant. One of the most important outcomes of the Systemability model was the capacity to predicts two different in-field reliability performances relative to two different markets in contrast with the classic methodology that uses the same in-house reliability data without considering environmental effects. The initial stage of modeling was followed by a second validation phase, which gave satisfactory results. The overall outcomes were very positive and they have allowed us to focus some improvements in maintenance management that will lead to greater effectiveness of the method in the coming years.
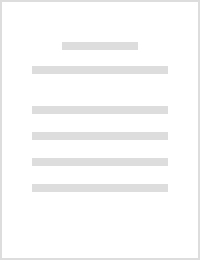
ABSTRACT Abstract: The increasing competition of global markets requires companies to focus their... more ABSTRACT Abstract: The increasing competition of global markets requires companies to focus their attentions on two main aspects of a production system: cost reduction and product quality. Product reliability performance is strongly correlated with the customer satisfaction and with its perception of the goods quality; in fact, product failures can represent one of the most serious damages for the manufacturer image. Reliability estimation through testing activities should be carried on in accordance with a time&cost saving strategy looking also at the product warranty period. Accelerated life tests (ALT) represent a methodology able to investigate product reliability performance in a shorter time respect to the classical testing methods, both in the design and in the production phase. The aim of this paper is the development of a procedure based on ALT in order to evaluate reliability performances of a new product; the use of such testing method is useful to systematically support the design phase and to help the service forecasting before the product launch. The methodology has been tested on a case study regarding a new model of washing machine for domestic use. The application of accelerated life tests was able to stress one of the most important failure mode of the product, returning important validation data for the design phase.
Uploads
Papers by N. Fanciullacci