Papers by Vadim Silberschmidt
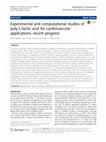
Mechanics of Advanced Materials and Modern Processes, Jul 25, 2017
Stents are commonly used in medical procedures to alleviate the symptoms of coronary heart diseas... more Stents are commonly used in medical procedures to alleviate the symptoms of coronary heart disease, a prevalent modern society disease. These structures are employed to maintain vessel patency and restore blood flow. Traditionally stents are made of metals such as stainless steel or cobalt chromium; however, these scaffolds have known disadvantages. An emergence of transient scaffolds is gaining popularity, with the structure engaged for a required period whilst healing of the diseased arterial wall occurs. Polymers dominate a medical device sector, with incorporation in sutures, scaffolds and screws. Thanks to their good mechanical and biological properties and their ability to degrade naturally. Polylactic acid is an extremely versatile polymer, with its properties easily tailored to applications. Its dominance in the stenting field increases continually, with the first polymer scaffold gaining FDA approval in 2016. Still some challenges with PLLA bioresorbable materials remain, especially with regard to understanding their mechanical response, assessment of its changes with degradation and comparison of their performance with that of metallic drug-eluting stent. Currently, there is still a lack of works on evaluating both the pre-degradation properties and degradation performance of these scaffolds. Additionally, there are no established material models incorporating non-linear viscoelastic behaviour of PLLA and its evolution with in-service degradation. Assessing these features through experimental analysis accompanied by analytical and numerical studies will provide powerful tools for design and optimisation of these structures endorsing their broader use in stenting. This overview assesses the recent studies investigating mechanical and computational performance of poly(l-lactic) acid and its use in stenting applications.
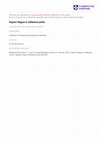
Key Engineering Materials, Oct 1, 2008
One of the forms of a vibro-impact effect in engineering components is impact fatigue (IF) caused... more One of the forms of a vibro-impact effect in engineering components is impact fatigue (IF) caused by a cyclic repetition of low energy, low-velocity impacts, for instance, in aerospace structures. It can have a highly detrimental impact on performance and reliability of such components, exacerbated by the fact that in many cases it is disguised in loading histories by non-impact loading cycles with higher amplitudes. Since the latter are traditionally considered as most dangerous in standard fatigue, IF has not yet received deserved attention; it is less studied and practically unknown to specialists in structural integrity. Though there is a broad understanding of the danger of high-energy single impacts, repetitive impacting of components has been predominantly studied for very short series. This paper aims at the analysis of IF of adhesively bonded joints, which are becoming more broadly used in aerospace applications. The study is implemented for two types of typical adherends-an aluminium alloy and a carbon-fibre reinforced composite-and an industry-relevant epoxy adhesive. Various stages of fatigue crack development in adhesively bonded joints are studied for the conditions of standard and IF. The results obtained-in terms of crack growth rates, fatigue lives, and microstructures of fracture surfaces-are compared for the two regimes in order to find similarities and specific features.
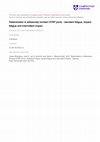
Composites Science and Technology, Sep 1, 2008
The response of adhesive joints to three fatigue regimes, namely; constant amplitude sinusoidal l... more The response of adhesive joints to three fatigue regimes, namely; constant amplitude sinusoidal loading (standard fatigue, SF), cyclic in-plane impacts (impact fatigue, IF) and a combination of the two (CSIF), has been investigated. The samples used in this study were carbon fibre reinforced polymer (CFRP) lap-strap joints (LSJs) bonded with a rubber modified epoxy adhesive. It was observed that fatigue fracture at very low load amplitudes occurred in IF. Two main patterns of failure were observed in SF; cohesive failure in the adhesive, which was linked to slow fatigue crack growth behaviour, and a mixed-mode failure, involving failure in both the adhesive and the CFRP. In addition, it was observed that the transition from cohesive to mixed mode failure was accompanied by crack growth acceleration. In IF it was seen that all failure was of a mixed-mechanism nature. In the combined standard and impact fatigue it was seen that the introduction of a relatively small number of impacts between SF blocks drastically changed the dynamics of fatigue crack propagation, increasing the crack rate. A further observation was that cavitation of rubber particles in the adhesive, which is seen as evidence of active toughening, was affected by the addition of impact loading.
