Papers by Silvia Maria Hoyos
Hoja de Vida nos cuenta en cinco historias cortas, las hojas de vidas sindicales y humanas de Héc... more Hoja de Vida nos cuenta en cinco historias cortas, las hojas de vidas sindicales y humanas de Héctor, Amanda, Oswaldo, Hernando y Teresa. Cinco líderes sindicales víctimas de la violencia, que han perdido amigos y parientes a manos de guerrilleros, paramilitares, fuerzas del Estado, que han perdido su vida íntima, incluso sus más cotidianos gustos. Estos hombres y mujeres pertenecen a los cinco sectores del sindicalismo más golpeados por la violencia: el magisterio, la minería, los servicios de salud, los trabajadores de la agroindustria y los entes territoriales, estos dos últimos agrupando a trabajadores y trabajadoras del Urabá y el Suroeste Antioqueños. Tercera parte- Documental de la realizadora Antioqueña Silvia María Hoyos sobre la violencia antisindical en Colombia. Producido para la Escuela Nacional Sindical
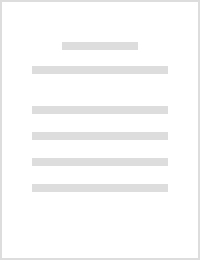
Journal of the Brazilian Society of Mechanical Sciences and Engineering, 2016
In this paper, a new simple analytical model for perforation process of composite sandwich panels... more In this paper, a new simple analytical model for perforation process of composite sandwich panels subjected to high-velocity impact of flat-ended projectile is presented. The panels consist of foam core sandwiched between two composite skins. In the analytical model, global deformation, plug shearing or localized tensile fracture, delamination of front and back-up composite skins, and the absorbed energy during the perforation of the sandwich panel are calculated considering the local indentation and also the energy balancing equation is employed to determine the ballistic limit and residual velocity of projectile. The results of current new model are compared with the experimental results available in the open literature and the finite element simulation results obtained by the LS-Dyna code. A good agreement is observed between the analytical and numerical model results and the experimental results.
In this paper, a new analytical model has been presented for energy absorption of aluminum-foam s... more In this paper, a new analytical model has been presented for energy absorption of aluminum-foam sandwich panels under ballistic impact. The panels consist of foam core sandwiched between two aluminum skins. In analytical model two types of sticker including cylindrical projectile with flat and hemispherical ended have been considered. It is supposed that aluminum skins failure by mean resistive pressure. Also foam absorbed a partial of projectile energy by crushing. Energy absorption of aluminum-foam sandwich panel is calculated and energy balancing equation has been employed for determination the ballistic limit and residual velocity of projectiles. The results of ballistic limit and residual velocity computed by new model have good agreement with experimental results. Also the effects of projectile mass and diameter in energy absorption of sandwich panel has been investigated.
�������������������� � ������������������������ �� � ������ �� ���� !�� " �#��$���� �%&%... more �������������������� � ������������������������ �� � ������ �� ���� !�� " �#��$���� �%&% �'()�� *+ � ��,� &�� ��������� � *+ ������ ������������������������������ ���� ���� ��� � �������� � "��� # $% �� � � � ���� � ���� �� ��������� � �� �� �� �� �� � ������������ �� � � �� � �� � � ���� ������ �� � � �� � �� ! � �� ��&' �� ,�;�� ��� � � � ��� � � � ��
Journal of Mechanical Science and Technology, 2015
ABSTRACT Thermal elastic-plastic finite element method has been employed to predict residual stre... more ABSTRACT Thermal elastic-plastic finite element method has been employed to predict residual stress and deformation in a T-Fillet welded joint. An uncoupled thermal-mechanical three-dimensional (3-D) model has been developed. A nonlinear-transient heat flow analysis was used to obtain the temperature distribution; then by applying thermal results in the three dimensional elastic-plastic model, residual stress and deformation distribution were obtained. Experiments were carried out to find fusion zone dimensions and displacement. Two heat source models with infinite speed are proposed and the mechanical result of the mentioned models and normal moving heat source are compared.
