Papers by Leslie Banks-sills
(a) For the geometry in Figure. 1, determine an explicit expression for the stress intensity fact... more (a) For the geometry in Figure. 1, determine an explicit expression for the stress intensity factors K1 and K2. (b) From the displacement field, determine the largest value of r = rc for which Δ v = 0. In the calculations, consider that the material in the upper half-plane is glass with Young’s modulus E1 = 73.0 GPa and Poisson’s ratio vl = 0.22; the material in the lower half-plane is epoxy with E2 = 2.94GPa and v2 = 0.29. (c) For crack tips A and B in Fig.1, determine rc for a = 10 mm. (d) Using the fracture criterion which fits the experimental data in Fig. 2, determine the critical stress, σcrit, for τ = 3σ and a = 10mm.
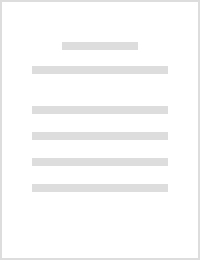
Fatigue & Fracture of Engineering Materials & Structures, Aug 22, 2021
The coupled energy release rate may be used with the virtual crack closure technique (VCCT) metho... more The coupled energy release rate may be used with the virtual crack closure technique (VCCT) method to determine the stress intensity factors of interface cracks. Different equations were presented over the years using this parameter. In recent papers, a new approach was presented by the authors. This approach includes two additional energy release rates, called here, the dual energy release rates. Here, the coupled and dual energy release rates are explored and well established. This leads to a new and more suitable equation for calculating the mode mixity or phase angle. In addition, a geometrical interpretation between the energy release rates for both homogeneous and interface crack problems is found. A problem of an interface crack between two linear elastic, isotropic, and homogeneous materials in an infinite body is presented. This problem emphasizes the advantage of the new equation, and the geometrical relation between the energy release rates is illustrated.
Springer eBooks, 2003
Write the general expression for the J-integral for anti-plane shear, i.e. mode III. Using the do... more Write the general expression for the J-integral for anti-plane shear, i.e. mode III. Using the dominant elastic singularity, shrink the J-contour down to the crack tip and prove, by direct calculation, that
Elsevier eBooks, 1989
ABSTRACT A compact mode II fracture specimen was previously employed to determine K IIc of perspe... more ABSTRACT A compact mode II fracture specimen was previously employed to determine K IIc of perspex. For a more ductile material such as aluminum, linear elastic fracture mechanics concepts cannot be employed. To this end, the specimen was calibrated for J-integral testing, so that J IIc measurements can be carried out. In this study, tests are performed on an aircraft aluminum, 7075-T7351. J Ic is determined to be 10.5 kN/m and a tentative value of J IIc is found to be 25 kN/m.
Theoretical and Applied Fracture Mechanics, Jun 1, 2022
Engineering Fracture Mechanics, 2023
Theoretical and Applied Fracture Mechanics, Dec 1, 2022
(a) By means of the weight function, determine an integral expression for the stress intensity fa... more (a) By means of the weight function, determine an integral expression for the stress intensity factor of the geometry and loading shown in Fig. 1. Assume plane strain conditions. (b) Carry out the integration to obtain an explicit expression for K 1 .
Springer eBooks, 2003
(a) For the geometry in Figure. 1, determine the direction of crack propagation according to the ... more (a) For the geometry in Figure. 1, determine the direction of crack propagation according to the maximum tangential stress criterion of Erdogan and Sih [1]. (b) Sketch this direction on a figure. (c) Determine the critical stress at fracture, σcrit. (d) Estimate the plastic zone size at fracture adjacent to the crack tip. Explain if the stress intensity factor may be employed to predict crack propagation.
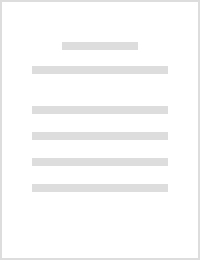
Veterinary and comparative orthopaedics and traumatology, Jul 1, 2003
SummaryThe long-term performance of total hip replacement is of concern to veterinary surgeons. T... more SummaryThe long-term performance of total hip replacement is of concern to veterinary surgeons. Two of the main complications associated with this procedure are implant loosening and stress shielding. Designs of the femoral stem which will avoid loosening and achieve maximum endurance while reducing stress shielding and periprosthetic bone loss are sought.In the intact femur the stress is distributed over the entire cross section of the bone. After hip replacement this pattern of stress distribution is altered because of the manner in which the load is transferred from the prosthesis to the bone.The objective of this study was to examine the stresses that develop in the femur and implant components of two different methods of hip replacement used clinically in dogs. Anatomic, three-dimensional finite element models of the canine femur with a cemented femoral stem and a Zurich cementless stem were constructed. The stresses and displacements were calculated by the finite element analysis method, under physiologic loads that included muscle forces and joint reaction forces. The results were compared to results obtained by a similar analysis of an intact femur.This study demonstrates that the Zurich cementless method causes less stress shielding in the proximal femoral cortex than does the cemented method. Implant stresses are higher in the Zurich cementless stem, but still within an acceptable range.