WIT transactions on engineering sciences, 1970
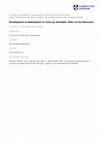
Key Engineering Materials, Jun 1, 2009
Various aspects of the effect of microstructural randomness exhibited by carbon fibrereinforced c... more Various aspects of the effect of microstructural randomness exhibited by carbon fibrereinforced cross-ply laminates on the delamination damage mechanism is investigated in this paper. In the first part, the matrix cracks with different spacings measured in experiments are simulated using finite elements in order to obtain the levels of degradation and effective properties for a composite beam loaded in bending. The results show significant levels of degradation of obtained effective properties depicting the importance of accounting for the inherent stochasticity in these laminates. In the second part of the paper, initiation of delamination at an interface between 0° and 90° layers due to stress concentrations at tips matrix cracks is simulated for a beam under tension. Stochastic cohesive zone elements with fracture parameters presented as random fields are used to model this interface in a composite. Different values of the axial stress are obtained for initiation of damage for a number of realisations based on this approach. The results emphasize the need to take into consideration the microstructural randomness in fibre-reinforced laminates for adequate predictions of damage and load carrying capacities.
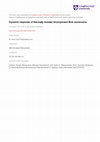
Applied Mechanics and Materials, Aug 1, 2011
Having a unique microstructure, nonwoven fabrics possess distinct mechanical properties, dissimil... more Having a unique microstructure, nonwoven fabrics possess distinct mechanical properties, dissimilar to those of woven fabrics and composites. This paper aims to introduce a methodology for simulating a dynamic response of core/sheath-type thermally bonded bicomponent fibre nonwovens. The simulated nonwoven fabric is treated as an assembly of two regions with distinct mechanical properties. One region-the fibre matrixis composed of non-uniformly oriented core/sheath fibres acting as link between bond points. Non-uniform orientation of individual fibres is introduced into the model in terms of the orientation distribution function in order to calculate the structure's anisotropy. Another regionbond pointsis treated in simulations as a deformable bicomponent composite material, composed of the sheath material as its matrix and the core material as reinforcing fibres with random orientations. Time-dependent anisotropic mechanical properties of these regions are assessed based on fibre characteristics and manufacturing parameters such as the planar density, core/sheath ratio, fibre diameter etc. Having distinct anisotropic mechanical properties for two regions, dynamic response of the fabric is modelled in the finite element software with shell elements with thicknesses identical to those of the bond points and fibre matrix.
Materials, Apr 8, 2022
This article is an open access article distributed under the terms and conditions of the Creative... more This article is an open access article distributed under the terms and conditions of the Creative Commons Attribution (CC BY
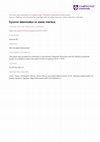
Composite Structures, Feb 1, 2020
The dynamic energy release rate (ERR) is derived for a delamination on the interface between a pa... more The dynamic energy release rate (ERR) is derived for a delamination on the interface between a partially supported vibrating beam and an elastic foundation, with a time-dependent displacement applied to the beam's free end. The configuration may represent, for example, the dynamic delamination of a laminated composite, or the cracking of a typical adhesively bonded composite joint. The developed theory is completely analytical and applicable to both symmetric double cantilever beams (DCBs) and thin layers on thick substrates. It was discovered that the dispersive propagation of flexural waves should be considered in order to capture contributions to the ERR from higher-order vibration modes. The developed theory is verified using finite-element-method (FEM) simulations and they are found to be in excellent agreement. This work will be useful to characterize the dynamic fracture toughness of layered materials in DCB tests, and to determine the fracture behavior of engineering structures under dynamic loads. Furthermore, the partially supported beam's elastic foundation is relevant for the study of crack process zones, which are usually analyzed using the FEM and the cohesivezone model. The potential applications of this study include determining the dynamic fracture toughness for crack initiation in laminated composite DCBs and adhesively bonded structures.