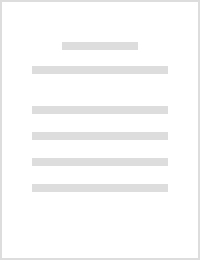
ABSTRACT This study is involved on modeling a standard welding procedure specification (SWPS) for... more ABSTRACT This study is involved on modeling a standard welding procedure specification (SWPS) for a multi pass weld of pipes, and the effect of increase in electrode velocity on thermal cycle and induced residual stress have been investigated. A double ellipsoidal model for weld heat source density and an appropriate coordinate system with a rotation around the pipe is adopted to simulate properly the sequence of weld properly. A 3D finite element analysis (FEA) is carried out using a commercial code and the validation of the model is confirmed by previous works. Temperature-dependent thermo-mechanical behavior for material properties and birth and death technique for elements of deposited filler layer are employed to model the weld. By a thermal analysis and uncouple residual stress the peak temperature, cooling rate, weld pool geometry and induced residual stress in heat affected zone (HAZ) are evaluated. The results indicate that peak temperatures against the time reasonably follows the sequence of weld and by increasing electrode velocity, the value of peak temperatures in a certain point of HAZ is reduced. The final hoop residual stress pattern for points underlying in HAZ influenced by the rise in electrode velocity, however the axial residual stress seems to be more influenced.
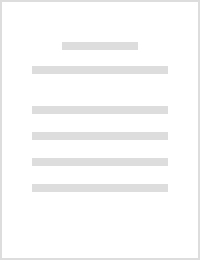
Journal of Pressure Vessel Technology, 2012
In this paper, a finite element simulation, based on abaqus software is presented for analyzing t... more In this paper, a finite element simulation, based on abaqus software is presented for analyzing the temperature history and the residual stress states in multipass welds in stainless steel pipe. The uncoupled thermal–mechanical a three-dimensional (3D) model and a two-dimensional (2D) model are developed. The volumetric heat source with double ellipsoidal distribution for front and rear heat source, proposed by Goldak and Akhlaghi, has also been used. Furthermore, a moving heat source has been modeled by abaqus subroutine DFLUX. A user subroutine FILM has also been used to simulate the combined thermal boundary conditions. The results of both a 3D model and a 2D axisymmetric model which are compared with the available experimental measurements show good agreements. Predictions show that the axial and hoop residual stresses in a 3D model and a 2D axisymmetric model have the same distributions in all locations except the starting point of welding. The effects of welding sequences on t...
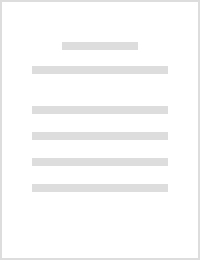
Journal of Pressure Vessel Technology, 2012
In this paper, the effect of hydrostatic testing internal pressure on the residual stresses of ci... more In this paper, the effect of hydrostatic testing internal pressure on the residual stresses of circumferentially butt-welded steel pipes is investigated by a three dimensional finite elements simulation based on ansys11 code. Residual stresses due to welding process are calculated by an uncoupled analysis. In this analysis, at first, a transient heat transfer problem is solved. Output of this analysis is temperature distribution history .This output is used as the structural analysis load. Output of structural analysis is welding residual stresses. The most important part of such simulations is modeling of heat power source. In the present work, heat power of welding electrode is simulated by a moving heat source with Gaussian distribution on a spherical domain. The presented model is used for calculation of residual stresses in an 8 in. three pass butt-welded steel pipe. Finally, the effects of hydrostatic testing internal pressure on the residual stresses are studied by the propos...
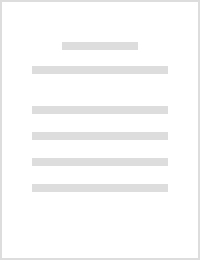
International Journal of Pressure Vessels and Piping, 2014
ABSTRACT Preheat effect on thermal cycle and residual stress was studied by employing a 3D finite... more ABSTRACT Preheat effect on thermal cycle and residual stress was studied by employing a 3D finite element method. A circumferential multi-pass butt weld of pipes based on ASME section IX was investigated and the experiment for thermal cycle validation was carried out. A spherical heat source density with a Gaussian distribution was employed and by an appropriate coordinate system, the rotation of electrode around the pipe was modeled reasonably. Sequentially coupled, thermal-mechanical analysis was applied using temperature-dependent thermo-mechanical behavior for material properties and the variation in peak temperature, cooling rate, and the axial residual stress due to the preheat effect were evaluated. The simulation results revealed that the pattern of final residual stress was influenced by the preheat temperature. However the thermal cycle experienced in the welding zone seems to be significantly affected by the preheat temperature.
