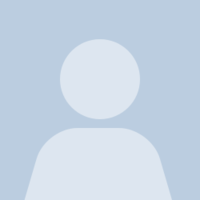
Dr. Arshad Adam Salema
I graduated as Chemical Engiener, from University of Pune, India in year 2002 and joined Agro based company as a Lab engineer. Later on I completed my M.E. Chemical, 2007 and PhD from Mechanical Engineering, from Universiti Teknologi Malaysia. I have published about 30 International and national refereed journal papers and about 20 international and national conference papers. I also reviewer for more than 15 journals such as Chemical Engineering Journal, Energy, Journal of Water and Climate, Bioresource Technology, etc. Currently, I hold Post Doctoral position at The University of New Brunswick, Canada
Supervisors: Associate Prof. Dr. Muhammad Afzal
Phone: +1-506-447-3421
Address: Department of Mechanical Engineering,
15, Dineen Drive,
The University of New Brunswick,
Room no. E12, Head Hall,
Fredericton, NB E3B 5A3, CANADA
Supervisors: Associate Prof. Dr. Muhammad Afzal
Phone: +1-506-447-3421
Address: Department of Mechanical Engineering,
15, Dineen Drive,
The University of New Brunswick,
Room no. E12, Head Hall,
Fredericton, NB E3B 5A3, CANADA
less
Related Authors
veena subramanyam
Xplore Research, University of Alberta
Christopher Koroneos
University of Western Macedonia (UOWM)
lsmail Badmus
Yaba College of Technology, Lagos. Nigeria
ibrahim hussain
Obafemi Awolowo University,Ile-Ife,Nigeria
Volkan Ediger
Kadir Has University
InterestsView All (6)
Uploads
Papers by Dr. Arshad Adam Salema
inclined feeding and inclined, tangential feeding. Experimental results showed that fly ash from both experiments were amorphous and almost similar in terms of residual carbon content (1.9 wt %). The major differences were that when feeding was done through the inclined feeding port, most of the ash was collected as fly ash and the size were coarser in the form of slightly broken skeletons. The tangential velocity component in the combustor arising from the tangential
feeding route caused the ash to be trapped at the swirling flow region above the bed, thereby retaining most of the ash particles as bottom ash. Further, the high degree of turbulence at the
swirling flow region, coupled with the high degree of rice husk penetration in the bed, resulted in fly and bottom ashes finer in size. It was concluded that combustion of rice husk by inclined
feeding method was more desirable due to the stable, uniform combustor temperatures and ease in ash collection.
(at 13–16 MJ/kg), which upon thermal degradation, releases a substantial amount of heat that is economically-viable when recovered. The recovered heat could be used for drying of
paddy or to increase steam for electricity generation. It was estimated that the potential energy generation from rice husk is 263 GWh per annum in 2000. In addition, thermal treatment of
rice husk also produces materials with commercial value in the form of siliceous rice husk ash (RHA) and activated carbon (AC). Depending on the type of thermal treatment applied, activated carbon could be generated in quantities ranging from 3–40 wt% in RHA. This paper presents research work that was undertaken in Universiti Teknologi Malaysia (UTM) to recover energy from rice husk and utilisation of its ash. The work involved controlled burning of rice husk in a fluidised bed to produce amorphous RHA which contains highly reactive silica and production of sodium silicate using RHA as raw material. Furthermore, the capability of RHA as an adsorbent and the effect of caustic digestion to produce sodium silicate on adsorption capacity of RHA were also conducted. Part 2 of this article will appear in the June - August 2009 issue of Ingenieur.
rice husk results in the formation of ash that has high commercial value due to its high silica content. Palm wastes, on the other hand, are produced in quantities exceeding the internal energy requirements for palm oil mills. Realising the good
potential of the fluidised bed technology in recovering energy from biomass, extensive research in the combustion of biomass using the fluidised bed technology is currently being carried out at Universiti Teknologi Malaysia (UTM). Different variants of the fluidised bed technology, namely the conventional bubbling fluidised bed, spouted bed (SB) and spinning fluidised bed (SFB) are being explored with the focus on the combustion of rice husk and palm wastes. This paper presents some of the results achieved from the research programmes.
fibers) with the help of char as microwave absorber (MA). Rapid heating and yield of microwave pyrolysis
products such as bio-oil, char, and gas was found to depend on the ratio of biomass to microwave absorber.