Journal of Computational Design and Engineering
Fibrous networks are abundant in nature and commonly used in industry. However, their geometrical... more Fibrous networks are abundant in nature and commonly used in industry. However, their geometrical modelling is challenging due to their complex microstructure. In this study, a novel method, called fibre placement method (FPM), is developed. In contrast to the existing methods, the FPM has various advantages, such as a fully parametric definition of structure. Also, this method is superior in mimicking the stochastic microstructure of fibrous networks compared with other schemes. Various fibrous networks can be generated easily by employing a user-friendly graphical user interface. Also, the generated fibrous networks are compatible with analysis software such as computer-aided engineering tools. Finally, this algorithm characterizes various features of networks including uniformity, void area fraction, and average curliness.
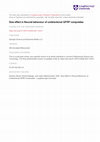
Journal of Mechanical Science and Technology, 2020
In this paper, the size effect in unidirectional (UD) laminated glass-fibre reinforced plastic (G... more In this paper, the size effect in unidirectional (UD) laminated glass-fibre reinforced plastic (GFRP) composites subjected to quasi-static bending loading was investigated: the sensitivity of a specimen's mechanical behaviour and failure mechanism to its geometry was studied. Composite beams with different numbers of 0° unidirectional plies were tested and their post-deformation structures were analysed microscopically. In the subsequent simulations, the intraply damage was modelled using continuum damage mechanics, implemented as a user-defined VUMAT subroutine in ABAQUS/Explicit, while cohesive zone elements were employed to characterize the delamination between different plies. It was observed that the flexural failure triggered the multiple delaminations; their location was studied. The influence of the size effect on the bending response of the UD composite beams was analysed in depth. The findings of the current study can be used to design modern structures made of composite materials.
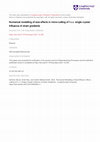
Journal of Manufacturing Processes, 2022
A size effect is exhibited by metals in cutting processes at small scales: a nonlinear escalation... more A size effect is exhibited by metals in cutting processes at small scales: a nonlinear escalation in the cutting energy per unit volume with a decrease in the thickness of uncut chip. To understand this phenomenon, a numerical model of orthogonal micro-cutting of f.c.c. single-crystal copper was developed, where three different depths of cut (0.8 μm, 1.4 μm and 2.0 μm) were considered. Enhanced models of crystal plasticity (EMCP) and strain-gradient crystal plasticity (EMSGCP) implemented in ABAQUS/Explicit through a VUMAT Fortran subroutine were used. Obtained results were compared with the experiments reported in the literature. The influence of size effect on deformation response of a single-crystal material was investigated extensively in terms of the distribution of field variables such as strain gradients, stresses, lattice rotations and activity of different slip systems. The influence of crystallographic orientation was also studied in the last part. It was observed that the size effect phenomenon was predicted more accurately with the EMSGCP theory, where polar dislocations evolving during deformation was found to affect it significantly.
Encyclopedia of Continuum Mechanics, 2020
The modeling and simulation of the nonlinear mechanical response of laminated composites is treat... more The modeling and simulation of the nonlinear mechanical response of laminated composites is treated. In the present context, a laminate consists of several stacked plies. Here, the smallest entities of consideration are the plies and their interfaces. Both are described by nonlinear elasto-damage constitutive laws. A number of approaches are introduced at material and interface level. Their utilization for structural simulations is discussed, including predictions for the response beyond peak load.
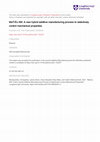
Additive Manufacturing, 2021
This study is the first to demonstrate how mechanical and geometrical properties of polylactide (... more This study is the first to demonstrate how mechanical and geometrical properties of polylactide (PLA) and acrylonitrile butadiene styrene (ABS) additively manufactured with material extrusion can be selectively tailored using a newly devised treatment method of chemical immersion in acetone. This combination of manufacturing and chemical treatment results in a hybrid process capable of modifying mechanical behaviour in a predictable and time-controlled manner. Key new understanding is generated by analysing short-term effects (tested immediately after immersion) on mechanical and geometrical properties of printed specimens, with different immersion times (1 to 60 seconds) causing significant increases in strain-at-fracture-up to 25-and 16-fold for PLA and ABS, respectively. In the long-term mechanical properties were found to recover by up to 90% of those for untreated specimens in ABS within 3 hours, while PLA properties recovered after 60 days. Importantly, while mechanical properties in both PLA and ABS recovered, the geometrical changes were retained. Annealing allowed the recovery time to be shortened: PLA specimens achieved full recovery within 24 hours. Chemical immersion provides significant advantages over widely used vapour-based treatment methods, since it allows selective application to achieve and localised changes of mechanical and geometrical properties. Applications of this new hybrid process, called Material Treatment Extrusion Additive Manufacturing (MaTrEx AM), are presented, including the capability to add new functionality (dramatically increased plasticity) to material structures manufactured with PLA and ABS. The implementation of MaTrEx AM as a hybrid manufacturing system is demonstrated. MatrEX AM enabled selective, localised modification of mechanical properties to increase toughness and redirect strain into selected regions of a mesh material.
