Papers by Thananan Akhadejdamrong
Journal of the Ceramic Society of Japan Supplement, 2004
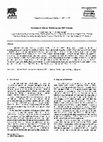
Journal of Materials Processing Technology, 1997
The densification of silicon nitride was carried out by Hot Isostatic Press (HIP) sintering via g... more The densification of silicon nitride was carried out by Hot Isostatic Press (HIP) sintering via glass-encapsulation method. The sintering performing techniques were studied in order to obtain high strength properties. a-Si:JN4 raw powder was used as the starting material in addition with a composition of 3 wt% Ah03 and 5 wt% Y203 . That ratio corresponds to the liquid phase compositions at the lowest temperature in the system Ah03 -Y203 -Si0 2 with having high strength at room temperature. Density, microstructure, hardness and fracture surface of specimens were measured. The experimental results showed that silicon nitride could have density nearly to theoretical density. X-ray Diffraction pattern indicated the transformation of a-phase to J3-phase occurred in every sintered specimens and fully transformed to J3 phase after complete soaking for 2 hrs. The development of elongated grains was related to the formation of large nuclei during phase transformation. The SEM micrographs and fractograph also showed the J3 rodlike grain. For the specimens having density over than 95%, the calculated hardness was appoximately between 14-16 GPa.

Materials Transactions, 2002
A protective nanocrystalline aluminum oxide layer forms during oxidation of Al-implanted TiN thin... more A protective nanocrystalline aluminum oxide layer forms during oxidation of Al-implanted TiN thin film coating on stainless steel substrate. TiN itself has poor chemical stability at elevated temperatures in an oxidizing atmosphere. Implantation of Al-ions to a TiN film, prepared by hollow cathode discharge ion plating (HCD-IP), at 4.5 × 10 17 ions·cm −2 has greatly improved thermal oxidation resistance at temperatures up to 973 K and for periods up to 20 h in a pure oxygen atmosphere. Al-implantation significantly reduced the oxidation rate of the TiN. The apparent activation energy for oxidation increased with increasing Al-dose. At the initial stage of oxidation, free metallic aluminum and/or new AlN-or more likely (Ti, Al)N-reacted with oxygen prior to oxidation of TiN. The thin aluminum oxide layer formed on the implanted samples was dense and free from surface flaws. This layer is thought to act as a barrier to oxygen migration protecting the TiN film from further oxidation. The diffusion of Al-atoms was a driving mechanism to activate the protection of TiN at high oxidation temperatures. The alteration of the oxidation kinetics and mechanism of the implanted TiN in an oxygen atmosphere is a consequence of the effective modification of oxide properties through Al incorporation.
Surface & Coatings Technology, 2004
... Tatsuhiko Aizawa Corresponding Author Contact Information , E-mail The Corresponding Author ,... more ... Tatsuhiko Aizawa Corresponding Author Contact Information , E-mail The Corresponding Author , a , Thananan Akhadejdamrong a and Atsushi Mitsuo b. ... of typical nitride ceramic coating with comparison to the carbide-coated and DLC-coated tools when using the ball-on-disc ...
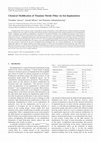
Materials Transactions, 2003
Titanium nitride, TiN is a typical ceramic coating film for cutting tools and dies; it often suff... more Titanium nitride, TiN is a typical ceramic coating film for cutting tools and dies; it often suffers from low oxidation temperature and high friction coefficient and wear volume. Its wearing and oxidation resistance is drastically improved by chemical modification via ion implantation. Carbon-, aluminum-and chlorine-ion implantation is introduced to describe the difference in the modified microstructure at the vicinity of surface. Ion-plated TiN films on a high-speed tool steel substrate are employed as a common specimen to be implanted. Each modified titanium nitride has its intrinsic, as-implanted nanostructure to the selected species. In the carbon implantation, the near-surface structure of TiN film is modified to have the layered bonding state with Ti-C/C-C/Ti-C. The Al-implantation modifies TiN to have non-equilibrium solid solution phase of (Ti, Al) N and metallic aluminum cluster. No change is seen in the chlorine implanted TiN except for increase of dislocations or point defects. The wear resistance is improved by the above as-implanted nano-structuring in the case of carbon implantation. Al-and Cl-implantation significantly improves the original oxidation and wearing resistance of TiN by the post-implantation nano-structuring. The stable, dense aluminum oxide layer is in-situ formed as a tight protective shield during the oxidation test by surface reaction between penetrating oxygen and diffusing aluminum. The lubricious titanium oxide film is also in-situ formed in the wear track at the presence of chlorine to sustain low friction and wear rate even in dry, severe wearing conditions.