Temperature profiles revealed the heating characteristics of the biomass materials which can rapidly
heat-up to high temperature within seconds in presence of MA. Some characterization of pyrolysis products
was also presented. The advantage of this technique includes substantial reduction in consumption
of energy, time and cost in order to produce bio-oil from biomass materials. Large biomass particle size
can be used directly in microwave heating, thus saving grinding as well as moisture removal cost. A synergistic
effect was found in using MA with oil palm biomass.
inclined feeding and inclined, tangential feeding. Experimental results showed that fly ash from both experiments were amorphous and almost similar in terms of residual carbon content (1.9 wt %). The major differences were that when feeding was done through the inclined feeding port, most of the ash was collected as fly ash and the size were coarser in the form of slightly broken skeletons. The tangential velocity component in the combustor arising from the tangential
feeding route caused the ash to be trapped at the swirling flow region above the bed, thereby retaining most of the ash particles as bottom ash. Further, the high degree of turbulence at the
swirling flow region, coupled with the high degree of rice husk penetration in the bed, resulted in fly and bottom ashes finer in size. It was concluded that combustion of rice husk by inclined
feeding method was more desirable due to the stable, uniform combustor temperatures and ease in ash collection.
(at 13–16 MJ/kg), which upon thermal degradation, releases a substantial amount of heat that is economically-viable when recovered. The recovered heat could be used for drying of
paddy or to increase steam for electricity generation. It was estimated that the potential energy generation from rice husk is 263 GWh per annum in 2000. In addition, thermal treatment of
rice husk also produces materials with commercial value in the form of siliceous rice husk ash (RHA) and activated carbon (AC). Depending on the type of thermal treatment applied, activated carbon could be generated in quantities ranging from 3–40 wt% in RHA. This paper presents research work that was undertaken in Universiti Teknologi Malaysia (UTM) to recover energy from rice husk and utilisation of its ash. The work involved controlled burning of rice husk in a fluidised bed to produce amorphous RHA which contains highly reactive silica and production of sodium silicate using RHA as raw material. Furthermore, the capability of RHA as an adsorbent and the effect of caustic digestion to produce sodium silicate on adsorption capacity of RHA were also conducted. Part 2 of this article will appear in the June - August 2009 issue of Ingenieur.
rice husk results in the formation of ash that has high commercial value due to its high silica content. Palm wastes, on the other hand, are produced in quantities exceeding the internal energy requirements for palm oil mills. Realising the good
potential of the fluidised bed technology in recovering energy from biomass, extensive research in the combustion of biomass using the fluidised bed technology is currently being carried out at Universiti Teknologi Malaysia (UTM). Different variants of the fluidised bed technology, namely the conventional bubbling fluidised bed, spouted bed (SB) and spinning fluidised bed (SFB) are being explored with the focus on the combustion of rice husk and palm wastes. This paper presents some of the results achieved from the research programmes.
fibers) with the help of char as microwave absorber (MA). Rapid heating and yield of microwave pyrolysis
products such as bio-oil, char, and gas was found to depend on the ratio of biomass to microwave absorber.
Temperature profiles revealed the heating characteristics of the biomass materials which can rapidly
heat-up to high temperature within seconds in presence of MA. Some characterization of pyrolysis products
was also presented. The advantage of this technique includes substantial reduction in consumption
of energy, time and cost in order to produce bio-oil from biomass materials. Large biomass particle size
can be used directly in microwave heating, thus saving grinding as well as moisture removal cost. A synergistic
effect was found in using MA with oil palm biomass.