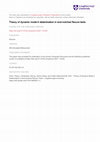
Composite Structures, 2021
The dynamic mode-II energy release rate of the end-notched flexure (ENF) test with applied time-d... more The dynamic mode-II energy release rate of the end-notched flexure (ENF) test with applied time-dependent displacement is derived for the first time with the effect of vibration included. A dynamic Euler-Bernoulli beam theory is employed together with a deflection condition to simulate contact. To investigate the dynamic effect and the relative dynamic contribution from each vibration mode, a dynamic factor and a spatial factor are defined. It is found that the contribution of the ith vibration mode is dependent on the spatial factor (which is a function of the delamination length and the total length of the ENF specimen) and that certain vibration modes are dominant (depending on the delamination-length ratio). In addition, for a given spatial factor, there may be a certain vibration mode with a zero contribution to the ERR. The developed theory is verified against results from finite-element-method simulation for two cases of ENF tests and they are in excellent agreement. This work now allows the loading ratedependent mode-II delamination toughness of layered materials to be determined using ENF tests. In addition, it provides understanding of the structural dynamic response in the presence of mode-II delamination and can guide the design of structures to mitigate the vibration-driven delamination.
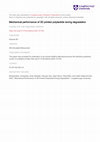
Additive Manufacturing, 2021
Although widely-used biodegradable polymers have been extensively studied for conventional manufa... more Although widely-used biodegradable polymers have been extensively studied for conventional manufacturing processes, this is the first study considering the effect of interfacial bonds between extruded filaments-the most important aspect related to additive manufacturingon degradation at 37°C. Its results improve the confidence in the material extrusion additive manufacturing process and negate one of the crucial unknown factors for bioresorbable products, by demonstrating that the interface degrades in a similar manner to the bulk polymer material. To do this, specially designed micro-tensile specimens were developed to analyse the degradation of 3D-printed parts for the first time at 37°C and accelerated temperatures. The mechanical properties of the interface between extruded filaments (Z specimen) were compared against the control, i.e. along filaments (F specimen), under medically relevant testing conditions (submerged at 37°C). Monitoring the degradation of tensile strength showed that both specimen types behaved similarly, exhibiting an initial induction period followed by a reduction in properties. Comparison of thermal and chemical properties revealed that during the early stage of degradation, crystallinity was the dominating factor, whilst at later stages, mechanical properties were mainly defined by the molecular weight and autocatalytic degradation. The findings suggest that understanding developed in the long-standing field of polymer degradation can be applied to additive-manufactured medical devices, which unavoidably contain interlayer interfaces.
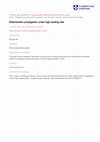
Composite Structures, 2020
Analytical theory for the dynamic delamination behavior of a double cantilever beam (DCB) under h... more Analytical theory for the dynamic delamination behavior of a double cantilever beam (DCB) under high loading rate is developed. Structural vibration and wave dispersion are considered in the context of Euler-Bernoulli beam theory. The theory is developed for both initiation and propagation of delamination in mode I. Two solutions for the energy release rate (ERR) are given for a stationary delamination: an accurate one and a simplified one. The former is based on global energy balance, structural vibration and wave dispersion; the latter is 'local' since it is based on the crack-tip bending moment. For the simplified solution to be accurate, sufficient time is needed to allow the establishment of all the standing waves. For a propagating delamination, a solution for the ERR is derived using the same simplification with the cracktip bending moment. The obtained ERR solutions are verified against experimental data and results from finite-element simulations, showing excellent agreement. One valuable application of the developed theory is to determine a material's dynamic loading-ratedependent delamination toughness by providing the analytical theory to post-process test results of dynamic DCB delamination.