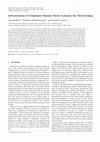
Materials Transactions, 2003
Various kinds of lubricants are utilized in every aspect of manufacturing for mass production. To... more Various kinds of lubricants are utilized in every aspect of manufacturing for mass production. To prolong the life time of tools or dies, much amount of lubricants must be used for mechanical machining or metal forming, resulting in massive emission of wasted lubricants. Dematerialization in the environmentally benign manufacturing requires less use and less emission of lubricants as possible to significantly reduce the environmental burden. For that purpose, dry machining or dry metal forming becomes a challenging issue to be solved. In the present paper, new tribological coating design is proposed to significantly reduce the wear volume and friction coefficient and to minimize the emission of wastes in wear. Titanium nitride coating has been widely used for protection of dies and tools from severe wear. Due to high friction coefficient and less wear endurance, adhesive wear often takes place against the stainless steel or ductile metallic alloy counter parts. Hence, even using this type of protective coating, lubricants are indispensable to reduce the friction coefficient and to be free from metallic sticking. Self-lubrication mechanism can be imprinted into titanium nitride coating only by chlorine implantation into it. Under the presence of chlorine in the wear track, the plastically deforming intermediate oxide film is in-situ formed to sustain low friction and low wearing mode in the relatively wide range of normal pressure and sliding velocity on the contact surface. Through the feasibility study, total amount of chlorine used for this self-lubrication is found to be negligibly small, but the self-lubrication mechanism is sustained to be working until the initial titanium nitride coating is completely worn out from the substrate.
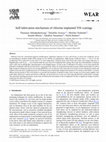
Wear, 2003
Different from the conventional physical modifications, significant reduction of wear and frictio... more Different from the conventional physical modifications, significant reduction of wear and friction in severe dry conditions can be accommodated to titanium nitride (TiN) coating via the chlorine ion implantation. High friction coefficient with µ = 0.8-1.2 for the as-deposited TiN is reduced to be less than 0.2 at room temperature. Titanium mono-oxide (TiO) and oxides with oxygen deficiency or Magnèli phase with Ti n O 2n−1 , were formed inside the wear track of Cl-implanted TiN coating. Due to the shear deformability of titanium mono-oxide and crystallographic shearing planes in this Magnèli phase, vicinity of the Cl-implanted TiN surface can be elasto-plastically deformed, resulting in reduction of shear stress, wear and friction. Micro-X-ray photoelectron spectroscopy (XPS) measurement as well as high-resolution transparent electron microscopy (HRTEM), were an effective tool to describe local surface reaction taking place inside and outside of the wear track. Oxidation process of TiN during wear is drastically changed at the presence of Cl-atoms on the surface. Cl-atoms diffuse from the inside of TiN to the surface to accelerate the formation of titanium oxides, and to escape out of the system together with oxide debris. Both wear volume and friction coefficient, are preserved to be as low as or lower than diamond like carbon (DLC) coatings. This preferable tribological property comes from self-lubrication mechanism of the Cl-implanted TiN due to significant change of surface reaction by the effect of Cl-atoms.
Journal of The American Ceramic Society, 2004
Chlorine implantation into TiN coatings decreases the wear loss and the friction coefficient. Eve... more Chlorine implantation into TiN coatings decreases the wear loss and the friction coefficient. Even by low-dose chlorine implantation, the wear volume is decreased by three orders of magnitude or more, and the friction coefficient becomes <0.1. This self-lubrication mechanism is related to the presence and mobility of implanted chlorine atoms inside the columnar TiN microstructure. According to observations of chlorine-implanted TiN coatings using high-resolution transmission electron microscopy, the chlorine atoms are present in the damaged region, where TiN is composed of nanosized grains. From these data, a self-lubrication mechanism is proposed with chlorine catalyzing the oxidation of titanium and leading to the formation of some tribological reaction product.
Uploads
Papers by Thananan Akhadejdamrong