International Journal of Fracture, Feb 14, 2017
The virtual crack closure technique makes use of the forces ahead of the crack tip and the displa... more The virtual crack closure technique makes use of the forces ahead of the crack tip and the displacement jumps on the crack faces directly behind the crack tip to obtain the energy release rates G I and G I I. The method was initially developed for cracks in linear elastic, homogeneous and isotropic material and for four noded elements. The method was extended to eight noded and quarter-point elements, as well as bimaterial cracks. For bimaterial cracks, it was shown that G I and G I I depend upon the virtual crack extension Δa. Recently, equations were redeveloped for a crack along an interface between two dissimilar linear elastic, homogeneous and isotropic materials. The stress intensity factors were shown to be independent of Δa. For a better approximation of the Irwin crack closure integral, use of many small elements as part of the virtual crack extension was suggested. In this investigation, the equations for an interface crack between two dissimilar linear elastic, homogeneous and transversely isotropic materials are derived. Auxiliary parameters are used to prescribe an optimal number of elements to be included in the virtual crack extension. In addition, in previous papers, use of elements smaller than the interpenetra
SpringerBriefs in applied sciences and technology, Jul 6, 2017
In this chapter, aspects of the finite element method for obtaining the displacement field of a b... more In this chapter, aspects of the finite element method for obtaining the displacement field of a body containing an interface crack are described. Square-root singular, quarter-point elements in two and three dimensions will be presented. Once the displacement field is found three methods are suggested for computing stress intensity factors; they include the displacement extrapolation (DE) method, the conservative interaction energy integral or M-integral, and the Virtual Crack Closure Technique (VCCT). The stress intensity factors are then employed to obtain the interface energy release rate and two phase angles.
ASTM International eBooks, Feb 12, 2009
In this investigation, an exact three-dimensional weight function is developed for the elliptical... more In this investigation, an exact three-dimensional weight function is developed for the elliptical crack family. Closed form expressions for the weight function of the penny-shaped and elliptical crack in an infinite body subjected to symmetric applied stresses are obtained. Several loadings are considered that lead to exact solutions which agree with those in the literature. Since crack-opening displacements for more complicated crack geometries do not appear in the literature, an approximate weight function is proposed. When applied to the geometries with known solutions, excellent agreement is obtained. When employed to determine the stress-intensity factor for a semielliptical and quarter-elliptical crack in a plate subjected to bending stresses, it produces results which are good for short cracks.
International Journal of Fracture, May 26, 2022
International Journal of Fracture, 1999
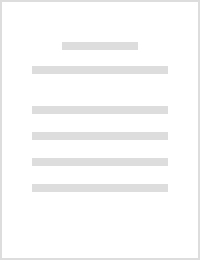
Fatigue & Fracture of Engineering Materials & Structures, Jan 5, 2023
The purpose of this investigation is to evaluate the contribution of fiber bridging to the energy... more The purpose of this investigation is to evaluate the contribution of fiber bridging to the energy release rate of a fracture resistance curve. Fiber bridging occurs when testing beam‐type specimens consisting of unidirectional plies in a laminate. Unidirectional double cantilever beam specimens composed of the carbon fiber reinforced polymer prepreg AS4/8552 were tested using standard methods. In addition, a cohesive zone model was developed and used to carry out finite element analyses on the tested specimens. It was employed to calculate the contribution of fiber bridging to the ‐curve which was determined from the tests. Fiber bridging in beam specimens increases the apparent fracture toughness of a composite laminate. A method has been proposed for evaluating its contribution to the energy release rate. In that way, an ‐curve may be determined for which the effect of fiber bridging is eliminated.
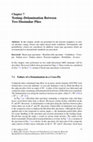
SpringerBriefs in applied sciences and technology, Jul 6, 2017
In this chapter, results are presented for the fracture toughness or critical interface energy re... more In this chapter, results are presented for the fracture toughness or critical interface energy release rate under mixed mode conditions. Deterministic and probabilistic criteria are considered. In addition, beam type specimens which are recommended in international standards are presented. Keywords Beam type specimens • Brazilian disk specimen • Confidence • Crossply • Failure curve • Failure surface • Fracture toughness • Probability • R-curve In this chapter, tests performed on two multi-directional (MD) laminates will be described. These tests follow those presented in Chap. 4. These results are considered in Sect. 7.1. In Sect. 7.2, testing of beam type specimens is discussed. 7.1 Failure of a Delamination in a Cross-Ply Composite plies containing long fibers in an epoxy matrix prepreg AS4/3502 were formed into a cross-ply laminate. A cross-ply laminate is one in which the fibers in the adjacent plies form an angle of 90 •. A plate of this material was fabricated and composite strips containing a delamination formed from a Teflon film were machined. The delamination was along the interface between two plies: either 0 • //90 • [10] or +45 • // − 45 • [11]. In Fig. 7.1a, a Brazilian disk specimen containing a composite strip with three layers, each about 4 mm wide, is shown. The layers consist of plies with fibers in the 0 • and 90 •-directions. A delamination is indicated along the interface between plies whose fibers are in the 0 • and 90 •-directions. Partial disks of aluminum were glued to the composite strip to complete the Brazilian disk specimens. Although the load is applied only to the composite at various angles ω, the aluminum partial disks allow for easier handling of the specimen and accurate placement in the loading frame. Recall that varying the angle ω results in various mode mixities. The radius of the disk is nominally 20 mm and its nominal thickness is 8 mm. In Fig. 7.1b, a variation of the specimen in Fig. 7.1a is shown. In this specimen, the inner part of the composite strip consists of three layers with plies in the 0 • , 90 • and 0 •-directions. Each layer
SpringerBriefs in applied sciences and technology, Jul 6, 2017
In this chapter, an interface crack between two dissimilar linear elastic, homogeneous and isotro... more In this chapter, an interface crack between two dissimilar linear elastic, homogeneous and isotropic materials is considered. Methods of testing, as well as some test results are presented.
Kluwer Academic Publishers eBooks, Mar 29, 2006
The reliability of a joint subjected to mechanical and thermal loads during processing and servic... more The reliability of a joint subjected to mechanical and thermal loads during processing and service constitutes a major technical problem. Joints contain flaws. The observed strength of a joint depends upon the location and size of the flaws, as well as the crack path through the joint. The aim of this investigation is to examine the path of a crack in an adhesive bond.
Uploads
Papers by Leslie Banks-sills