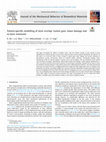
Journal of the Mechanical Behavior of Biomedical Materials, 2020
This paper investigates the effects of multiple stents, with and without overlap, on the outcome ... more This paper investigates the effects of multiple stents, with and without overlap, on the outcome of stent deployment in a patient-specific coronary artery using the finite element method. Specifically, the objective of this study is to reveal the effect of stent overlap on lumen gain, tissue damage and in-stent restenosis in percutaneous coronary intervention. Based on intravital optical coherency tomography imaging, threedimensional model of a specific patient's coronary artery was developed, with two constituent layers (media and adventitia) and plaque, using Mimics. Hyperelastic models with damage, verified against experimental results, were used to describe stress-stretch responses of arterial layers and plaque. Abaqus CAE was used to create the models for Resolute Integrity™ drug-eluting stents and tri-folded expansion balloons. The results showed that lumen gain was improved by the overlapping stents than a single stent after deployment; however, damage to the media layer was greater, promoting a higher rate of in-stent restenosis. Meanwhile, the lumen gain achieved with the non-overlapping stents was smaller than that with the overlapping ones, due to an increased recoiling effect. Also, non-overlapping stents induced more tissue damage and higher rate of in-stent restenosis than overlapping stents. With respect to long-term clinical outcomes, the study recommended the use of a single stent where possible or multiple stents with minimal overlaps to treat long or angulated lesions.
Additive Manufacturing, 2020
The deposited filament, from which the 3d printed specimens are comprised (sometimes referred to ... more The deposited filament, from which the 3d printed specimens are comprised (sometimes referred to as rasters, fibres, roads, tracks or extrudates in other studies). Extruded-filament geometry: The cross-sectional geometry of the extruded filament. EFW: Extruded-filament width F: Filament direction (sometimes referred to as longitudinal direction in other studies-parallel to the print bed) Interface: The region of joining between two extruded filaments. Interlayer bonding: The interfacial bonding between layers (extruded filaments). LH: Layer height Load-bearing area: The cross-sectional area of the specimen, which bears mechanical load. Specific load-bearing capacity: The maximum load capacity of specimens normalised by the weight of the unit length of the specimen gauge. Z: Z-direction (normal-to-filament direction and normal to the print bed).
Engineering Fracture Mechanics, 2020
Is mechanical anisotropy in extrusion-based 3D-printed parts caused by weak interfilament bonding... more Is mechanical anisotropy in extrusion-based 3D-printed parts caused by weak interfilament bonding, as is widely accepted? This study demonstrates that filament-scale geometric features may be a more important factor than filament bonding. Specially designed 3D-printed compact tension specimens were tested normal to, and along, the direction of extruded filaments. Higher strength and resilience were found in the filament direction. These differences disappeared when small grooves, comparable to micro-features, were introduced in specimens tested along the former direction to replicate grooves that naturally occur between filaments/layers. Mechanical testing and fractography demonstrate that filament-scale geometric stress raisers are critically important and cause anisotropy in 3D-printed materials.
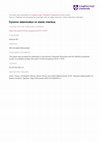
Composite Structures, 2019
The dynamic energy release rate (ERR) is derived for a delamination on the interface between a pa... more The dynamic energy release rate (ERR) is derived for a delamination on the interface between a partially supported vibrating beam and an elastic foundation, with a time-dependent displacement applied to the beam's free end. The configuration may represent, for example, the dynamic delamination of a laminated composite, or the cracking of a typical adhesively bonded composite joint. The developed theory is completely analytical and applicable to both symmetric double cantilever beams (DCBs) and thin layers on thick substrates. It was discovered that the dispersive propagation of flexural waves should be considered in order to capture contributions to the ERR from higher-order vibration modes. The developed theory is verified using finite-element-method (FEM) simulations and they are found to be in excellent agreement. This work will be useful to characterize the dynamic fracture toughness of layered materials in DCB tests, and to determine the fracture behavior of engineering structures under dynamic loads. Furthermore, the partially supported beam's elastic foundation is relevant for the study of crack process zones, which are usually analyzed using the FEM and the cohesivezone model. The potential applications of this study include determining the dynamic fracture toughness for crack initiation in laminated composite DCBs and adhesively bonded structures.
Uploads
Papers by Vadim Silberschmidt