International Journal of Impact Engineering, 2010
In this paper based on Zaera and Sanchez-Galvez [4] model, a new analytical model has been presen... more In this paper based on Zaera and Sanchez-Galvez [4] model, a new analytical model has been presented for penetration of deformable projectiles into ceramic–metal targets. By considering erosion and flattening of projectile tip, the one-dimensional equation of motion has been established. The momentum equation has been employed to describe the fragmented ceramic conoid. Considering work hardening material behavior, energy conservation
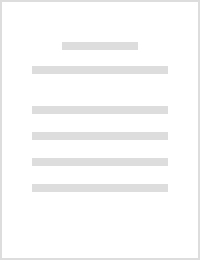
Computational Materials Science, 2010
ABSTRACT In thermal spray coating deposition, the layers of coating are built up by splatting of ... more ABSTRACT In thermal spray coating deposition, the layers of coating are built up by splatting of hot metal droplets onto a cold work piece, flattening of these droplets and ultimately their solidification. The extent of flattening and the pressure evolved during the process are effective on the mechanical properties and bonding strength of the coating layer. In this investigation, the impact of a fully molten metal particle on the surface is simulated using a commercial finite element package, LS-DYNA, in which a 2D axisymmetric domain for deformation is assumed. The equation of momentum is established for the deformed particle in a Lagrangian frame and explicit solution is applied using shell elements. It was revealed that the extent of deformation and the pressure profile evolved during the splatting and changed by variations in stress–strain and pressure–density of material. Null material model for the stress–strain behavior of fully molten metal droplet, and Mie-Gruneisen pressure–density model give reasonable results, particularly for the prediction of the extent of material at the initial time of splatting process. In addition, the particles impacted at a higher velocity are more extended at a shorter time. Null material behavior and Mie-Gruneisen pressure–density relationship represented to be an appropriate material model for fully molten metal droplets impacting at a high speed.

Composites Part B: Engineering, 2011
In this paper, based on LS-Dyna code, a new finite element (FE) simulation of the ballistic perfo... more In this paper, based on LS-Dyna code, a new finite element (FE) simulation of the ballistic perforation of the ceramic/composite targets, which impacted by cylindrical tungsten projectiles, has been presented. Research on this method has been conducted by a few research groups in recent years. The ceramic material, which is the front plate, has been made of Alumina 99.5% and composite backup plate composed of Twaron fibers. The 2-dimensional (2D), axi-symmetric, dynamic-explicit, Lagrangian model has been considered in this simulation. The Johnson-Cook, Johnson-Holmquist and Composite-Damage materials behaviors have been used for projectile, ceramic and composite materials respectively. The brittle fracture and fragmentation of ceramic conoid, the failure criteria based on fracture of fibers or matrixes of composite materials and erosion or flattening of projectile during perforation have been considered. The residual velocity and perforation time has been obtained and compared with the available analytical models. The results show that when the ceramic is impacted by a projectile, a fragmented ceramic conoid breaks from ceramic tile and the semi-angle of ceramic conoid with increasing initial velocity decreases. Furthermore, the dishing of composite layers at high impact velocities and the delamination of layers near the ballistic limit velocity decrease.

Composites Part B: Engineering, 2012
In this paper, an analytical model for perforation of composite sandwich panels with honeycomb co... more In this paper, an analytical model for perforation of composite sandwich panels with honeycomb core subjected to high-velocity impact has been developed. The sandwich panel consists of a aluminium honeycomb core sandwiched between two thin composite skins. The solution involves a three-stage, perforation process including perforation of the front composite skin, honeycomb core, and bottom composite skin. The strain and kinetic energy of the front and backup composite skins and the absorbed energy of honeycomb core has been estimated. In addition, based on the energy balance and equation of motion the absorbed energy of sandwich panel, residual velocity of projectile, perforation time and projectile velocity have been obtained and compared with the available experimental tests and numerical model. Furthermore, effects of composite skins and aluminium honeycomb core on perforation resistance and ballistic performance of sandwich panels has been investigated.
Composite Structures, 2011
An analytical model has been developed in this paper for perforation of ceramic/multi-layer woven... more An analytical model has been developed in this paper for perforation of ceramic/multi-layer woven fabric targets by blunt projectiles. In previous Chocron–Galvez analytical model the semi-angle of ceramic conoid is constant and the strain rate effects are also neglected in the stress–strain behavior of the yarns and only strain energy absorbed by the yarns is considered.In this paper which is
Uploads
Papers by Silvia Maria Hoyos