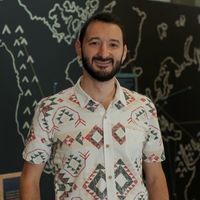
Juan Martínez
Mechanical Engineer, PhD.
J.D. Martínez works as associate professor of the Chemical Engineering Program in the Engineering School at the Pontificia Bolivariana University, (Medellín, Colombia). His interests are related to thermochemical processes (combustion, gasification and pyrolysis) of renewable and non-renewable resources, power systems, waste management and biofuels production.
J.D. Martínez works as associate professor of the Chemical Engineering Program in the Engineering School at the Pontificia Bolivariana University, (Medellín, Colombia). His interests are related to thermochemical processes (combustion, gasification and pyrolysis) of renewable and non-renewable resources, power systems, waste management and biofuels production.
less
Related Authors
Prof. Nagwa Mohamed A . Aref
Ain Shams University
M.M. Noor
Universiti Malaysia Pahang (UMP)
David Seamon
Kansas State University
Sadhan Mahapatra
Tezpur University
Armando Marques-Guedes
UNL - New University of Lisbon
Augustine O. O Ayeni
Covenant University Canaanland, Ota.
Gary Feinman
Field Museum
Ehsan Houshfar
University of Tehran
Antonio Bula
Universidad del Norte - Barranquilla, Colombia
naveen noronha
Visvesvaraya Technological University
InterestsView All (20)
Uploads
Papers by Juan Martínez
strengths not only for fast pyrolysis, but also for slow or intermediate pyrolysis. Auger pyrolyzers are of relatively simple design and overcome some of the problems of conveying heat for pyrolyzing biomass or wastes. The mechanical forces associated with auger reactors enhance particle mixing and heat transfer, which are key to successful pyrolysis. This paper presents a comprehensive review of the advantages and challenges of this technology and identify the main characteristics of both single- and twin-screw auger technology. The effect of operating conditions on yield and some properties of pyrolysis products are also provided. The review includes examples of commercial/demonstration-scale auger pyrolysis plants operated around the world.
CaCO3) used as expansion agents. The novelty of this study is the valorization of an important hazardous waste for the synthesis of a potential material for construction. All these feedstock where characterized by elemental, proximate and TG/DTG analyses and also by XRF for determining the inorganic composition. The LWA were produced from two different mixtures: i) clay and oily waste (CW) and ii) clay
and oil sludge (CS), by using different proportions of both NaHCO3 and CaCO3 (0, 20 and 40 wt%). Additionally, the influence of sintering temperature (900, 950 and 1000 °C) on the particle density was
also evaluated. Although TG/DTG analysis suggests a higher CO2 release with CaCO3 and hence, a higher bloating phenomena; there also appears an influence of the petrochemical waste composition. In addition, the particle density varied from 1.394 to 2.227 g/cm3, and from 1.226 to 2.571 g/cm3, for mixtures using CaCO3 and NaHCO3, respectively, and the lower the sintering temperature, the lower the particle density. The lowest density (1.223 g/cm3) was obtained when oily waste and NaHCO3 at 40 wt% are used (CW_NaHCO3_40). For this mixture, the synthesis process is prompted not only by the NaHCO3 addition, but also by the reaction among different elements of clay and oily waste. The resulting aggregate exhibited a foam-like structure with rounded cavities, suggesting the bloating phenomenon occurrence.
and cell-wall structure by SEM were analyzed. A severe degradation of both hemicellulose and cellulose was found at 240 °C, and a char-like material rich in lignin with high LHV is obtained. At this temperature, oxidation reactions are favored leading to highest specific surface area (174.95m2/g) at 75 min. In addition, the reactivity of torrefied biomasses were higher than the raw material; particularly, those produced at 180 and 210 °C. Likewise, their structure exhibited a higher aromaticity with torrefaction severity. Therefore, torrefaction under air conditions upgrades the quality of patula pine wood as a solid biofuel for further thermochemical processing such as combustion or gasification.
strengths not only for fast pyrolysis, but also for slow or intermediate pyrolysis. Auger pyrolyzers are of relatively simple design and overcome some of the problems of conveying heat for pyrolyzing biomass or wastes. The mechanical forces associated with auger reactors enhance particle mixing and heat transfer, which are key to successful pyrolysis. This paper presents a comprehensive review of the advantages and challenges of this technology and identify the main characteristics of both single- and twin-screw auger technology. The effect of operating conditions on yield and some properties of pyrolysis products are also provided. The review includes examples of commercial/demonstration-scale auger pyrolysis plants operated around the world.
CaCO3) used as expansion agents. The novelty of this study is the valorization of an important hazardous waste for the synthesis of a potential material for construction. All these feedstock where characterized by elemental, proximate and TG/DTG analyses and also by XRF for determining the inorganic composition. The LWA were produced from two different mixtures: i) clay and oily waste (CW) and ii) clay
and oil sludge (CS), by using different proportions of both NaHCO3 and CaCO3 (0, 20 and 40 wt%). Additionally, the influence of sintering temperature (900, 950 and 1000 °C) on the particle density was
also evaluated. Although TG/DTG analysis suggests a higher CO2 release with CaCO3 and hence, a higher bloating phenomena; there also appears an influence of the petrochemical waste composition. In addition, the particle density varied from 1.394 to 2.227 g/cm3, and from 1.226 to 2.571 g/cm3, for mixtures using CaCO3 and NaHCO3, respectively, and the lower the sintering temperature, the lower the particle density. The lowest density (1.223 g/cm3) was obtained when oily waste and NaHCO3 at 40 wt% are used (CW_NaHCO3_40). For this mixture, the synthesis process is prompted not only by the NaHCO3 addition, but also by the reaction among different elements of clay and oily waste. The resulting aggregate exhibited a foam-like structure with rounded cavities, suggesting the bloating phenomenon occurrence.
and cell-wall structure by SEM were analyzed. A severe degradation of both hemicellulose and cellulose was found at 240 °C, and a char-like material rich in lignin with high LHV is obtained. At this temperature, oxidation reactions are favored leading to highest specific surface area (174.95m2/g) at 75 min. In addition, the reactivity of torrefied biomasses were higher than the raw material; particularly, those produced at 180 and 210 °C. Likewise, their structure exhibited a higher aromaticity with torrefaction severity. Therefore, torrefaction under air conditions upgrades the quality of patula pine wood as a solid biofuel for further thermochemical processing such as combustion or gasification.